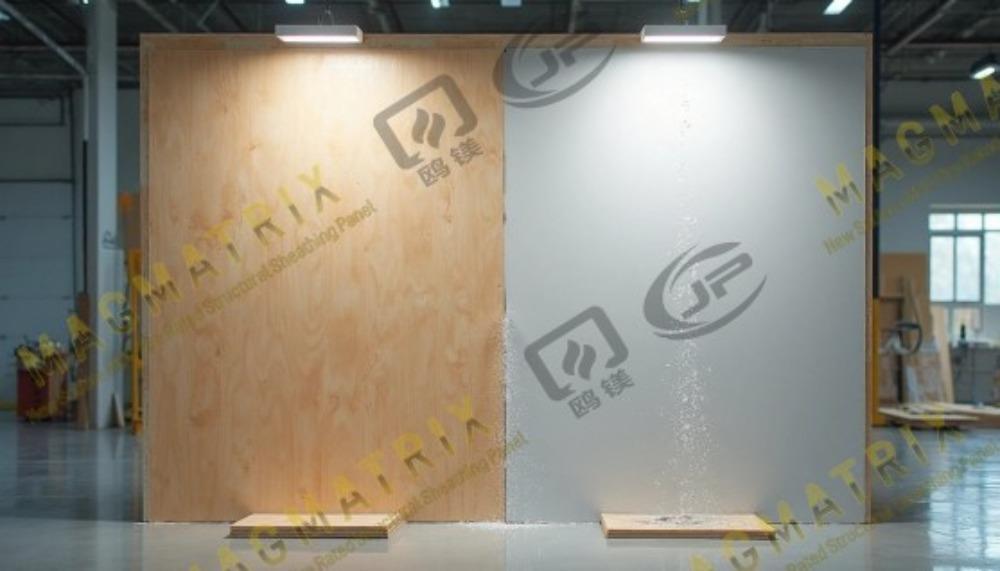
MgO Sheathing Boards are marketed as waterproof building materials - but do they really keep all water out? Many people believe these boards completely repel moisture. Our testing shows a different story. MgO boards are water-resistant but not fully waterproof. This difference matters a lot if you're planning construction projects in areas with moisture issues.
Quality MgO boards hold up well against moisture without warping, swelling, or breaking down. Their strong water resistance makes them perfect for bathrooms, kitchens and humid spaces. But not all magnesium oxide panels deliver the same results. Boards made with magnesium sulfate resist water better over time compared to other types. The magnesium oxide sheathing gives great moisture protection, but water can still seep in after long exposure.
This piece will show you our complete test results about what really happens to MgO sheathing under different moisture conditions. These insights are a great way to get the knowledge you need for your next building project.
Understanding Water Resistance vs Waterproofing in MgO Boards
The difference between water resistance and waterproofing plays a key role when construction professionals choose building materials. My research shows this matters a lot, especially when you have to pick magnesium oxide sheathing boards for places that get wet often.
Definition of Water Resistance in Building Materials
Water resistance means a material can fight off water to some extent—but not completely. Water-resistant materials can handle small amounts of water like light rain and splashes without getting damaged right away. Building materials need techniques and special ingredients that reduce how much water gets through walls, foundations, and joints.
MgO boards represent water-resistant building materials because of how they're made and put together. These boards handle moisture well and stay strong. Unlike materials made from organic stuff, MgO boards keep their shape even when wet. They don't swell up, twist, or fall apart when they touch moisture briefly.
Quality MgO boards show great water resistance:
They barely soak up water and stay strong
Nothing organic means no mold or mildew can grow
They keep their shape even when exposed to moisture
Their softening coefficient stays above 0.90 even after soaking for 180 days
MgO boards dissolve in water at about 0.03g/100g water. This is much better than gypsum (0.2g/100g water) and matches Portland cement (0.084g/100g water). This low dissolving rate helps them work great in wet places.
Why MgO Boards Are Not Fully Waterproof
MgO boards resist moisture well but aren't truly waterproof. Waterproof materials stop water completely—even underwater for long periods. MgO boards, whatever their quality, can't do this.
These boards have some limits to their water resistance:
1.Prolonged Exposure Effects: Quick water contact won't hurt much, but leaving them wet for over an hour can make them expand from the cold. Long moisture contact means MgO boards might soak up water and change shape.
2.Edge Vulnerability: Board edges don't resist water as well as their surfaces. You need extra waterproofing products to seal these edges properly.
3.Formulation Differences: Not every MgO board fights water the same way. Boards with magnesium chloride soak up moisture from humid air because they attract water. This creates "crying boards" where water forms on the surface and drips down with chloride ions, which might rust nearby metal parts. As Jinpeng Group's MagMatrix Brand with the most innovations of the BMSC 517 new sulfate chlorine MGO board formulation that would totally make it as the moisture resistance capability at the application of the exterior fire-rated wall sheathing panel, roofing sheathing, and subfloor sheathing panels.
4.Salt Leaching Concerns: Too much moisture can dissolve chloride salts inside some MgO boards. This creates crystals on the surface, weakening the board.
MgO boards made with magnesium sulfate handle moisture better than those made with chloride. Magnesium sulfate doesn't attract water molecules, so these premium boards fight moisture better. But you still need proper sealing to use them in wet places.
The gap between water-resistant and waterproof materials really shows up in places that stay wet or touch water directly. In spots like swimming pools, saunas, or outside walls in rainy climates, MgO boards might soak up moisture from the air. This leads to water stains, salt deposits, and damage over time.
Water resistance works fine for most indoor spots that get wet now and then. MgO boards work great in bathrooms, kitchens, and basements—places where they stop mold and keep the building strong. These boards don't soak up much water, which helps buildings last longer and stay healthy.
How Formulation Affects Water Resistance
The way magnesium oxide sheathing boards handle moisture exposure depends on their chemical makeup. We need to look at their core formulation to learn about why some MgO boards work better than others in wet conditions. The type of magnesium salt used as a binding agent makes all the difference.
Magnesium Chloride-Based MgO: Hygroscopic Behavior
Traditional magnesium oxide panels use magnesium chloride (MgCl₂) as the main binding agent. This creates magnesium oxychloride cement or Sorel cement, which dates back to 1867. These boards provide decent water resistance at first, but they show major weaknesses in humid environments over time.
The biggest problem with magnesium chloride-based formulations comes from their highly hygroscopic nature. Research shows these boards pull in moisture from the surrounding air. This makes them a poor choice for humid areas. My research reveals that high relative humidity causes these boards to:
Pull in too much water from the air
Create water droplets with high chloride ion concentrations
Get much heavier even in normal outdoor humidity
This moisture-loving behavior creates what we call the "crying board" phenomenon. Lab tests showed the first "tears" on chloride-based boards appeared at 89% relative humidity after they gained 43% weight. The board soaks up so much moisture from the air that water droplets form on its surface, carrying dissolved chloride ions.
Manufacturing defects can make these issues worse by leaving unreacted magnesium chloride (free chlorides) in the board. Traditional MgO panels often contain up to 40% chloride, which creates a high risk of moisture problems. Water exposure breaks down even well-made boards into Mg(OH)₂ and MgCl₂.
Chlorides cause these boards to deliquesce (soak up moisture) when they get wet, which reduces their strength. The boards need the right chloride ratios to handle moisture properly.
Magnesium Sulfate-Based MgO: Improved Moisture Stability
New MgO board formulations use magnesium sulfate (MgSO₄) as the binding agent. This is a big deal as it means that they work much better in humid conditions. Magnesium sulfate doesn't attract and hold water molecules like chloride does.
This different formula creates several benefits:
5.Better moisture resistance: Magnesium sulfate boards don't soak up much water, so they work well in relatively humid places.
6.No crying: MgSO₄-based boards stayed dry even after 2+ years at 30°C and 90% relative humidity.
7.No corrosion: Metal fasteners and frames stay protected because these boards don't contain chloride ions.
8.Stable structure: The boards keep their strength and shape in humid areas, unlike chloride-based products that swell and warp.
Premium magnesium sulfate-based boards contain about 8% chloride, with less than 5% free chloride ions and only 0.2% sulfate. Lower chloride levels associate directly with better performance.
Tests prove this performance difference. Sulfate-based boards started "crying" at 95% relative humidity after seven weeks, gaining about 60% weight. This shows a major improvement over chloride-based products.
Magnesium sulfate-based MgO boards work great in bathrooms and basements without developing moisture issues or damaging nearby materials. Strong bonds between magnesium and oxygen atoms form magnesium oxide crystals (MgO), giving these boards their strength and resistance.
Higher-quality materials make magnesium sulfate boards more expensive, but their excellent moisture performance makes them the best choice where humidity control matters. Notwithstanding that, these improved boards still need proper sealing to work best in consistently wet environments.
Test Methodologies for Water Resistance in MgO Sheathing
Testing the water resistance of magnesium oxide sheathing boards needs standardized methods that predict ground performance accurately. Manufacturers, builders, and regulatory bodies use these procedures to calculate how MgO boards react when exposed to moisture conditions of all types.
Water Absorption Rate Testing (ASTM C1185)
ASTM C1185 stands as the most accessible method to measure water absorption in magnesium oxide panels and offers a standardized way to calculate moisture uptake. The test follows these precise steps:
9.Test specimens dry in an oven at 90°C ± 2°C until they reach constant weight
10.Specimens cool in a desiccator and get weighed to the nearest 0.001 gram
11.Water at 23°C ± 4°C submerges the specimens for 48 hours
12.Specimens come out, get wiped with a damp cloth, and weighed again
Results show up as percentage increase in weight, giving a clear measure of water absorption capacity. High-quality magnesium oxide sheathing boards absorb less than 10% water by mass during the two-hour immersion period. This performance matches gypsum panels and is a big deal as it means that wood-based panels absorb 20% more water.
Premium MgO boards must meet quality control standards with water absorption rates no higher than 0.34% by weight. Low absorption rates associate directly with a board's strength in damp environments.
Freeze-Thaw Cycle Durability
Regions with temperature fluctuations need freeze-thaw cycling tests. These tests simulate seasonal weather conditions that might damage building materials.
ASTM C666, Procedure B guides the testing of MgO sheathing for non-roof applications. The testing protocol needs:
4 by 12 inches (102 mm × 305 mm) test samples
Repeated freezing and thawing cycles
Evaluation for damage after cycle completion
5 or more specimens to ensure valid statistics
Durable magnesium oxide boards show no damage after 25 complete freeze-thaw cycles. Top-tier MgO boards stay remarkably stable during these tests because of their unique physical structure. The board's porous, sponge-like texture stops internal damage during freezing as water doesn't fill its pores completely, leaving room for expansion.
Premium magnesium oxide sheathing handles up to 50 freeze-thaw cycles with only 0.5% strength loss, well under the 18% allowed threshold. This unique durability makes quality MgO boards perfect for climates where temperatures change often.
Surface Condensation Observation
Surface condensation tests reveal long-term performance best, especially in identifying the "crying board" issue that affects some magnesium oxide panels.
Two main methods are used:
Humidity Chamber Testing: Controlled humidity chambers at 90% or higher relative humidity hold test specimens. Changes become visible over a 15-day period. This test shows if boards will weep moisture in high-humidity environments.
Water-Soluble Chloride Test: Ground MgO board powder sits in sealed jars with distilled water for quick results. After 24 hours, chloride content testing begins. Boards likely to have issues in humid environments show up in this test.
Quality magnesium oxide sheathing stays free of "salty tears" on its bottom surface at 30-35°C with 90-95% humidity for 72 hours. Premium products show no halogenation even after 90 days of testing.
These standard tests provide data about different magnesium oxide formulations' performance in various moisture conditions. MOCA (Magnesium Oxide Cement Association) recommends buying boards from trusted suppliers who provide current test reports for leachable ion content and material property tests.
Quality boards with proper formulation deliver excellent moisture resistance for many challenging applications, though no MgO board achieves complete waterproofing.
Observed Effects of Prolonged Moisture Exposure
Field testing has revealed concerning patterns in magnesium oxide sheathing boards that face long-term moisture exposure. Research institutions around the world have documented these behaviors in various humidity conditions. Their findings give construction professionals valuable insights.
Swelling and Warping in Chloride-Based Boards
Chloride-based MgO boards become unstable in highly humid environments. Field studies confirm that boards with magnesium chloride can hold four times more water when relative humidity rises from 50% to 80%. This much moisture causes the boards to physically deform.
Traditional magnesium oxychloride (MOC) boards look stable at first. However, moisture exposure over time makes them expand and warp, which affects their structural profile. This happens because magnesium chloride pulls moisture from the air. Magnesium sulfate-based boards work better - they stay stable even in humid conditions.
Danish research found systemic failures in buildings that used chloride-heavy MgO panels. The situation became so bad that they had to replace boards in 82 public buildings and nearly 12,000 homes. Repair costs reached almost 1 billion DKK. The biggest problem is that these issues often stay hidden until major damage occurs.
Efflorescence and Salt Leaching
MgO boards face a distinctive moisture-related issue - efflorescence. This creates powdery white deposits on board surfaces. Water dissolves mineral salts inside the board structure and brings them to the surface as it evaporates.
The "crying board" phenomenon represents the worst of these moisture problems. Lab tests found this mainly in magnesium oxychloride boards that contained excess unreacted MgCl₂. Scientists observed:
Water droplets appearing on board surfaces
Salty solution that looks like tears running down walls
Boards started "crying" at 89% relative humidity after gaining 43% mass
These issues create both visual and practical problems. The leaching starts when relative humidity goes above 84%, which causes MgO boards to absorb too much moisture. Boards with high levels of free chlorides cause the most trouble, often due to poor manufacturing quality that leaves unreacted magnesium chloride in the board structure.
Structural Integrity Loss Over Time
Long-term moisture exposure breaks down the board's internal structure. High humidity breaks down binding agents and weakens the board's basic strength.
The Technical University of Denmark found that MOC boards lose their cohesion as their binder breaks down at humidity levels above 95%. This process turns the solid material into Mg(OH)₂ and MgCl₂, which speeds up deterioration.
Construction applications face an even bigger challenge - moisture-induced degradation affects other building components. The salty solution from leaching attacks metal parts throughout the building. Studies show:
0.8mm zinc flashings completely corrode within 1-2 years
Electro galvanized steel profiles, nails and screws corrode to base steel in 1-2 years
Only stainless steel (A2 and A4 grade) stays undamaged
The effects spread to nearby materials. Wood parts next to deteriorating MgO boards soak up chloride-filled moisture, which spreads corrosive elements through the structure. Australian studies report similar damage - cracking, bulging walls, and dampness.
Some boards handle moisture better than others. Research shows that all but one-third of tested boards cried under similar exposure conditions. This varies based on raw material composition, curing conditions, mineral stability, and physical board properties. These findings highlight why manufacturing quality matters for long-term performance.
The 'Crying Board' Phenomenon Explained
The mysterious "crying board" phenomenon is one of the biggest problems we see in certain types of magnesium oxide sheathing boards. These boards develop water droplets on their surfaces after installation in buildings. People call them "crying" or "weeping" boards. Scientists started studying this issue after extensive documentation in European buildings to understand why it happens and what risks it creates.
Surface Condensation and Chloride Ion Migration
Chemical composition causes the crying behavior in magnesium oxide sheathing boards - not external leaks as many people think. Research shows this happens almost exclusively in boards that use magnesium oxychloride cement (MOC) as their binding agent. The process works through several connected mechanisms:
Poorly manufactured boards contain unreacted magnesium chloride (MgCl₂), which creates the problem at the molecular level. This compound pulls moisture from surrounding air because of its hygroscopic properties. The boards start absorbing significant atmospheric moisture when relative humidity goes above 84%.
The moisture dissolves excess MgCl₂ and creates a concentrated salt solution inside the board. This solution moves to the board surface through capillary action and forms visible droplets with high chloride ion concentrations. When panels are installed vertically, these droplets collect at the bottom edges, looking like tears running down a face.
Manufacturing issues make this worse:
Wrong magnesium-to-chloride ratios during production
Not enough curing time to complete chemical reactions
Skipping proper post-processing soaking to remove excess chlorides
Magnesium oxysulfate (MOS) boards handle moisture much better. Studies showed MOS boards stayed dry even after two years at 90% relative humidity and 30°C. This shows how the right formula determines moisture performance.
Impact on Metal Corrosion and Esthetics
The crying board phenomenon creates serious functional issues beyond just looking bad. The high concentration of chloride ions in these tears causes aggressive corrosion in nearby metal parts.
Corrosion happens in several ways. Free chloride ions (Cl⁻) easily penetrate and disrupt the protective oxide films that usually protect metal surfaces. This starts localized electrochemical corrosion that creates small but deep holes, weakening structural integrity.
Field studies revealed severe metal damage:
0.8mm zinc flashings completely corroded in 1-2 years
Electro-galvanized steel profiles, nails and screws rusted through to base steel just as quickly
All but one of these metals failed - only stainless steel components (grades A2 and A4) resisted this chloride-induced corrosion. The risk extends to structural framing members and could affect building safety over time.
The boards create more esthetic problems as chloride-laden moisture evaporates. It leaves behind white crystalline formations through efflorescence. These deposits show up on board surfaces, nearby materials, and painted finishes. The constant moisture also creates perfect conditions for mold growth in organic building materials like wood framing.
The crying board phenomenon shows us a materials science challenge - we need to balance binding chemistry with environmental resilience. The solution requires either new formulas with magnesium sulfate binders or better quality control to ensure proper magnesium-to-chloride ratios and removal of unreacted compounds.
Building professionals need to know the difference between MgO formulations. These differences affect long-term building performance and durability significantly.
Comparative Performance: MgO vs Plywood, Gypsum, and Cement Boards
Building professionals must make vital decisions about sheathing materials suitable for moisture-prone environments. A comparison between magnesium oxide sheathing boards and traditional alternatives shows key differences in how they perform.
Water Absorption in Plywood and Gypsum
MgO boards and other materials show striking differences in moisture absorption. MgO boards' surface moisture absorption stands at just 0.34%, nowhere near gypsum board's higher 3% absorption rate. This difference greatly affects how vulnerable these materials are to water damage in humid environments.
Immersion testing reveals even bigger gaps:
MgO boards: Less than 10% absorption after 24 hours
Gypsum boards: Up to 30% absorption
Plywood: Over 40% absorption
Numbers tell only part of the story. MgO boards dry completely in about four days after reaching moisture saturation. Plywood and OSB need almost 25 days to return to normal. This quick moisture management helps avoid structural issues that plague wood-based panels, which often warp, swell, or delaminate after exposure to water.
Installation and Handling Differences with Cement Boards
Cement boards resist water well but need extra sealing to stay protected long-term. Without proper sealing, these boards might absorb water and crack under extreme conditions.
MgO boards streamline installation in several ways:
Their lighter weight reduces worker fatigue
Workers need only simple tools instead of specialized cutting equipment
Lighter materials improve safety and speed up work
Cement boards weigh more than MgO panels and take more effort to install. Installation costs rise because of longer installation times and extra labor needs.
Fire and Mold Resistance Comparison
MgO panels outshine traditional materials in fire protection. These boards withstand temperatures up to 1200°C without releasing harmful gasses and keep their structural integrity even in extreme heat. They outperform gypsum board, which offers fire resistance but can't handle such high temperatures.
Plasterboard's highest test level reaches only about 30 minutes at temperatures below 900°C. MgO boards that are 7mm thick can resist fire for at least one hour in any condition.
MgO boards handle moisture-prone environments better than other options. Their mineral-based cement composition helps them stay stable when exposed to moisture. On top of that, these boards contain no organic materials that could feed mold spores, which stops fungal growth before it starts.
Quality magnesium oxide sheathing proves superior where moisture resistance, fire safety, and structural integrity matter most.
Enhancing Water Resistance Through Sealing and Coating
Quality sealing and coating help maximize moisture protection for magnesium oxide sheathing boards. MgO boards need extra barriers against water intrusion, especially at edges and joints, even when they're high quality.
Silicone-Based Sealants for Edge Protection
MgO boards are most vulnerable to moisture at their exposed edges. You should apply high-quality edge sealers or primers made specifically for magnesium oxide panels. Neutral-curing (non-acidic) silicone sealants create an effective weather barrier and protect nearby building components.
The perimeter needs silicone sealant right after final pressure application for exterior installations. Quick sealing protects VHB tape and other fastening systems from harsh cleaning agents while stopping moisture from getting in.
Acrylic and Polymer Coatings for Surface Treatment
Surface treatments boost the moisture resistance of magnesium oxide sheathing substantially. Here are coating options with different benefits:
Primers: These are vital for alkaline boards like MagPanel®, making them work well with concrete or masonry surfaces
Acrylic Stucco Topcoats: These create strong, direct finishes that keep moisture out
Polymer Modified Cement Base: This makes boards more moisture-resistant and durable
Specialized Paints: Some formulas react with MgO cement to create UV-resistant protective layers
The boards need suitable primers or sealants after mounting to resist moisture, mold, and environmental factors better. Make sure to follow the manufacturer's instructions and drying guidelines carefully.
Installation Tips to Prevent Water Ingress
Good installation techniques are the foundations of keeping MgO sheathing boards water-resistant:
13.Boards should stay off the ground to avoid standing water
14.Use rust-proof fasteners that won't corrode when touching the alkaline board material
15.Small expansion gaps between boards prevent cracking from natural movement
16.Regular checks help spot leaks or damage early
Exterior applications work best when MgO panels pair with proper water-resistive barriers. This combination helps buildings last longer and stay sustainable while making the most of quality magnesium oxide sheathing's natural water resistance.
These protective steps matter most in bathrooms, basements, and exterior spots where boards face challenges from constant water exposure.
Best Use Cases for Water-Resistant MgO Sheathing
Real-world uses show why water-resistant magnesium oxide sheathing boards are so valuable. The right environment will help these materials last longer and perform better in places with moisture challenges.
Bathrooms and Kitchens
MgO panels work great in interior spaces that get wet often. These boards create a perfect base for bathroom tiles and provide lasting stability. You'll find them ideal for shower surrounds and vanity backsplashes where regular materials might break down.
Kitchen installations stay strong even with cooking steam and water splashes. The boards won't grow mold or bacteria because they're made from inorganic materials - a huge plus for food prep areas. You can install them behind sinks and around plumbing without worrying about the swelling or warping that happens with wood products.
Basements and Utility Rooms
Basement moisture creates unique challenges that MgO boards handle well. These boards keep their shape even in humid conditions. They barely absorb water, which makes them perfect for damp spaces or areas that might flood.
MgO sheathing works wonders in utility rooms with washers, water heaters, and plumbing. The panels stop moisture problems in spots that might leak or get condensation. They create a solid foundation for different types of flooring while blocking ground moisture in basements.
Exterior Walls with Protective Cladding
MgO sheathing needs proper protection for outdoor use to work its best. Quality boards can handle weather exposure for months while waiting for cladding. These boards work best with high-performance water-resistive barriers and proper sealing.
Coastal areas benefit from MgO sheathing's resistance to salt damage. Outdoor applications should include an extra layer of materials or coating systems for the best protection. This combo creates tough exterior walls that resist moisture, fire, and pests.
Conclusion
Our testing has found that magnesium oxide sheathing boards provide excellent water resistance but are not completely waterproof. This difference is vital for builders and contractors who plan projects in moisture-prone environments. Quality MgO boards keep their structural integrity around moisture, though they will absorb some water after long exposure.
The board's performance depends on its composition. Magnesium sulfate-based boards substantially outperform their chloride-based alternatives. These boards show minimal moisture absorption and eliminate the "crying board" issue. Performance tests like ASTM C1185 and freeze-thaw cycling validate these results. High-quality boards resist water absorption below 0.34% and maintain strength after multiple freeze-thaw cycles.
MgO sheathing boards show clear benefits compared to traditional materials. Their moisture resistance beats gypsum board's 3% absorption rate. The boards are also easier to install than cement boards. Silicone-based sealants and acrylic coatings will boost their moisture protection, especially at exposed edges.
These boards work best in bathrooms, kitchens, basements, and protected exterior walls. Such environments benefit from the board's moisture resistance and mold-preventing inorganic makeup.
Smart builders should think over magnesium oxide sheathing as water-resistant rather than waterproof. The quickest way to maximize their performance is through proper installation, edge sealing, and protective coatings. Choose MgO boards made with magnesium sulfate instead of magnesium chloride, especially for high-humidity areas. This approach will give you impressive moisture protection without unexpected limitations in your next construction project.