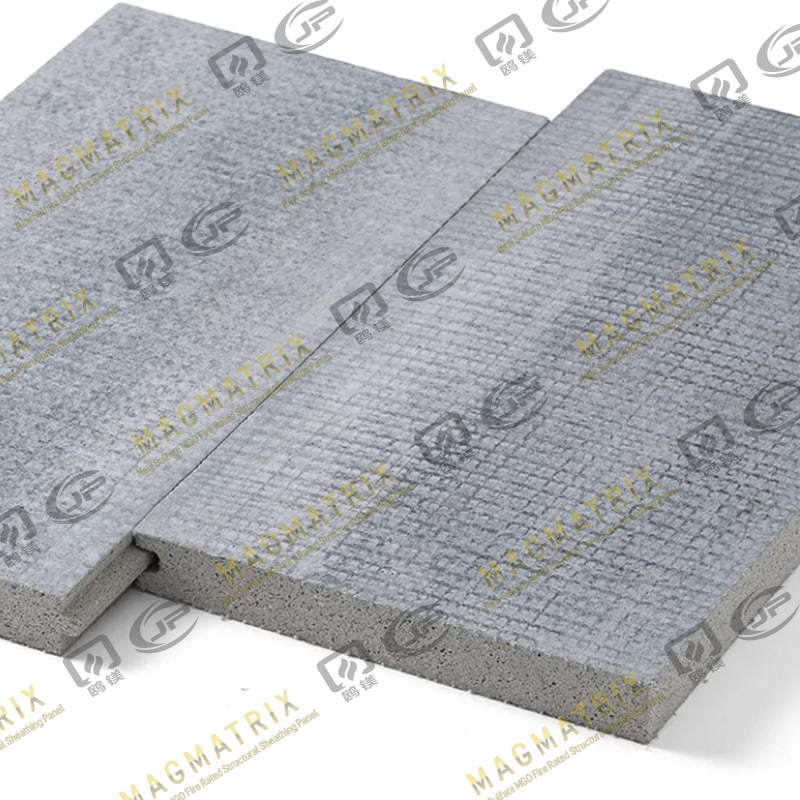
Here's something amazing - mgo boards can handle heat up to 1200°F without melting. This incredible fire resistance explains why top architects now choose these innovative building materials for their net-zero construction projects.
Magnesium boards pack some impressive benefits that put them ahead of traditional options. The differences between mgo board and gypsum board are clear - magnesium boards are 100% recyclable, biodegradable and create less CO₂ during production. Mgo board flooring also keeps indoor temperatures stable and cuts down energy use. These boards are a great fit for passive house designs, especially when you have subfloor applications where each material needs to boost efficiency and support green practices.
This piece will get into why architects focused on sustainability love these versatile boards. We'll look at everything from their non-toxic makeup that helps indoor air quality to their long-lasting performance, and see how mgo boards change green building practices to create truly sustainable structures.
Why MgO Boards Align with Net-Zero Design Goals
Net-zero buildings just need materials that minimize their environmental effect throughout their lifecycle. MgO boards are a perfect match for these tough standards. They offer two key environmental advantages: minimal carbon footprint during production and remarkable CO₂ absorption as they cure.
Low embodied carbon in production process
The manufacturing process of mgo board uses substantially less energy than traditional cementitious materials. Production happens at lower temperatures – between 700-900°C compared to 1450°C for ordinary Portland cement. This temperature difference saves energy and leads to fewer greenhouse gas emissions.
Energy savings go beyond temperature requirements. Research shows that magnesium board manufacturing uses about 50% less energy than other cement-based boards. This reduction is vital for construction projects seeking net-zero certification.
The numbers tell a clear story about carbon emissions. MgO construction material creates about 340 kg of CO₂ per metric ton. In comparison, calcium oxide used in traditional concrete produces around 740 kg per metric ton. This means MgO boards produce 54% less carbon than conventional materials.
Several factors contribute to this reduced carbon effect:
- Lower calcination temperatures (700-900°C vs. 1450°C)
- Simpler manufacturing techniques
- Knowing how to use alternative, low-calorific-value fuels
- Reduced water requirements
Magnesium oxide comes from abundant and renewable sources like seawater and brine pools. This improves sustainability by reducing dependence on extensive mining operations that traditional building materials need.
Traditional cement and concrete production accounts for about 5% of global CO₂ emissions. MgO board subfloor and wall applications offer a viable alternative that fits perfectly with net-zero design principles.
Magnesium oxide comes from abundant and renewable sources like seawater and brine pools. This improves sustainability by reducing dependence on extensive mining operations that traditional building materials need.
Traditional cement and concrete production accounts for about 5% of global CO₂ emissions. MgO board subfloor and wall applications offer a viable alternative that fits perfectly with net-zero design principles.
The technical process has several stages:
1.MgO hydrates to form Mg(OH)₂ (magnesium hydroxide)
2.The Mg(OH)₂ absorbs CO₂ from the atmosphere
3.This forms hydrated magnesium carbonates (HMCs)
4.These carbonates provide binding properties and strength
Unlike traditional materials that release carbon throughout their lifecycle, mgo boards can reabsorb almost as much CO₂ as they create during manufacturing.
The research backs these benefits with real results. Carbonation curing techniques can boost this carbon capture effect. Samples cured under accelerated carbonation (10% CO₂) showed 28-day compressive strengths seven times higher than those cured normally. This proves that carbon absorption not only helps the environment but also makes the material stronger.
Architects who choose mgo board over gypsum board make a choice that supports carbon reduction goals while getting better performance. Buildings in France alone create about 23.5% of greenhouse gas emissions from traditional building materials. Switching to alternatives like magnesium board offers a great chance to reduce construction's climate effect.
The construction industry faces growing pressure to reduce its environmental footprint. MgO boards offer a compelling solution that matches net-zero building goals perfectly. They combine lower carbon production with active carbon capture during use.
Non-Toxic Composition and Indoor Air Quality Benefits
People spend 90% of their time in net-zero buildings, and the materials used in construction directly affect their health. Material choices become vital in these tightly-sealed spaces. MgO boards emerge as a healthier option compared to standard building materials due to their exceptional non-toxic qualities.
Absence of VOCs, formaldehyde, and asbestos
MgO boards' superior health benefits come from their natural mineral makeup. These boards don't contain volatile organic compounds (VOCs), formaldehyde, asbestos, silica, benzene, or ammonia. This isn't just marketing - it represents a radical alteration in construction material safety.
Standard building materials release harmful chemicals through off-gassing that can last years after installation. Many regular products use formaldehyde-based adhesives that release toxins into living spaces. MgO boards, however, produce almost no toxic off-gassing. This creates a safer indoor environment right from the start.
MgO board's composition is simple and natural:
- Magnesium oxide/sulfate (primary binding agent)
- Wood dust (cellulose) to add flexibility
- Perlite or vermiculite to provide insulation
- Glass fiber mesh to reinforce structure
This simple formula shows clear differences when you compare MgO boards with gypsum options. Regular gypsum products often contain artificial additives and irritants that can harm sensitive people over time.
Architects focused on health should note that MgO boards are labeled as "nutritional waste" at the end of their life. This proves how safe they are - they can return to earth without special handling.
Improved air quality in airtight net-zero buildings
Net-zero buildings create a unique challenge for indoor air quality. Their sealed design saves energy but might trap pollutants. MgO board flooring and wall systems offer major advantages here.
These non-toxic boards work exceptionally well in controlled-ventilation spaces. By removing a key source of indoor pollutants, architects can design spaces that boost occupant health while staying energy efficient.
Some groups see immediate benefits. People with asthma, allergies, or chemical sensitivities often feel better in spaces built with MgO boards. Kids, older adults, and hospital patients also benefit from fewer chemicals in the air.
Moisture control becomes critical in airtight buildings. Poor moisture management leads to mold and bad air quality. MgO board subflooring excels here - it naturally resists mold and mildew, which keeps biological contaminants away. This resistance maintains good air quality even during humid weather or seasonal changes when condensation might cause issues.
Public health benefits go beyond personal comfort. Schools, hospitals, and apartment buildings share air among many people. Using non-toxic materials can reduce sick building syndrome and health complaints. This makes MgO board flooring valuable for buildings with vulnerable groups.
The health benefits continue even during fires. Unlike standard materials that create thick smoke and toxic fumes when burning, MgO boards keep the air clearer. This helps people see and breathe better during evacuations - adding to the material's fire-resistant properties.
Zero off-gassing certification combined with natural antimicrobial properties creates an exceptional indoor environment. This matches perfectly with net-zero design principles and modern wellness standards.
Energy Efficiency Through Thermal and Moisture Control
MgO boards' thermal performance is a vital part of meeting net-zero energy standards. These boards stand out because they regulate temperature and handle moisture better than other materials. Both qualities substantially affect a building's energy use and how well it performs over time.
Thermal insulation properties of MgO board flooring
MgO boards show remarkable thermal insulation qualities that make them valuable in energy-efficient construction. These boards have low thermal conductivity and reduce heat transfer between indoor and outdoor environments effectively. Buildings maintain steady indoor temperatures through seasonal changes, which reduces the load on heating and cooling systems.
MgO boards' thermal resistance (R-value) adds substantially to their insulation performance. Tests by Intertek show high-end magnesium oxide boards have an R-value of 0.065(m²·K)/w. This rating might seem modest alone but becomes highly effective in complete building systems.
Ground applications prove MgO board flooring delivers outstanding energy efficiency benefits:
- Buildings with MgO structural insulated panels use about 30% less energy than conventional methods
- These panels keep indoor temperatures stable whatever the weather outside
- Reduced heating and cooling costs lead to long-term savings
MgO boards' unique physical structure helps them achieve optimal thermal performance. The material's density and composition resist heat flow while staying structurally sound. Spaces built with MgO board subfloor systems need less energy to stay comfortable and experience fewer temperature swings.
MgO boards merge well with other high-performance materials beyond their basic insulation properties. To name just one example, MgO structural insulated panels combine these boards with rigid foam insulation to create a complete thermal barrier. MgO boards bonded with pressure-fused polyurethane insulation achieve an R-value of 6.5 per inch—better than polystyrene and standard spray-applied polyurethanes.
Architects praise magnesium boards' thermal stability. Unlike other materials that expand and contract as temperatures change, MgO boards stay dimensionally stable. This stability preserves the building envelope's integrity and stops energy-wasting thermal bridges.
Moisture resistance in high-humidity zones
Moisture control's link to energy efficiency often gets overlooked but remains essential. MgO boards excel here too. Their exceptional water resistance keeps both structural integrity and thermal performance strong even in tough environments.
Water absorption tests show MgO panels absorb less than 10% moisture after two hours of immersion—like gypsum but much better than wood-based panels that absorb over 20%. MgO boards also dry faster, reaching balance in about four days while plywood and OSB take nearly 25 days.
MgO boards outperform gypsum boards in handling moisture because they keep their mechanical properties when wet. Gypsum panels lose 36% to 52% of their flexural strength after 25 wetting-drying cycles. MgO boards stay almost completely strong. OSB and plywood weaken by 40% and 9% respectively under the same conditions.
This stability with moisture directly improves energy efficiency. Wet insulation works poorly and can lose up to 40% of its thermal resistance. MgO boards prevent this by:
5.Staying dimensionally stable when wet (no warping or swelling)
6.Fighting off mold and mildew that can damage building envelopes
7.Drying effectively through their unique hygric properties
MgO boards' hygrothermal performance makes them perfect for humid environments where traditional materials fail. They store moisture while allowing vapor to pass both ways, creating a balanced moisture system. This eliminates the need for interior vapor retarders in any climate zone and simplifies wall design.
Before high-quality magnesium boards existed, architects had to choose between moisture resistance and thermal performance. MgO board flooring solves this problem by providing both qualities at once. Buildings become more resilient and energy-efficient, performing consistently in all kinds of weather.
Durability and Lifecycle Performance in Sustainable Architecture
MgO boards' durability directly affects environmental impact and running costs throughout a building's life. These boards show remarkable qualities that make them valuable for architects who design green structures built to last generations.
Fire resistance up to 1200°C
MgO boards' fire resistance stands out as their most impressive durability feature. The boards withstand temperatures up to 1200°C (2192°F) and keep their structural integrity. Traditional building materials don't match this performance and fail at lower temperatures.
Yes, it is worth noting that MgO boards have an A1 non-combustible rating, which offers unmatched safety in homes and commercial buildings. This rating means they never help spread fire. The magnesium boards stay structurally stable even at extreme temperatures, which substantially reduces collapse risks during fires.
MgO boards provide another safety advantage - they release almost no harmful substances during fires. Unlike common materials, they don't give off toxic gasses in high heat. This creates safer evacuation conditions. This quality becomes especially important when you have wildfire-prone areas where material choice can dramatically change safety outcomes.
Rigorous testing standards back up MgO boards' fire performance. ASTM E84 tests show these boards have no flame spread at 1200°C. Their non-combustible properties meet ASTM E136 standards, making them perfect for fire-rated assemblies under ASTM E119.
Mold and pest resistance in long-term use
Beyond fire resistance, MgO boards excel at curbing biological threats that usually break down standard building materials. Magnesium oxide resists microbial and insect damage, which extends how long installations last.
MgO boards' inorganic makeup creates an environment where mold, mildew, and fungus can't grow. These boards contain no organic material, so termites, carpenter ants, and wood-boring insects find nothing to eat. This resistance to biological threats works great in humid climates where standard materials often break down faster.
MgO boards handle moisture better than gypsum boards. Both materials resist mold at first, but gypsum boards with paper facing become vulnerable after long moisture exposure. MgO boards keep resisting mold even after extensive water contact because of their fully inorganic makeup and alkaline properties.
This translates into excellent structural stability for long-term use. MgO board flooring systems don't warp, swell, or come apart during brief moisture exposure[162]. The largest longitudinal study shows these boards keep their mechanical properties even after long exposure to harsh environments.
Reduced maintenance and replacement cycles
MgO boards' long service life boosts their green profile by cutting down replacement needs and environmental effects. Their mix of fire resistance, moisture handling, and biological resistance means much less maintenance.
To cite an instance, see these proven performance advantages:
- MgO boards keep their flexural strength after 25 cycles of water soaking and drying, while OSB loses 40% strength and plywood loses 9%
- Gypsum panels lose 36-52% strength under similar test conditions
- MgO boards resist impact better, which reduces damage in high-traffic areas
These qualities create real lifecycle benefits for sustainable architecture. Buildings with MgO board subfloor systems need fewer repairs over time. The upfront cost might be higher, all the same, long-term savings from less maintenance make up for this investment.
These durability advantages add up over a building's life. Structures using MgO boards in SIP (Structural Insulated Panel) applications resist flame, water, mold, and insects. This means minimal upkeep keeps them sound for decades.
Less need for replacement and repair creates multiple green benefits. Fewer material cycles reduce embodied carbon and waste throughout a building's life. MgO board flooring's extended durability isn't just convenient - it's essential for sustainable design.
Recyclability and End-of-Life Waste Reduction
MgO boards are revolutionizing how architects think about sustainability in construction materials. These boards stand out with their end-of-life options that cut down construction waste and support closed-loop material cycles.
100% recyclability of magnesium board
MgO boards have become a game-changer in construction. Architects who care about the environment love them because they're fully recyclable. Most building materials end up in landfills, but magnesium boards can be processed and used again to create a sustainable cycle.
The recycling process of MgO boards follows these steps:
8.Collection and segregation - Workers gather MgO boards from construction or demolition sites and separate them from other debris
9.Cleaning - Teams remove paint, cladding, and other impurities
10.Crushing and grinding - Clean boards are ground into smaller pieces
11.Separation - Methods like magnetic separation or sieving remove contaminants
12.Reworking - Refined MgO particles become part of new products, often mixed with fresh materials
Recycling MgO boards does more than reduce waste. The process saves natural resources by cutting down the need for new raw materials. China leads global production of MgO-based artificial plate, making about 600 million square meters yearly. This massive scale makes recycling even more vital for managing resources responsibly.
Recycled MgO boards need less energy to produce than new ones, which reduces construction's carbon footprint. The recycling process can extract magnesium for other industrial uses, turning potential waste into valuable resources.
MgO boards beat gypsum boards in recyclability. While people can recycle gypsum under certain conditions, MgO boards offer easier recycling with fewer restrictions.
Biodegradability under specific conditions
MgO boards shine in another environmental aspect - they can biodegrade under specific conditions. This sets them apart from synthetic building materials that stay in landfills for centuries.
These boards act as "nutritional waste" that safely biodegrades. People can dispose of them in several ways:
- Mix them into soil as nutrients
- Bury them safely in landfills without harming the environment
- Use them as ground cover or road base material
MgO's inert nature means minimal environmental impact when disposal becomes necessary. This helps in places where recycling facilities aren't available.
The biodegradability of MgO board flooring gives peace of mind about future disposal. Even when people can't recycle or reuse MgO board subfloor materials, they won't harm the environment.
MgO boards' biodegradability reduces landfill waste and eases pressure on waste management systems. Their durability means less construction waste during installation and use, making them eco-friendly throughout their life.
Architects aiming for sustainable buildings find MgO boards' complete recyclability and biodegradability compelling. These end-of-life benefits, plus their strong performance, make them perfect for net-zero building designs.
Versatile Applications in Net-Zero Construction
Architects have found innovative ways to use mgo boards in net-zero construction projects. These versatile materials work well with building systems of all types and support strict sustainability standards.
MgO board subfloor in passive house designs
Passive house construction needs materials that deliver exceptional energy performance and create healthy indoor environments. MgO board subfloor installations shine here by providing a stable foundation that blends smoothly with other passive house elements. These boards let air and moisture vapor pass through—like traditional lime-based materials—which makes them valuable for breathable building assemblies that prevent condensation and trapped moisture.
MgO floor boards provide high compressive strength and stay dimensionally stable. This creates a solid foundation for flooring types like hardwood, laminate, and tile. What makes these boards even more valuable for passive house designers is their ability to maintain properties in moisture-prone areas such as kitchens, bathrooms, and laundry rooms.
Use in SIP panels and modular construction
Structural Insulated Panels (SIPs) showcase one of the best uses for magnesium boards in net-zero buildings. These panels combine an insulating foam core between two layers of mgo board to create high-performance building components for walls, ceilings, and floors. The key benefits include:
- Construction time drops significantly compared to traditional methods
- No thermal bridges where energy typically escapes
- Smooth integration with prefabricated and modular construction systems
Prefabrication with mgo boards has proven its worth in hundreds of projects. One assembly system using these panels has been active since 2007 and features in about 500 buildings worldwide. These magnesium board-based SIPs offer a clear path to faster, more efficient construction while delivering strong energy performance.
Exterior cladding for thermal envelope integrity
The building envelope plays a crucial role in achieving net-zero energy performance. MgO boards serve as excellent exterior cladding options that protect thermal envelope integrity under tough conditions. Their weather resistance makes them ideal for external use, even in harsh environments.
Premium MgO cladding's exceptional structural strength lets builders directly install heavy materials like fiber cement board or brick without extra support. Construction teams can install these panels using standard plywood techniques without special training.
MgO boards combine smoothly with exterior insulation and finish systems (EIFS) to create continuous insulated building envelopes. This setup boosts overall energy efficiency and offers many esthetic choices including synthetic stucco finishes, lap siding, brick veneer, and stone.
Comparing MgO Board vs Gypsum Board in Green Projects
The differences in performance between magnesium oxide and gypsum boards become more noticeable as we look at green building materials. Your choice between these options will affect both how well the building performs right away and its environmental footprint down the road.
Fire rating and moisture resistance comparison
These materials show major differences in how they handle fire. MgO boards reach an A1 fire resistance classification (non-combustible) and can handle temperatures up to 1200°F without failing structurally. Standard gypsum boards resist fire through water vaporization but flames will destroy them eventually. MgO boards need just 3mm thickness to meet safety standards, while gypsum needs 12mm to match these ratings.
MgO boards excel at handling moisture and stay structurally sound even after staying underwater for 100 days. The numbers tell a clear story - MgO boards absorb only 0.34% moisture compared to gypsum's 3%. Gypsum boards lose 36-52% of their strength after 25 cycles of getting wet and drying out. MgO boards keep almost all their structural strength intact.
Lifecycle emissions and recyclability differences
Carbon footprint numbers show MgO board production creates about 70kg of CO₂ per ton. This is nowhere near cement's 740kg and matches gypsum's 65kg. MgO boards stand out because they keep absorbing carbon dioxide throughout their life, turning it into magnesium carbonate and making air quality better.
MgO boards shine at the end of their life cycle since you can recycle them completely. Builders can reuse broken pieces, grind them into new materials, or add them to agricultural products. You can also crush these boards to let them degrade naturally, which might help stabilize soil. Gypsum boards can be recycled too, but they often release harmful substances during disposal.
MgO boards perform better in all these key areas. That's why sustainable architects choose them more often when they need materials that work well now and stay environmentally friendly over time.
Cost Efficiency Over Time for Architects and Builders
The original cost often drives building material choices, but the largest longitudinal study reveals a different story. MgO boards cost USD 1.50-3.50 per square foot while drywall ranges from USD 0.30-0.70. However, their extended lifespan and performance create big financial benefits for architects and property owners.
Lower insurance premiums in fire-prone zones
Property owners can save money right away through reduced insurance premiums when they build with MgO boards. Insurance companies reward their superior fire resistance with better rates. This becomes especially valuable in wildfire-prone regions or dense urban areas where fire safety costs affect insurance rates by a lot.
Multifamily developers now choose MgO panels to build affordable fire-rated wall assemblies with NFPA 285 approved designs. These assemblies prove to be nowhere near standard fire protection requirements. The resulting insurance discounts help offset the higher upfront material costs.
Reduced labor and replacement costs
MgO boards save money throughout a building's lifecycle beyond insurance benefits. Their exceptional durability cuts down repair and replacement expenses that pile up with traditional materials. Buildings with magnesium board installations need much less maintenance over time, especially when you have moisture-prone areas where regular materials break down quickly.
These boards also speed up installation. MgO SIPs (Structural Insulated Panels) help builders finish room additions in two days instead of two weeks. Some MgO panel systems go up 55% faster and save 41% in labor costs compared to conventional stick framing.
The savings continue after construction. Rigid MgO panels eliminate wet-laid gypsum systems in subfloor applications. This removes unwanted moisture and expensive curing time. The panels support shelving and fixtures directly on walls without extra backing materials, which saves on materials and labor.
The total lifecycle costs show MgO boards as the clear winner:
- More affordable than specialty fire-rated products like LP Flameblock
- All but one of these panels last longer due to superior durability
- Less maintenance needed in tough environments
- Lower disposal costs since you can recycle the materials
These accumulated savings prove the value of investing in MgO technology. Architects and builders looking to save money will find it an economically sound choice for environmentally responsible construction.
Conclusion
MgO boards mark a fundamental change in eco-friendly construction materials for net-zero buildings. This piece shows how these boards benefit the environment. They leave minimal carbon footprints during production and absorb CO₂ while curing. This makes them much more sustainable than conventional options. Their non-toxic makeup creates healthier indoor spaces. This becomes especially important when you have tightly-sealed net-zero structures where air quality affects people's wellbeing.
Magnesium boards' performance features make them the top choice for sustainability-minded architects. Without doubt, these boards' exceptional heat regulation and moisture control work together to improve energy efficiency. They keep their structural strength intact. The boards resist fire, mold, and pests exceptionally well. This leads to a longer service life that needs minimal upkeep—a key factor for truly sustainable buildings.
The original costs might seem to favor traditional materials. The financial benefits become clear over time. Lower insurance premiums, quicker installation, and reduced maintenance costs throughout a building's life cycle make the difference. MgO boards deliver better value despite higher upfront investment.
These boards work well in construction of all types—from subfloors to exterior cladding. They adapt easily to different architectural needs. The boards match passive house standards and work well with modular construction methods. This makes them perfect for innovative sustainable building approaches.
MgO boards offer more than just another building material option. They provide a detailed solution for architects who want to create buildings with minimal environmental impact. These structures deliver peak performance, health benefits, and lasting value. Leading architects now choose these boards more often. This shows a basic change toward building materials that line up with both current performance needs and our shared duty to build sustainably for future generations.