In the realm of construction materials, the choice of sheathing can significantly impact a building's performance, longevity, and environmental footprint. This article provides a comprehensive comparison of Magnesium Oxide sheathing board with two traditional alternatives: drywall (gypsum board) and plywood. We will delve into key aspects such as moisture and fire resistance, durability, environmental impact, cost, and ease of installation. By examining the unique properties and applications of each material, readers will gain a clearer understanding of when and why to choose MgO board over conventional options, particularly for projects demanding superior performance in challenging conditions, or those with an emphasis on sustainable building practices.
Key Takeaways
Choosing the right sheathing material is crucial for a building's performance and longevity. Here are the key takeaways from our comparison of Magnesium Oxide (MgO) sheathing board, drywall, and plywood:
Superior Moisture and Mold Resistance: MgO board significantly outperforms both drywall and plywood in wet and humid conditions, making it an ideal choice for bathrooms, kitchens, basements, and exterior applications where moisture is a concern. It is inherently resistant to mold and mildew growth.
Exceptional Fire Resistance: MgO board is non-combustible and offers superior fire resistance compared to drywall and plywood. It provides an excellent fire barrier, enhancing the safety of structures.
High Durability and Strength: With its high compressive and flexural strength, MgO board is more durable and resistant to impact than drywall. While plywood offers good structural strength, MgO board provides a more stable and less susceptible to warping alternative in certain conditions.
Eco-Friendly Option: MgO board boasts a lower environmental impact due to its sustainable manufacturing process, use of mineral-based components, and recyclability. It is often free of harmful chemicals found in some traditional building materials.
Versatile Applications: While drywall is primarily for interior walls and plywood for structural sheathing, MgO board offers a wider range of applications, including interior and exterior walls, subflooring, tile backing, and fire-rated assemblies.
Installation Considerations: While installation methods are generally similar, MgO board can be heavier than drywall and requires carbide-tipped blades for cutting. Plywood requires specific fasteners for structural applications.
Cost vs. Value: Although the upfront cost of MgO board might be slightly higher than standard drywall or plywood, its long-term benefits in terms of durability, moisture resistance, fire safety, and reduced maintenance can offer significant overall value and cost savings.
Material Overview
Understanding the fundamental composition and characteristics of Magnesium Oxide (MgO) sheathing board, drywall, and plywood is essential before delving into their performance comparisons. Each material brings a unique set of properties to the construction table, influencing their suitability for various applications.
Magnesium Oxide Sheathing Board
Magnesium Oxide board, often referred to as magboard, is a mineral-based sheathing material made from a combination of magnesium oxide, magnesium chloride (or magnesium sulfate), wood fibers (cellulose), and perlite. These components are mixed with water and cured to form a solid, inert board. Its primary binder, magnesium oxide, is a naturally occurring mineral. MgO boards are typically lightweight, yet incredibly strong, and come in various thicknesses and finishes. They are generally produced using a manufacturing process that requires less energy than Portland cement.
Drywall
Drywall, also known as gypsum board or plasterboard, is a common construction material used for interior walls and ceilings. It consists of a core of gypsum plaster pressed between two sheets of thick paper. Gypsum is a soft sulfate mineral. Drywall is relatively easy to cut and install, providing a smooth surface ready for painting or other finishes. It is widely used due to its affordability and ease of workability, but it is known for its susceptibility to moisture damage and mold growth if not properly protected.
Plywood
Plywood is a widely used wood product consisting of multiple thin layers (plies) of wood veneer glued together with adjacent layers having their wood grain rotated up to 90 degrees to one another. This cross-graining technique improves strength and reduces shrinkage, making plywood a very stable and strong material for its weight. Plywood is commonly used for structural sheathing, subflooring, roofing, and various other construction and woodworking applications. Its properties vary based on the type of wood used, adhesive, and grade.
Material Overview Comparison Table
Feature |
Magnesium Oxide (MgO) Board |
Drywall (Gypsum Board) |
Plywood |
Primary Composition |
Magnesium Oxide, Magnesium Chloride/Sulfate, Cellulose Fibers, Perlite |
Gypsum plaster core, paper facing |
Multiple layers of wood veneer, adhesive |
Typical Use |
Interior/Exterior walls, ceilings, subflooring, tile backer, fire-rated assemblies |
Interior walls and ceilings |
Structural sheathing, subflooring, roofing, general construction |
Density |
Medium to High (varies by product) |
Low to Medium |
Medium (varies by wood type) |
Workability |
Requires carbide-tipped blades for cutting, score and snap possible |
Easy to cut, score and snap |
Requires saws for cutting, can splinter |
Texture/Finish |
Smooth, uniform surface, sometimes with a slight texture |
Smooth, paper-faced surface ready for finishing |
Wood grain, can be smooth or rough depending on grade |
Eco-Friendly Aspects |
Mineral-based, lower energy manufacturing, recyclable |
Gypsum is natural, but paper facing and some additives |
Renewable resource (wood), but adhesive can be petroleum-based |
Moisture Resistance
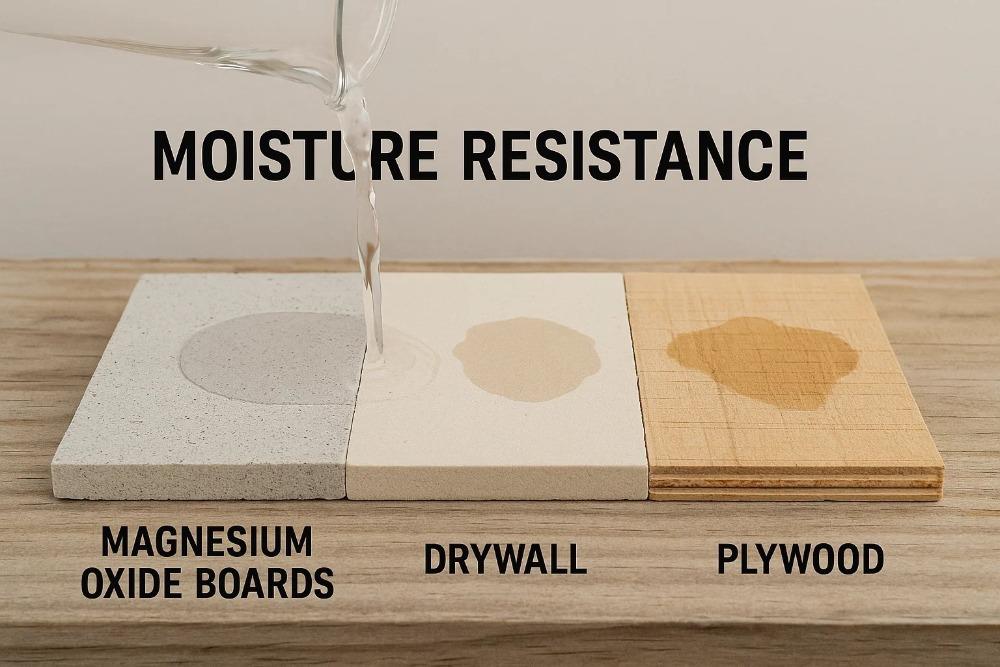
Moisture resistance is a critical factor in material selection, particularly in areas prone to humidity, direct water exposure, or where there's a risk of leaks. The ability of a sheathing material to resist water absorption, prevent mold growth, and maintain structural integrity in damp conditions directly impacts the longevity and health of a building.
Magnesium Oxide Boards
Magnesium Oxide (MgO) boards exhibit exceptional moisture resistance, setting them apart from many traditional building materials. Their inherent mineral composition makes them largely impervious to water absorption. Unlike gypsum or wood-based products, MgO boards do not swell, warp, or delaminate when exposed to moisture. This characteristic also makes them highly resistant to mold, mildew, and fungi growth, which are common issues in damp environments and can lead to structural damage and health problems. This makes MgO board an excellent choice for wet areas such as bathrooms, kitchens, basements, and for exterior applications where weather exposure is a concern.
Drywall
Standard drywall, while widely used for interior applications, has very poor moisture resistance. Its gypsum core readily absorbs water, leading to softening, crumbling, and a loss of structural integrity. Once wet, drywall becomes an ideal breeding ground for mold and mildew, often necessitating complete replacement. While moisture-resistant drywall (green board) and paperless drywall offer some improved performance, they are not waterproof and still susceptible to damage in prolonged wet conditions. They are typically only recommended for areas with intermittent moisture exposure, not direct water contact.
Plywood
The moisture resistance of plywood varies significantly depending on the type of wood, the adhesive used, and whether it has been treated. Standard interior-grade plywood uses water-soluble adhesives and will delaminate, swell, and lose strength when exposed to moisture. Exterior-grade plywood (like marine-grade plywood or certain treated panels) uses waterproof adhesives and is designed to withstand a degree of moisture exposure without delaminating. However, even exterior plywood can still absorb water into its wood fibers, which can lead to swelling, warping, and eventually rot and mold if constantly wet or poorly ventilated. It does not offer the inherent mold resistance of MgO board.
Moisture Resistance Comparison Table
Feature |
Magnesium Oxide (MgO) Board |
Drywall (Gypsum Board) |
Plywood |
Water Absorption |
Extremely low; inherently non-absorbent |
High; rapidly absorbs water, leading to degradation |
Varies by grade; can absorb water, leading to swelling and delamination |
Swelling/Warping |
Negligible; maintains dimensional stability |
High; swells, sags, and warps significantly when wet |
Moderate to High; can swell and warp, especially interior grades |
Mold/Mildew Resistance |
Inherently resistant; inorganic composition does not support growth |
Very poor; ideal breeding ground for mold when wet |
Moderate; susceptible to mold and rot when persistently wet |
Delamination |
Does not delaminate |
Not applicable (core disintegrates) |
High for interior grades; low for exterior/marine grades |
Suitability for Wet Areas |
Excellent (bathrooms, kitchens, basements, exterior) |
Poor (standard); Limited (moisture-resistant "green board") |
Varies; Poor for interior grades; Moderate for exterior/marine grades |
Fire Resistance
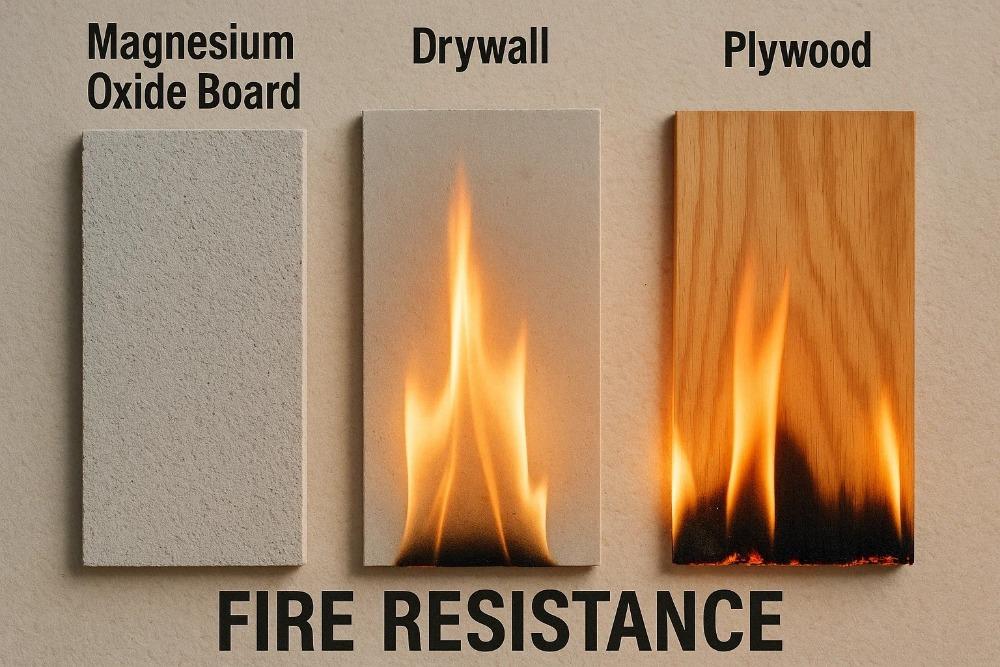
Fire resistance is a paramount safety consideration in building construction. The ability of a material to withstand fire, prevent flame spread, and maintain structural integrity during a blaze can significantly impact the safety of occupants and the extent of property damage.
Magnesium Oxide Board
Magnesium Oxide (MgO) board stands out for its exceptional fire resistance. It is inherently non-combustible and has a very high melting point, typically able to withstand temperatures exceeding 1000°C (1800°F). When exposed to fire, MgO board does not release toxic fumes, smoke, or melt. Instead, it maintains its structural integrity for extended periods, acting as an effective fire barrier. This property helps to compartmentalize fires, limit their spread, and provide valuable time for evacuation and firefighting efforts, often surpassing the fire ratings of conventional building materials.
Drywall
Standard drywall offers good fire resistance, primarily due to its gypsum core. Gypsum contains chemically combined water (approximately 21% by weight). When exposed to high temperatures, this water is released as steam, a process called calcination, which helps to cool the surface and slow down heat transfer. This "fire-retardant" property makes drywall a widely accepted material for fire-rated assemblies. However, once the calcination process is complete and all the water has evaporated, the gypsum core begins to break down. While it slows fire spread, it will eventually succumb to prolonged fire exposure and does not offer the same level of integrity as MgO board.
Plywood
Plywood, being a wood-based product, is inherently combustible. While treated plywood (fire-retardant treated plywood, or FRT plywood) is available and designed to reduce flame spread and smoke development, untreated plywood will ignite and contribute fuel to a fire. The rate at which it burns depends on its thickness, density, and the presence of any fire-retardant treatments. In a fire, plywood will char and eventually lose its structural integrity, unlike the non-combustible nature of MgO board and the fire-slowing properties of gypsum. For applications requiring specific fire ratings, untreated plywood is generally not suitable without additional fire-rated layers.
Fire Resistance Comparison Table
Feature |
Magnesium Oxide (MgO) Board |
Drywall (Gypsum Board) |
Plywood |
Combustibility |
Non-combustible (Class A fire rating) |
Non-combustible (gypsum core) |
Combustible (wood-based); can be treated to be fire-retardant |
Flame Spread Rating |
Extremely low; typically Class A (0) |
Very low; typically Class A |
Varies; Untreated is high; FRT is low |
Smoke Development |
Negligible; does not produce toxic smoke or fumes |
Low; can produce some smoke from paper facing |
Varies; can produce significant smoke and toxic gases |
Structural Integrity in Fire |
Maintains integrity for extended periods; acts as fire barrier |
Retains integrity for a period due to calcination, then degrades |
Loses integrity and burns; contributes to fire load |
Resistance to High Temperatures |
Extremely high; withstands over 1000°C (1800°F) |
Good; releases water to cool, then breaks down |
Poor; ignites and chars |
Role in Fire Safety |
Primary fire barrier; containment |
Fire slowing; contributes to fire-rated assemblies |
Fuel source (unless treated); requires additional barriers |
Durability and Strength
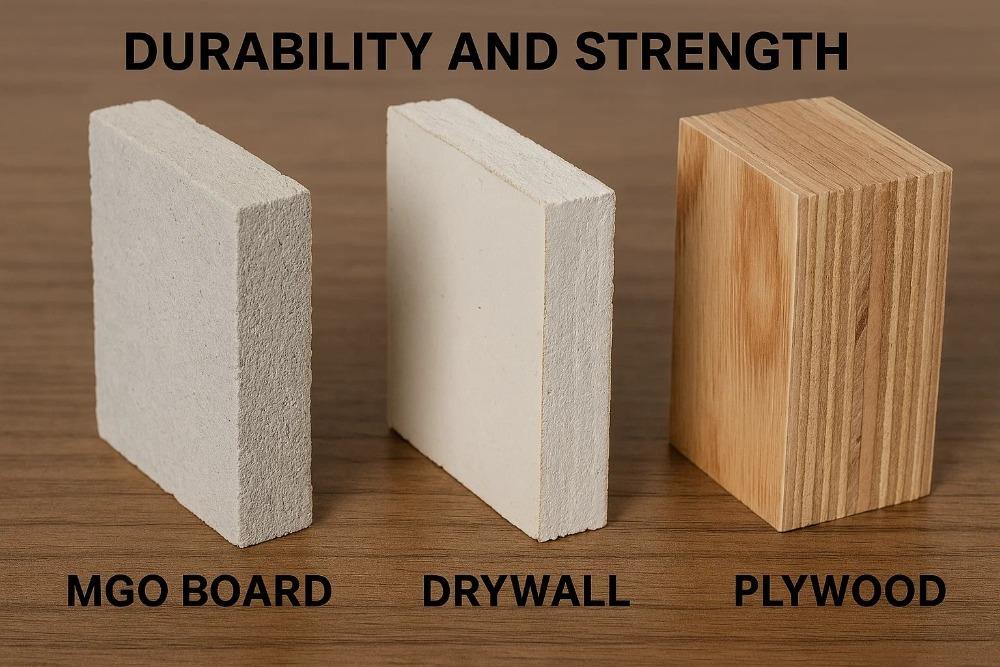
The durability and strength of a sheathing material directly influence a structure's long-term integrity, resistance to impact, and ability to withstand daily wear and tear. These characteristics are vital for both the structural performance and the longevity of interior and exterior surfaces.
MGO Board
Magnesium Oxide (MgO) board offers impressive durability and strength, making it a robust alternative to traditional materials. It possesses high compressive and flexural strength, meaning it can withstand significant pressure and bending forces without cracking or breaking. This inherent strength contributes to its resistance against impact damage, making it less prone to dents and holes compared to drywall. MgO board also maintains its dimensional stability well, resisting expansion, contraction, and warping due to changes in temperature or humidity, which further contributes to its long-term durability. Its uniform composition also makes it less susceptible to delamination or material breakdown over time.
Drywall
Drywall, while widely used for interior finishes, is relatively fragile in terms of impact resistance. It is prone to dents, holes, and scratches from everyday impacts. While easy to repair, frequent repairs can be a nuisance. Its strength relies heavily on its installation, particularly on the spacing of studs and proper fastening. In terms of overall structural contribution, standard drywall offers minimal shear strength to a building's frame; its primary role is as a surface finish. When exposed to moisture, its strength rapidly deteriorates, as discussed in the previous section.
Plywood
Plywood is renowned for its excellent structural strength and durability, particularly for its weight. The cross-grained layering of veneers distributes stress evenly, making it highly resistant to splitting, cracking, and warping under normal conditions. It offers significant shear strength, making it a crucial component in bracing and stabilizing building frames against lateral forces like wind and seismic activity. Plywood's strength and impact resistance vary with its thickness and grade, with thicker and higher-grade panels offering superior performance. However, as a wood product, it can be susceptible to rot, insect damage, and delamination if persistently exposed to moisture, and its surface can be abraded or dented with heavy impact.
Durability and Strength Comparison Table
Feature |
Magnesium Oxide (MgO) Board |
Drywall (Gypsum Board) |
Plywood |
Impact Resistance |
High; resistant to dents, holes, and shattering |
Low; prone to dents and holes |
High (varies by thickness/grade); can dent or abrade |
Compressive Strength |
High |
Low |
High |
Flexural Strength |
High |
Low |
High |
Dimensional Stability |
Excellent; minimal expansion/contraction with temperature/humidity |
Poor when wet; good when dry |
Good (less warping than solid wood); can swell/shrink with moisture |
Resistance to Cracking |
High |
Moderate; can crack at joints or from building movement |
High; resistant to splitting |
Resistance to Delamination |
Does not delaminate |
Not applicable (core disintegrates) |
Low for interior grades; High for exterior/marine grades |
Overall Durability |
Excellent; long-lasting and robust |
Moderate (in dry conditions); Poor (in wet conditions) |
Excellent (especially for structural applications) |
Structural Contribution |
Provides shear strength; can be used structurally |
Minimal structural contribution; primarily a surface finish |
Significant; provides shear strength and bracing |
Environmental Impact
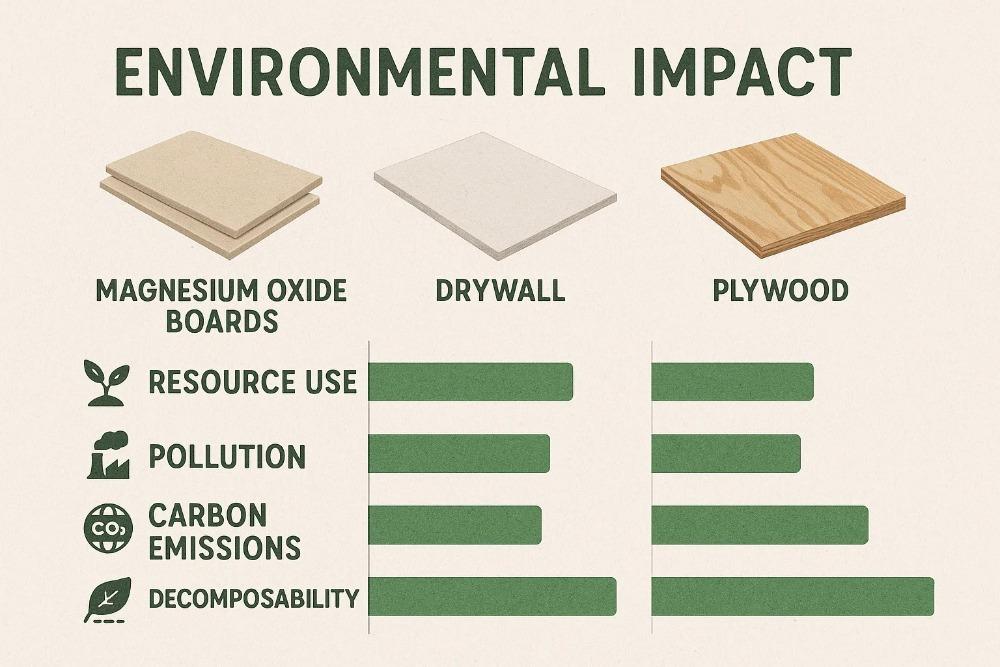
The environmental impact of building materials is an increasingly important consideration in construction. This includes evaluating aspects such as resource depletion, energy consumption during manufacturing, waste generation, and the presence of harmful substances throughout a material's lifecycle.
Magnesium Oxide Boards
Magnesium Oxide (MgO) boards are generally considered an environmentally friendly building material. The primary raw material, magnesium oxide, is derived from abundant natural minerals. Its manufacturing process typically requires significantly less energy and produces fewer CO2 emissions compared to the production of Portland cement, which is a key component in many conventional construction materials. MgO boards are also often free from harmful chemicals such as formaldehyde, asbestos, and silica, which can be found in some traditional boards. They are non-toxic, recyclable, and contribute to healthier indoor air quality, making them a strong choice for green building initiatives.
Drywall
The environmental impact of drywall is mixed. While gypsum is a natural mineral, its extraction can have localized environmental effects. The manufacturing process for drywall involves calcining gypsum, which is energy-intensive. Furthermore, standard drywall often uses paper facers and some additives, and the material itself is not easily recyclable in many regions, leading to significant landfill waste. When drywall gets wet and grows mold, it often ends up in landfills, contributing to waste. While some recycled content can be incorporated, the overall lifecycle assessment reveals areas for improvement, particularly regarding landfilling and energy consumption.
Plywood
Plywood's environmental impact largely depends on the source of the wood and the type of adhesive used. If sourced from sustainably managed forests (certified by organizations like FSC), wood is a renewable resource, making plywood a relatively environmentally sound choice. However, conventional plywood often uses formaldehyde-based adhesives (like urea-formaldehyde), which can off-gas volatile organic compounds (VOCs) into indoor environments, affecting air quality. Low-VOC or formaldehyde-free adhesives are available but are not always standard. The energy consumed in manufacturing plywood, from logging to veneer slicing and pressing, is also a factor. While plywood is biodegradable, its breakdown can be slow, and treated plywood can release chemicals into the soil upon decomposition.
Environmental Impact Comparison Table
Feature |
Magnesium Oxide (MgO) Board |
Drywall (Gypsum Board) |
Plywood |
Resource Origin |
Abundant natural minerals (magnesite) |
Natural mineral (gypsum); paper from wood pulp |
Renewable resource (wood) |
Manufacturing Energy |
Lower energy consumption compared to cement-based products |
Moderate to High (calcination process) |
Moderate (logging, veneer production, pressing) |
CO2 Emissions |
Lower emissions during production |
Moderate (from calcination) |
Varies (logging, transport, processing); can be offset by carbon sequestration in wood |
Recyclability |
Recyclable (can be crushed and reused) |
Difficult to recycle in many areas; often landfilled |
Can be repurposed; recyclability depends on adhesives/treatments |
Harmful Chemicals |
Typically free of formaldehyde, asbestos, silica |
Can contain additives; paper facers; some newer products are low-VOC |
Can contain formaldehyde (VOCs) from adhesives; low-VOC options available |
Indoor Air Quality |
Promotes healthy air quality; no off-gassing |
Can off-gas VOCs (especially older types); risk of mold spores |
Can off-gas VOCs from adhesives; mold risk if wet |
Waste Generation |
Low waste during manufacturing; material can be reused/recycled |
Significant landfill waste |
Waste from cutting; can be landfilled |
Overall Environmental Footprint |
Generally considered a green/sustainable choice |
Mixed; improving with newer formulations and recycling efforts |
Varies based on sourcing and adhesive type; potentially sustainable |
Cost and Value
When selecting building materials, the initial purchase price is just one component of the overall financial consideration. It's crucial to evaluate the long-term value, which includes factors like durability, maintenance requirements, potential for future repairs, and the material's contribution to energy efficiency or health benefits.
Upfront Costs
Magnesium Oxide Boards: MgO boards typically have a higher upfront material cost per square foot compared to standard drywall and often slightly more than standard plywood. This is due to their specialized manufacturing process and the benefits they offer. However, their cost has become more competitive as production has scaled and awareness has grown.
Drywall: Standard drywall is generally the most economical option in terms of initial material cost. Its widespread availability and simple manufacturing process contribute to its affordability, making it a budget-friendly choice for interior finishes. Moisture-resistant or specialized fire-rated drywall can be slightly more expensive.
Plywood: The upfront cost of plywood varies significantly based on its type, grade, and thickness. Construction-grade sheathing plywood is often comparable to or slightly more expensive than standard drywall per square foot, while marine-grade or specialty architectural plywood can be considerably more expensive.
Long-Term Value
Magnesium Oxide Boards: The long-term value of MgO boards is high due to their superior durability, moisture resistance, and fire resistance. Their resistance to mold, rot, and impact significantly reduces the need for future repairs or replacement, especially in high-moisture areas or fire-prone environments. This translates into lower maintenance costs and a longer lifespan for the installed material. Additionally, their contribution to better indoor air quality and potential for lower insurance premiums (due to fire resistance) adds to their long-term value.
Drywall: While cheap to install initially, the long-term value of standard drywall can be diminished by its susceptibility to moisture damage and impact. Repairs for holes, dents, and water damage are common, adding to maintenance costs over time. In damp environments, complete replacement due to mold can be a significant expense. Specialty drywall offers improved value in specific scenarios but still lacks the all-around robustness of MgO board.
Plywood: Plywood offers good long-term structural value, particularly when used as sheathing where its strength contributes to the overall stability of the building. Exterior-grade plywood, when properly installed and maintained (e.g., protected from continuous moisture), can last for decades. However, its susceptibility to rot and insect damage if exposed to persistent moisture means that ongoing maintenance or costly replacement might be necessary if environmental conditions are not managed. The long-term value depends heavily on appropriate material selection for the application and proper installation.
Maintenance
Magnesium Oxide Boards: Require very low maintenance. Once installed and finished, their inherent resistance to moisture, mold, and impact means they generally do not require frequent repairs or specialized upkeep.
Drywall: Can require moderate maintenance, particularly for patching holes and repairing water damage. In areas with high traffic or moisture, more frequent attention may be needed.
Plywood: Maintenance requirements for plywood vary. As structural sheathing, it typically requires little direct maintenance once covered. However, if used in exposed applications, it may require regular sealing, painting, or treatment to protect against weathering, rot, and insects.
Cost and Value Comparison Table
Feature |
Magnesium Oxide (MgO) Board |
Drywall (Gypsum Board) |
Plywood |
Upfront Material Cost |
Higher |
Lowest (standard); Moderate (specialty) |
Varies (moderate for standard sheathing; high for specialty) |
Installation Cost |
Comparable to drywall; potentially slightly higher due to weight/cutting tools |
Low; very common and easy to install |
Moderate; requires specific fastening; cutting may be dusty |
Repair Cost |
Low; less prone to damage, simple patching if needed |
Moderate to High (frequent repairs for impacts/water damage) |
Moderate; depends on type of damage and location |
Maintenance Needs |
Very Low |
Moderate (patching, cleaning if mold occurs) |
Moderate (if exposed, requires sealing/painting/treatment) |
Lifespan/Durability Value |
Excellent; long-lasting, resistant to many issues |
Moderate; susceptible to water/impact damage |
Excellent for structural use; good if protected from elements |
Long-Term ROI |
High; reduced replacement/repair costs, fire safety, health benefits |
Variable; can be low if moisture/impact issues are prevalent |
Good; strong structural integrity, but vulnerable if exposed to moisture |
Installation
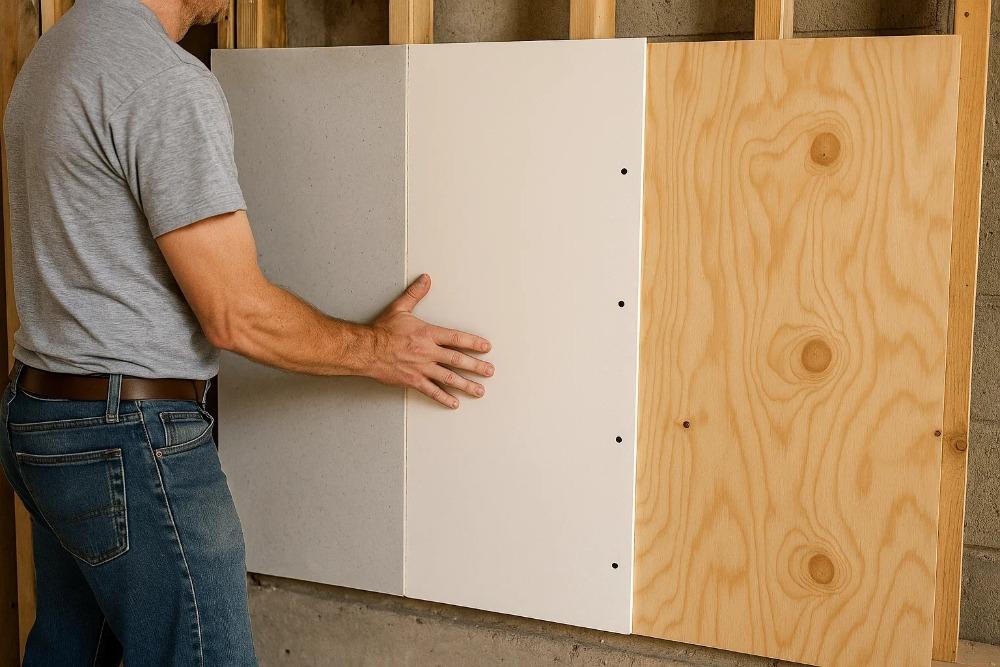
The ease and method of installation are significant practical considerations for any building material, impacting labor costs, project timelines, and the tools required.
MGO Board
Installing Magnesium Oxide (MgO) board shares many similarities with drywall, but with a few key differences. MgO boards can be scored and snapped for cutting, similar to drywall, but due to their density and strength, they often require a heavy-duty utility knife or, for more precise or frequent cuts, carbide-tipped saw blades (like those used for fiber cement board) to ensure clean edges and prolong blade life. They are typically fastened with screws, much like drywall, but the type of screw might need to be corrosion-resistant, especially in wet or exterior applications. While generally rigid, they can be somewhat heavier than standard drywall of the same thickness, which might require an extra hand during installation, particularly for large sheets or ceiling applications. Proper dust collection is recommended when cutting with power tools.
Drywall
Drywall is known for its relatively straightforward and quick installation process, making it a favorite for interior finishes. It is easy to cut by scoring with a utility knife and snapping. Drywall sheets are lightweight and can often be handled by a single person, especially smaller sizes. They are fastened to studs with drywall screws or nails. The main labor-intensive part of drywall installation is the finishing process, which involves taping, mudding (applying joint compound), sanding, and multiple coats to achieve a seamless surface ready for paint. This finishing requires skill and time to achieve a professional look.
Plywood
Plywood installation involves cutting sheets to size using various saws (circular saw, jigsaw, etc.) and fastening them securely with nails or screws. For structural sheathing, specific nailing patterns and fastener types (e.g., common nails or structural screws) are often required by building codes to ensure proper shear strength. Plywood can be heavy, especially larger and thicker sheets, often requiring two people for handling and lifting, particularly for roof decking or exterior wall sheathing. While less "finishing" is typically required than drywall, edges may need sanding, and if exposed, the surface may require sealing or painting. Its rigid nature and robust fastening requirements make it a sturdy material once installed.
Installation Comparison Table
Feature |
Magnesium Oxide (MgO) Board |
Drywall (Gypsum Board) |
Plywood |
Cutting Method |
Score and snap (heavy-duty utility knife); Carbide-tipped saw blades |
Score and snap (utility knife) |
Various saws (circular, jigsaw, table saw) |
Fastening Method |
Screws (corrosion-resistant for wet/exterior) |
Drywall screws or nails |
Nails or screws (specific types/patterns for structural) |
Weight per Sheet |
Moderate to Heavy (can be heavier than standard drywall) |
Light to Moderate |
Moderate to Heavy (varies by thickness/type) |
Handling |
Often requires two people for large sheets |
Can often be handled by one person for standard sheets |
Often requires two people for large/thick sheets |
Finishing Requirements |
Taping and mudding similar to drywall for seamless finish; direct paint/tile possible |
Taping, mudding, sanding (multi-step process for seamless finish) |
Less finishing for structural use; sanding/sealing/painting for exposed use |
Special Tools |
Carbide-tipped blades recommended |
Basic utility knife, drill/driver |
Saws, drill/driver, framing hammer/nail gun |
Learning Curve |
Moderate; similar to drywall but with material differences |
Low; widely understood and practiced |
Moderate; specific structural requirements |
Applications
The diverse properties of Magnesium Oxide (MgO) sheathing board, drywall, and plywood lead to distinct and overlapping applications across various construction sectors. Understanding where each material excels helps in making informed decisions for specific project needs.
Residential
In residential construction, drywall is the undisputed champion for interior walls and ceilings due to its affordability, ease of installation, and smooth finish for paint or wallpaper. It creates comfortable living spaces and serves as a basic fire barrier. Plywood is extensively used for structural components such as subflooring, wall sheathing (providing shear strength against wind and seismic forces), and roof decking. Its strength makes it ideal for these load-bearing applications.
Magnesium Oxide board, while less common historically, is gaining traction in residential settings, particularly where superior performance is desired. Its exceptional moisture resistance makes it an ideal choice for wet areas like bathrooms, kitchens, laundry rooms, and basements, serving as an excellent tile backer board or wall sheathing that won't succumb to mold. Its fire resistance is also a significant advantage for fire-rated walls and ceilings, offering enhanced safety in multi-family dwellings or for enclosing furnaces and water heaters. For homeowners seeking durable, healthy, and high-performance materials, MgO board presents a compelling alternative for interior finishes, particularly in areas prone to dampness or requiring higher impact resistance than drywall.
Commercial
Commercial buildings often have more stringent requirements for fire safety, durability, and sometimes moisture control. Drywall is still widely used for interior partitions and ceilings, especially in office spaces, retail, and hospitality, where aesthetics and quick installation are priorities. Specialized fire-rated drywall is commonly employed to meet strict building codes. Plywood continues its role in commercial construction for structural sheathing, subflooring, and bracing, providing the necessary rigidity and strength for larger structures.
MgO board finds significant application in commercial projects that demand high performance. Its superior fire rating makes it invaluable for firewalls, elevator shafts, stairwells, and other fire-rated assemblies where code compliance is critical. Its moisture and mold resistance are highly beneficial in commercial kitchens, public restrooms, laboratories, and other high-humidity environments, reducing maintenance and health risks. Furthermore, its durability and impact resistance are advantageous in high-traffic areas like corridors, schools, and hospitals, where walls are subjected to frequent wear and tear, reducing the need for costly repairs.
Specialty Uses
Beyond standard residential and commercial applications, each material has niche or specialty uses.
Drywall's flexibility, particularly thinner types, allows it to be used for curved walls and architectural features. Sound-resistant drywall is also a specialty product used in theaters, recording studios, and multi-unit dwellings to reduce noise transmission.
Plywood's versatility extends to furniture construction, cabinetry, boat building (marine-grade plywood), and even concrete formwork due to its strength and ability to hold shape. Specialty plywood types are manufactured for specific uses, such as non-slip flooring for trailers or decorative paneling.
Magnesium Oxide board's unique properties lend themselves to several specialty applications. It is increasingly used for exterior sheathing in areas prone to hurricanes or high moisture, providing a robust, weather-resistant, and non-combustible exterior substrate. Its stability and resistance to chemicals make it suitable for cleanrooms and certain industrial environments. Due to its smooth, stable surface, it can also serve as a substrate for various finishes, including direct painting, plastering, or even as an architectural panel where its inherent properties are an asset. Its resistance to pests and rot also makes it attractive for agricultural buildings or crawl space encapsulations.
FAQ
Here are answers to some frequently asked questions regarding Magnesium Oxide Sheathing Board and its comparison to traditional materials:
Q: What makes magnesium oxide board better for wet areas?
A: Magnesium oxide board is superior for wet areas due to its inherent mineral composition. Unlike gypsum (drywall) or wood (plywood), MgO board does not absorb water readily, swell, warp, or disintegrate when exposed to moisture. Its inorganic nature also makes it naturally resistant to mold, mildew, and fungi growth, which cannot feed on the material. This makes it an ideal choice for bathrooms, kitchens, basements, and exterior applications where moisture is a constant concern.
Q: Can you paint or finish magnesium oxide board like drywall?
A: Yes, magnesium oxide board can be painted, plastered, or finished much like drywall. Its smooth, stable surface accepts a variety of finishes. For a seamless look, the joints typically need to be taped and mudded with a suitable joint compound, similar to drywall installation. Once the finishing is complete, it provides a durable surface ready for your chosen paint or decorative coating.
Q: Is magnesium oxide board safe for people with allergies?
A: Magnesium oxide board is generally considered a safe and healthy building material, particularly for people with allergies. It is typically free from common allergens and irritants such as formaldehyde, asbestos, and silica, which can be found in some traditional building products. Its inherent resistance to mold and mildew growth also contributes to better indoor air quality, reducing the presence of airborne mold spores that can trigger allergic reactions.
Q: How does the cost of magnesium oxide board compare to drywall?
A: The upfront material cost of magnesium oxide board is generally higher than standard gypsum drywall. However, when evaluating the total project cost, especially in areas prone to moisture or requiring higher fire ratings, MgO board can offer significant long-term value. Its superior durability, moisture resistance (reducing future mold remediation or replacement costs), and exceptional fire resistance can lead to lower maintenance, fewer repairs, and potentially even lower insurance premiums, offsetting the initial higher material price over the lifespan of the building.
Q: Can you use plywood instead of magnesium oxide board for exterior walls?
A: Yes, plywood is commonly used for exterior wall sheathing, providing structural bracing for buildings. However, if using plywood for exterior walls, it must be an exterior-grade plywood (e.g., sheathing-grade or structural plywood) that uses waterproof adhesives to prevent delamination. Even so, exterior plywood can still absorb water into its wood fibers, which can lead to swelling, warping, and eventually rot and mold if not properly protected by a weather-resistant barrier and exterior cladding. Magnesium oxide board offers superior inherent moisture, mold, and fire resistance, making it a more robust and maintenance-friendly option for exterior sheathing, especially in very wet climates or for projects demanding non-combustible exterior materials.