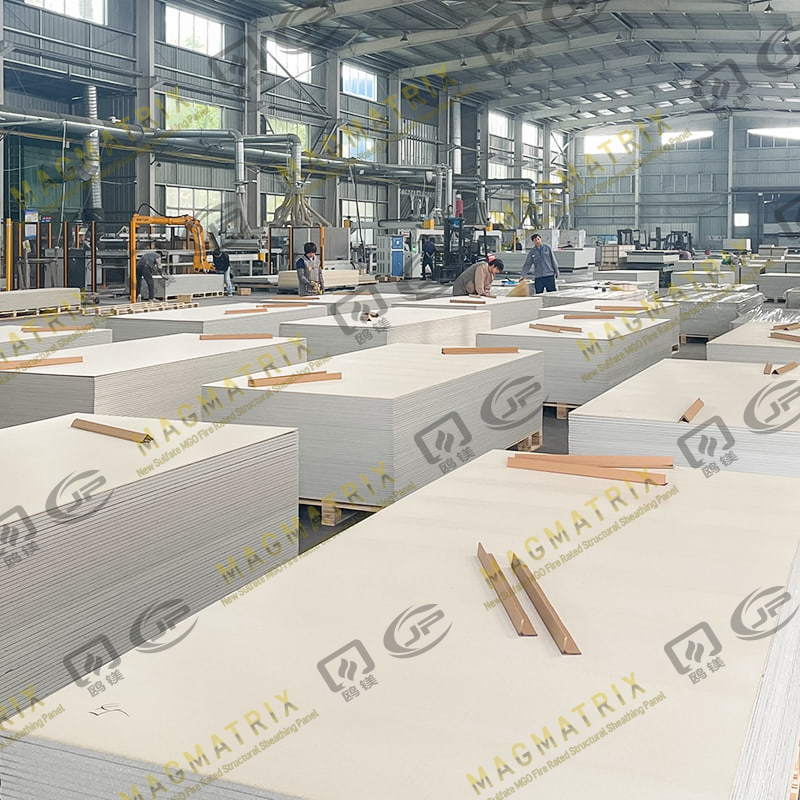
MgO board technology has become a game-changer in construction with its remarkable fire resistance. These boards can withstand temperatures up to 1200°F without toxic fumes. The global market shows a clear change in building material priorities. Experts project magnesium oxide board sales to reach USD 2,372.7 million by 2030.
MgO boards stand far apart from traditional drywall in performance. Their fire rating extends to 4 hours, while drywall tops out at just 1 hour. These magnesium boards excel in moisture resistance too. They stay waterproof and mold-free in humid conditions where regular drywall fails and warps.
The cost difference between MgO boards and drywall is notable. MgO boards cost $1.50 to $3.50 per square foot, compared to drywall's $0.50 to $1.00 range. Yet their durability, strength, and eco-friendly features make them worth considering. These boards use natural, recyclable materials that reduce carbon footprint. Their thermal insulation properties help cut down energy costs over time.
This detailed cost analysis will get into how these differences affect your 2025 construction projects. You'll learn to balance initial costs with long-term benefits to make smart choices.
Material Overview: MgO Board vs Drywall
The distinct performance characteristics of MgO boards and traditional drywall stem from their fundamental differences in composition. These materials might look like they do the same job, but their internal structures tell us a completely different story.
Composition of magnesium oxide (MgO) board
Magnesium oxide (MgO), a naturally occurring mineral, makes up most of the board's core foundation. Strong bonds between magnesium and oxygen atoms create crystals that give the board substantial strength and resistance.
MgO boards need several key ingredients in their recipe:
Magnesium Sulfate (MgSo4): Mixes with magnesium oxide to create a cement as MagMatrix’s BMSC 517 sulfate magnesium cementitious slurry that binds everything together
Perlite: This volcanic glass makes the board fire-resistant and helps with thermal insulation
Wood fiber/sawdust: Works as an adhesive to improve overall performance
Fiberglass mesh: Makes the board structure stronger and tougher
Non-woven fabric: Keeps moisture out while letting the board breathe
MgO boards come in light gray, white, or beige colors, unlike paper-faced materials. You can find them in different grades - smooth face, rough texture, and utility. These boards weigh between 0.85–1.2 grams per cubic centimeter, making them strong yet relatively light.
Core materials used in drywall panels
Traditional drywall has a much simpler makeup. Gypsum, also known as calcium sulfate dihydrate, serves as the core material. Manufacturers heat and grind this natural mineral into fine powder, then mix it with water to create a thick slurry.
Drywall's sandwich-like structure consists of:
1. A gypsum core at the center
2. Thick, smooth paper facing on the front that's ready to paint
3. Rough paper backing on the reverse side that bonds well with joint compound
Gypsum's fire resistance makes it valuable for construction. Heat causes gypsum to release water vapor that slows down flame spread. Manufacturers also add various ingredients to the gypsum slurry to improve fire resistance, prevent mold, and enhance soundproofing.
Drywall weighs between 1.2-1.3 g/cm³, which is almost the same and sometimes more weight than MgO board, though many people see it as lighter. This weight helps with structural support and sound reduction.
Key differences in manufacturing process
These materials' performance differences come from their distinct manufacturing processes. MgO boards go through several steps that make them more durable:
Manufacturers start by mixing magnesium oxide powder with magnesium sulfate solution to create a cement slurry. They blend in perlite, wood fibers, and reinforcing materials, then add layers of fiberglass mesh for extra strength. The mixture gets cast into thin cement panels that need specific curing procedures to work properly.
MgO boards work great in Structural Insulated Panels (SIPS) and Exterior Insulated Finish Systems (EIFS) because of their excellent structural properties.
Drywall manufacturing uses a simpler process. A mixture of gypsum powder, water, and additives creates a slurry that goes between paper layers. Standard-sized sheets are cut from continuous sheets before drying.
MgO boards offer some environmental benefits compared to traditional drywall. They're made from inorganic materials that don't release toxins during manufacturing or disposal. The production process creates fewer harmful emissions and uses less energy than gypsum-based sheetrock manufacturing.
The cloth-like structure and fiberglass in MgO boards create impressive bending strength of 18-27 MegaPascals (MPa), which beats gypsum boards' maximum of 5.6 MPa. Impact resistance shows big differences too - MgO boards can take about 4.5 kilojoules of impact compared to gypsum's 1 kilojoule.
MgO boards cost more than paper-faced gypsum drywall. Many construction projects find this investment worthwhile when they need durability and resistance to environmental factors.
Fire Resistance Ratings and Safety Standards
Fire safety plays a vital role in choosing construction materials. Building codes now just need higher standards for fire resistance. MgO board and traditional drywall show clear differences in how they handle fire events.
MgO board fire rating: Up to 4 hours
Magnesium oxide boards are champions of fire resistance and protect buildings well during a blaze. These boards achieve fire ratings up to 4 hours, which makes them perfect for places that need strict fire safety. This extended protection gives people more time to evacuate and emergency teams to respond.
MgO boards' heat tolerance makes them great at fighting fires. They stay structurally sound even at temperatures reaching 1,472°F (800°C). This impressive performance comes from magnesium oxide's natural properties - it simply won't burn.
Quality MgO boards meet the ASTM E136 non-combustible standard. European Standard EN 13501-1 rates them as A1 non-combustible materials - the highest fire resistance level available. High-quality magnesium boards in wall assemblies can reach 1-hour and 2-hour fire ratings without extra materials.
Drywall fire resistance limitations
Standard gypsum drywall doesn't match MgO boards in protection. Though sold as fire-resistant, traditional drywall protects for less than an hour. This becomes the biggest problem when people need more time to evacuate.
Drywall's fire resistance comes from its thermal properties. Its core has 21% crystalline water that creates a temporary shield during fires. Rising temperatures turn this water into steam, which cools nearby materials and slows down flames.
Notwithstanding that, this protection has clear limits. Lab tests show that gypsum board turns to powder within 20-30 minutes at 400°C, losing all its bending strength. The paper facing that gives drywall its structure breaks down between 200°C and 350°C.
Type X and Type C drywall offer better fire resistance. Type X's 5/8" panels usually provide 1-hour protection. Type C includes glass fiber reinforcement and other ingredients to boost its fire resistance. Higher ratings (2-4 hours) need multiple board layers or extra components.
Smoke and toxic gas emissions during fire
The materials' smoke and toxic emissions create the most important safety difference. MgO boards produce almost no smoke and zero toxic fumes during fires. This is a big deal as it means that people can evacuate more easily during emergencies.
Gypsum drywall releases harmful gasses when burning. Regular drywall creates moderate smoke and toxic fumes that make air quality and visibility worse during evacuations. This matters because smoke inhalation kills more people than any other factor in fires.
Material composition explains these emission differences. MgO boards don't have organic materials that could catch fire and create fumes. Buildings stay safer without toxic emissions, especially in enclosed spaces where evacuation takes longer, like high-rises or healthcare facilities.
Fire testing shows these differences clearly. Wall assemblies face controlled fires at temperatures above 1000°C. Tests check if walls stay standing and keep the unexposed side's temperature rise under 140°C above the starting point. MgO boards beat traditional materials in all key fire safety measures during these tough tests.
Moisture and Mold Resistance in Humid Environments
Moisture damage and mold growth create major challenges for construction materials in humid environments. Your choice between traditional drywall and MgO boards can make a big difference in structural integrity and indoor air quality as time passes.
Water absorption rate of drywall vs MgO
These materials differ mainly in how they handle moisture. MgO boards show unique resistance with a surface moisture absorption rate of just 0.34%. This low rate helps them stay stable even after water exposure. Standard gypsum drywall absorbs nearly 3% of moisture on contact, which makes it nowhere near as resistant to water damage.
The gap between these materials becomes clear during standardized immersion testing. Quality MgO boards show less than 10% water absorption after two-hour immersion tests. Wood-based panels absorb much more - upwards of 20%.
MgO boards are better at drying too. After reaching free moisture saturation, magnesium boards return to normal in about four days. This matches gypsum but outperforms plywood and OSB, which need nearly 25 days to dry completely.
Material |
Surface Absorption Rate |
Recovery Time After Saturation |
MgO Board |
0.34% |
4 days |
Gypsum Drywall |
3% |
4 days |
Wood-Based Panels |
>20% |
25 days |
Mold growth prevention in magnesium board
MgO boards don't just resist water - they actively stop mold growth through multiple ways. These boards are inorganic, so they don't provide food for mold spores. This eliminates any biological foundation that fungal growth needs.
On top of that, MgO boards have natural antimicrobial properties that fight mold, mildew, fungus, and rot. These physical properties create conditions where mold can't grow, even in humid environments.
Magnesium board's natural moisture management adds more protection. The boards store moisture safely while letting vapor pass both ways. This breathability stops internal condensation that usually causes hidden mold in standard construction materials.
Tests from independent labs confirm that MgO boards work without vapor barriers in any climate zone. Moisture levels inside these panels stay too low for microbial growth, whatever the outside humidity.
Performance in bathrooms and basements
MgO boards really shine in damp spaces like bathrooms and basements. In these tough spots, magnesium boards keep their shape without warping, swelling, or coming apart during short moisture exposure.
MgO boards work great for:
Bathroom walls, especially around showers and tubs
Sauna enclosures with big temperature and humidity swings
Pool areas that are always damp
Basement finishing where moisture is common
Kitchen backsplashes and sink areas
Regular gypsum drywall needs special moisture-resistant versions ("green board") for these uses. But even these upgraded gypsum products can't match standard MgO boards. Long-term moisture exposure makes standard drywall swell, warp, and break down.
Health risks go beyond structural issues. Mold in homes can cause serious health problems and expensive cleanup costs. MgO boards prevent these issues and help create healthier indoor spaces, especially if you have allergies, asthma, or chemical sensitivities.
Durability and Structural Integrity Over Time
Buildings need construction materials that last long and stay strong throughout their life. A look at magnesium oxide mgo board compared to regular drywall shows clear differences in how tough they are.
Impact resistance of MgO boards
MgO boards can take hits and impacts way better than standard drywall. Good quality magnesium boards hit an impact strength of 4.5 kilojoules or higher. These boards are tough because they use fiberglass mesh inside, creating a cloth-like structure that spreads out force really well.
MgO boards also stand out with their bending strength (flexural strength) of 18-27 MegaPascals (MPa). They can handle heavy loads without bending or breaking, making them perfect where structural strength matters most. Several factors make these boards so tough:
Reinforced core structure with fiberglass mesh
Higher density mineral composition
No paper facing that could tear or puncture
Natural crystalline structure of magnesium oxide
Real-world use shows walls that look good and stay strong, even in tough conditions. The high impact strength stops dents, holes, and surface damage that usually ruins normal wall materials.
Cracking and denting in drywall
Regular drywall just doesn't hold up as well. With impact strength at only 1 kilojoule and bending strength under 5.6 MPa, gypsum boards break down from everyday use. This weakness shows up in many common problems:
Drywall gets dented easily when things hit it because it's made with paper fibers. Small impacts leave visible marks that need fixing. Cracks also pop up where drywall sheets meet, usually because the compound shrinks as it dries.
Corner areas give the most trouble. Metal corner beads help some but stay bent once they're hit. You can't just patch these corners - they need complete replacement.
"Nail pops" create another headache when nail heads push through the drywall surface. New homes see this problem a lot when wet wood studs dry out and warp after installation.
Drywall in busy areas needs constant fixes:
1. Widening cracks with a utility knife
2. Applying new compound in multiple thin layers
3. Sanding smooth and repainting
4. Reinforcing damaged areas with additional materials
Patches don't last forever - cracks come back in the same spots, which means more work and money spent on repairs.
Long-term performance in high-traffic areas
Places with lots of people really show the difference between these materials. MgO boards work great in schools, hospitals, and businesses where walls take constant abuse.
These boards stay strong without needing the regular fixes that drywall demands. Hallways, stairwells, and other busy areas benefit from their resistance to scratches and dents. You can hang heavy things on them without extra support behind the wall.
Regular drywall works fine in homes but struggles in demanding commercial spaces. It's too soft and gets damaged easily from impacts and heavy loads. Repairs get pricey, and sometimes you need to replace whole sections. Over time, maintaining drywall costs much more than the minimal care MgO boards need.
Life expectancy tells the biggest story: MgO boards last much longer than standard drywall. This longer life makes up for their higher price tag, giving better value in projects where toughness matters most.
More and more high-traffic buildings now use MgO boards inside and out, despite the higher upfront cost. The benefits over time outweigh the initial expense through less maintenance, fewer replacements, and better looks that last.
Thermal and Acoustic Insulation Capabilities
Good insulation plays a key role in modern construction. It affects energy use and makes spaces more comfortable. Wall materials' insulation quality determines heating and cooling costs and blocks unwanted noise.
Thermal conductivity of MgO vs drywall
MgO board shows clear advantages over regular drywall when it comes to thermal performance. These boards have a thermal conductivity value of 0.45 W/m/°C at room temperature. This low conductivity makes them great at stopping heat transfer between inside and outside.
The thermal conductivity of MgO boards changes with temperature in interesting ways. The conductivity drops to about 0.12 W/m/°C when temperatures reach around 200°C. This happens because the material dehydrates, which boosts its insulating properties as temperatures change.
Magnesium boards' thermal stability brings several real-world benefits:
Less energy escapes through walls and ceilings
Room temperatures stay more stable
Heating and cooling costs drop in harsh climates
The structure stays intact without thermal expansion issues
Regular gypsum drywall doesn't match up. Its thermal conductivity stays the same no matter the temperature. It lacks the adaptive properties that make magnesium board better at handling temperature changes.
MgO boards work great in places with big temperature swings. Their low thermal conductivity helps prevent condensation - a common issue with less effective insulating materials.
Soundproofing performance in interior walls
The dense structure of MgO boards makes them better at blocking sound too. These boards beat standard drywall panels at sound insulation. This quality makes them a top pick for projects that need good noise control.
MgO boards block sound better for two main reasons:
1. Higher density - More mass means better sound blocking
2. Material composition - The structure absorbs sound waves instead of letting them pass
Magnesium oxide mgo board works well in:
Application |
Acoustic Benefit |
Home theaters |
Keeps sound from leaking to other rooms |
Recording studios |
Blocks outside noise |
Multi-family housing |
Stops noise between units |
Office environments |
Creates quieter work areas |
Educational facilities |
Makes learning easier by reducing noise |
Regular drywall can do an "okay" job with sound, especially with multiple layers. But even then, it can't match what a single layer of MgO can do. Drywall's lighter weight lets more sound through, which means less effective sound barriers.
Projects that need serious sound blocking often need extra soundproofing with standard drywall. MgO boards might cost more upfront, but you won't need those extra materials.
These benefits make buildings perform better and feel more comfortable. Homes get quieter living spaces. Businesses save on operating costs and create better work environments.
The thermal and acoustic advantages should factor into your cost calculations. These benefits last throughout the building's life - they're not just about saving money during construction.
Installation Process and Labor Requirements
The total project cost depends on more than just the raw mgo board price. Installation challenges play a big role. Both materials need proper installation techniques to perform well, but they require different approaches and tools.
Cutting and fastening MgO boards
MgO board installation works best with specific tools. The cleanest cuts come from circular saws with thin carbide blades through these dense materials. Thicker magnesium boards need a plunge saw with a diamond blade for better precision. Thin boards (8mm or less) can be scored and snapped, unlike thicker variants.
The board's mildly alkaline composition (pH 9-10) means you'll need stainless steel screws to prevent corrosion. Regular galvanized fasteners might corrode unless they have barrier coatings. You should pre-drill holes at least 12mm from board edges to keep the structure intact and prevent cracks.
Drywall installation tools and techniques
Drywall needs a completely different set of tools. You'll need T-squares for marking cuts, utility knives for scoring, and special drywall screws. While MgO boards need carbide tools, drywall cuts easily with simple hand tools.
The drywall process has clear stages:
1. Measuring and cutting panels to size
2. Securing to studs with drywall screws
3. Applying joint tape and multiple layers of compound
4. Sanding between coats for a smooth finish
This multi-step finishing process sets drywall apart from MgO board installation, which rarely needs taping or compound.
Time and labor cost comparison
Labor makes up much of the total installation costs for both materials. MgO board installation by skilled workers costs between $3.00 and $8.00 per square foot. These rates reflect the expertise needed to handle heavier panels correctly.
MgO boards have some efficiency advantages. You can use them right after installation, while drywall needs up to seven days for joint compound to set. On top of that, MgO board's tight-fitting joints often eliminate the need for tape, corner bead, and joint compound.
MgO board installation might reduce your project time by skipping long drying periods, even though it needs special tools and handling. Time-sensitive projects might benefit from this advantage, which could offset the higher MgO board price through faster completion and fewer labor hours.
Real Cost Analysis for 2025 Projects
The price gap between MgO board and drywall in 2025 construction projects needs a closer look beyond just upfront costs. Builders must look at the full cost to make smart decisions about materials.
mgo board price per square foot (2025 estimates)
MgO board prices in 2025 range from $1.50 to $3.50 per square foot based on thickness, quality, and specific performance features. High-end magnesium oxide mgo board with better fire and moisture resistance costs more. Basic utility-grade magnesium boards are available at lower prices.
Construction-grade magnesium board for interior work costs $2.00 to $2.50 per square foot on average, which is a big investment compared to regular materials. Large projects might get volume discounts of 10-15% on bulk purchases.
Drywall cost breakdown: material + labor
Regular drywall materials cost much less, between $0.30 and $0.70 per square foot for simple 1/2-inch panels. Even special moisture-resistant or fire-rated drywall options are cheaper than basic magnesium board.
The total installation cost goes beyond just materials. Professional drywall installation in 2025 costs $2.21 to $2.62 per square foot including materials and labor. Here's the breakdown:
Component |
Cost Range (per sq ft) |
Materials |
$0.30 - $0.70 |
Labor |
$1.50 - $3.00 |
Finishing |
$0.50 - $1.50 |
Professional magnesium board installation now costs between $3.00 and $8.00 per square foot with materials, due to higher material costs and special labor needs.
Lifecycle cost comparison: maintenance and replacement
The original price difference becomes smaller over time when you look at total ownership costs. Building costs are just 10-20% of lifetime expenses, while maintenance and operations take up the other 80-90%.
MgO boards need very little maintenance over their long life, which saves money on:
Moisture and impact damage repairs
Mold removal and related health costs
Replacement in busy or damp areas
This makes magnesium board an affordable choice for commercial spaces, bathrooms, basements, and other damp places where drywall often needs early replacement.
Environmental Impact and Sustainability Factors
Environmental responsibility in construction now shapes how we choose materials beyond just their performance. Building professionals assess materials by examining their complete environmental impact from production to disposal.
Recyclability of magnesium oxide boards
MgO boards excel in end-of-life sustainability. These boards are fully recyclable through a systematic process that includes collection, cleaning, crushing, and transformation into new products. The recyclability brings clear environmental benefits as it keeps construction waste out of landfills and preserves natural resources by reducing raw material extraction.
Recycled MgO boards need less energy to produce than new ones, which leads to reduced carbon emissions throughout their lifecycle. Experts call these magnesium boards "landfill friendly" because they lack toxic substances that could harm soil or water sources.
VOC emissions and indoor air quality
The growing focus on indoor air quality has sparked interest in materials that emit minimal chemicals. MgO boards contain zero volatile organic compounds (VOCs) according to ASTM D5116-10 testing standards. This quality sets them apart from many conventional building materials that release harmful chemicals.
Magnesium oxide mgo boards are free from:
Formaldehyde (meets ASTM D6007-14 standards)
Asbestos materials
Toxic binders and crystalline silica
Heavy metal salts and hexavalent chromium
These features make magnesium board an ideal choice for people who suffer from allergies, asthma, or chemical sensitivities.
Energy usage in production process
MgO boards' manufacturing energy footprint offers another key advantage. The production needs just 25-50% of the energy required for calcium hydroxide or Portland cement manufacturing. This efficiency comes from:
Lower temperature processing (versus traditional cement requiring 1400°C)
Simpler manufacturing process that needs fewer energy-intensive steps
Room-temperature processes some manufacturers have developed
MgO boards can absorb CO2 during curing and throughout their lifecycle, which potentially reduces net carbon emissions by 73% compared to Portland cement.
Conclusion
The choice between MgO boards and traditional drywall for your 2025 projects goes beyond the original price tag. MgO board costs substantially more upfront—$1.50 to $3.50 per square foot while drywall costs $0.30 to $0.70. You'll need to review this price difference against the long-term advantages.
Fire safety emerges as the most compelling benefit. MgO boards give you up to four hours of protection, and drywall maxes out at just one hour. These magnesium boards are completely waterproof, which solves the moisture problems that often plague drywall in bathrooms, basements, and humid spaces.
The premium price of mgo board makes sense when you look at its durability. Its impact resistance reaches 4.5 kilojoules compared to drywall's 1 kilojoule. This means your walls stay looking good and structurally sound for decades with minimal upkeep. High-traffic areas benefit most, where regular drywall would need constant fixes.
Magnesium boards shine on the environmental front too. They produce zero VOC emissions, are fully recyclable, and take less energy to manufacture. These features line up perfectly with modern construction's push toward sustainability. Projects focused on health benefit from these boards' lack of harmful chemicals.
Building professionals should weigh all these factors carefully. Traditional drywall works well for budget-focused projects with simple needs. Yet magnesium oxide mgo board performs better in almost every way except the original cost. Your choice depends on what matters most—saving money now or getting better performance, sustainability, and lower maintenance costs later. This analysis should help you make smart choices for your 2025 construction projects.