Key Takeaways
Magnesium Oxide (MGO) sheathing boards are a high-performance, multi-purpose building material.
They offer exceptional fire resistance, often exceeding that of traditional materials.
MGO boards are highly resistant to moisture, mold, and mildew growth.
Their robust composition contributes to superior durability and strength.
The manufacturing process is relatively eco-friendly, contributing to sustainable building practices.
What Is a Magnesium Oxide Sheathing Board?
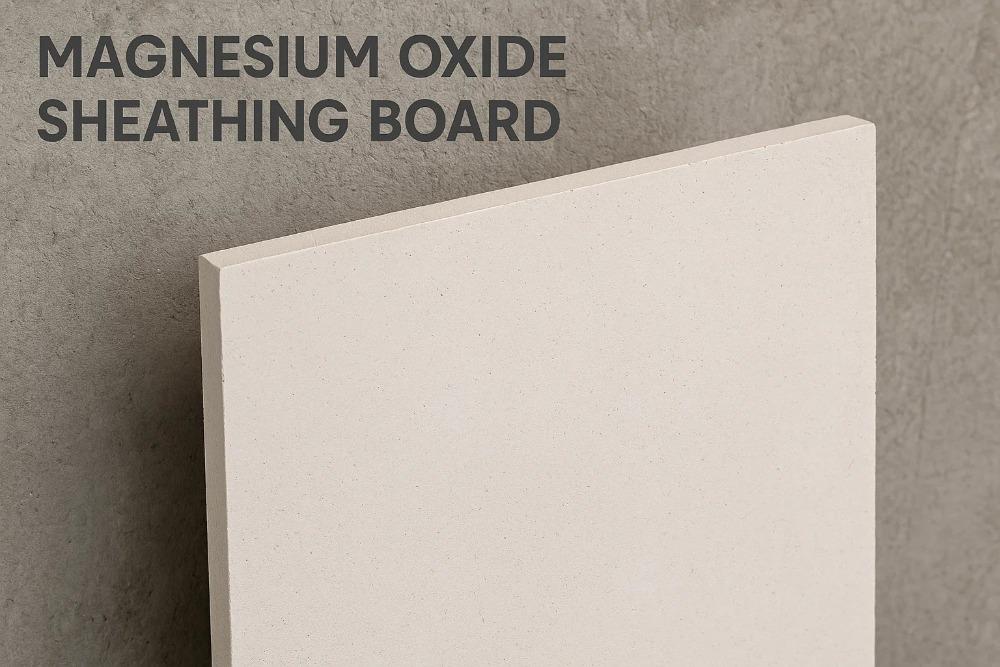
Definition and Uses
A Magnesium Oxide (MGO) sheathing board is a mineral-based, green building material made primarily from magnesium oxide, a naturally occurring mineral. It is a factory-made, non-structural, sheathing panel product with a wide range of uses in construction. MGO boards are designed to serve as a superior alternative to traditional gypsum-based drywall, cement board, fiber cement, and plywood/OSB products. Their versatility allows them to be used in various applications, including:
Exterior sheathing: Providing a durable and fire-resistant layer for external walls.
Interior walls and ceilings: Offering excellent fire protection and moisture resistance for internal partitions and overhead surfaces.
Subflooring: Creating a stable and robust base for various flooring materials.
Tile backing: Serving as a reliable, waterproof substrate for ceramic, porcelain, and natural stone tiles in bathrooms, kitchens, and other wet areas.
Fire-rated assemblies: Integral components in systems requiring specific fire resistance ratings.
Structural insulated panels (SIPs): Used as the sheathing material for enhanced insulation and structural integrity.
Soffits and fascias: Providing durable and low-maintenance finishes for roof overhangs.
Shaft wall enclosures: Forming fire-rated barriers in vertical shafts.
Historical Background
The use of magnesium-based cements in construction is far from a modern innovation. In fact, their history stretches back millennia, predating many of the widely used building materials of today.
Ancient civilizations recognized the beneficial properties of magnesia (magnesium oxide). It was notably used in mortar for the construction of significant structures like the Great Wall of China and by the Romans in their architecture, including potentially components of the Pantheon. These early applications leveraged magnesia for its binding properties and durability.
However, with the advent of the 20th century, the prominence of magnesium-based cements waned. Cheaper alternatives, such as Portland cement, gypsum, and plywood, became widely available, leading to a shift in construction practices. For several decades, MGO-based materials were largely relegated to niche applications, such as high-temperature kiln linings and specialized patching cements.
The resurgence of magnesium oxide boards in the mainstream construction industry began approximately two decades ago. This revival was driven by a growing demand for sustainable, high-performance building materials that addressed issues like fire safety, moisture control, and environmental impact. Modern manufacturing techniques and a deeper understanding of MGO's unique properties allowed for the development of the MGO sheathing boards we know today. Their exceptional benefits quickly propelled them back into contention as a preferred choice for builders seeking durable, eco-friendly, and resilient construction solutions. Notably, MGO boards were extensively used in the construction of the Beijing National Stadium for the 2008 Olympics, highlighting their embrace in major, modern architectural projects.
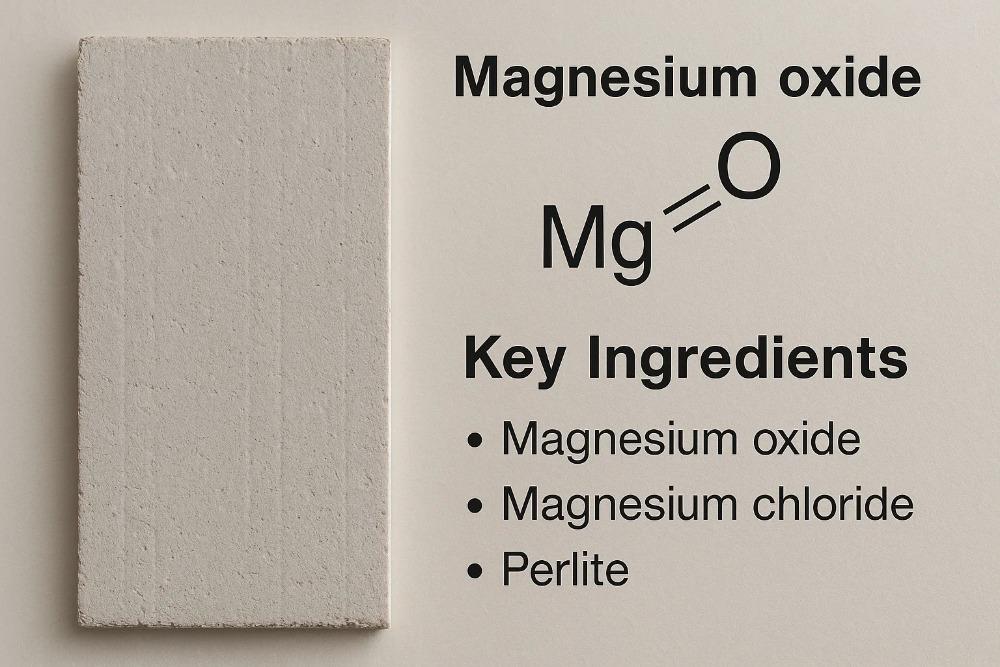
Chemical Structure
Magnesium oxide (MgO), also known as magnesia, is an inorganic compound that occurs as a white solid. Its chemical structure is characterized by an ionic bond between magnesium (Mg) and oxygen (O) atoms. Magnesium, being a metal from Group 2 of the periodic table, readily loses two electrons to form a Mg2+cation. Oxygen, a nonmetal from Group 16, readily gains two electrons to form an O2− anion. These oppositely charged ions are attracted to each other, forming a crystal lattice structure typical of ionic compounds.
The crystal structure of magnesium oxide is similar to that of sodium chloride (rock salt), adopting a cubic crystal system where each Mg2+ ion is surrounded by six O2− ions, and vice versa. This strong ionic bonding contributes significantly to MgO's high melting point (2852°C), hardness, and chemical stability, which are crucial for the performance of MGO boards in various environmental conditions, particularly under high heat or in the presence of moisture. The stability of this structure is key to the material's fire resistance, as it does not readily break down or combust when exposed to flames.
Key Ingredients
While magnesium oxide is the primary binder, MGO boards are composite materials, meaning they are made from a combination of several ingredients that work synergistically to achieve their desired properties. The precise formulation can vary slightly between manufacturers, but the core components generally include:
Magnesium Oxide (MgO): The primary binding agent, typically derived from the calcination of natural magnesite. It reacts with magnesium chloride to form a hydrated magnesium oxychloride cement, which is the main binder that solidifies the board.
Magnesium Chloride (MgCl2): Acts as a crucial reactant with MgO. When dissolved in water, magnesium chloride facilitates the hydration and hardening process, forming the stable magnesium oxychloride cement that binds the other components together. The precise ratio of MgO to MgCl2 is critical for strength and stability.
Perlite: A lightweight, amorphous volcanic glass that is heat-treated to expand. Perlite is added to the mix to reduce the overall weight of the board, improve its insulation properties (both thermal and acoustic), and enhance fire resistance due to its non-combustible nature.
Wood Fibers/Cellulose: Typically in the form of sawdust or other recycled wood fibers, these components act as reinforcement, similar to rebar in concrete. They provide tensile strength, improve impact resistance, and help prevent cracking. The type and amount of fibers influence the board's flexibility and workability.
Fiberglass Mesh: Often embedded within the layers of the board, fiberglass mesh provides additional tensile strength, dimensional stability, and crack resistance. It helps distribute stresses across the board and further enhances its durability.
Other Additives: Minor amounts of other additives may be included to fine-tune specific properties. These can include:
Plasticizers: To improve workability and flow during manufacturing.
Water repellents: To further enhance moisture resistance.
Stabilizers: To control setting time and ensure long-term performance.
The careful proportioning and mixing of these ingredients are vital for producing MGO boards with consistent quality, strength, and the desired range of performance characteristics.
Manufacturing
Production Process
The manufacturing of Magnesium Oxide (MGO) sheathing boards typically involves a multi-step process that combines precise material blending with advanced curing techniques. The goal is to create a homogenous, dense, and durable panel.
Raw Material Preparation:
Magnesium Oxide (MgO): High-purity caustic calcined magnesia is typically used. It is often finely ground to ensure uniform reactivity.
Magnesium Chloride (MgCl2): This is usually supplied as a concentrated aqueous solution.
Aggregates and Fillers: Perlite, wood fibers, and other lightweight aggregates are carefully measured and prepared. Fiberglass mesh is cut to size.
Mixing:
The dry raw materials, including MgO, perlite, and wood fibers, are fed into large industrial mixers.
Simultaneously, the magnesium chloride solution, often diluted to a specific concentration, is introduced into the mixer.
The ingredients are thoroughly mixed to create a homogeneous slurry or paste. The consistency of this mixture is critical for the final board quality.
Forming:
The mixed slurry is then continuously fed onto a conveyor belt or casting machine.
As the material moves, a layer of fiberglass mesh is typically laid onto the top and/or bottom surface of the forming board. This reinforcement is crucial for the board's structural integrity.
Rollers or pressing mechanisms compress the material to the desired thickness, ensuring uniformity and density. This process can be automated, creating a continuous sheet of the MGO mixture.
Initial Setting and Cutting:
Once formed, the green (uncured) board begins to undergo an initial setting reaction, where the magnesium oxide reacts with the magnesium chloride solution to start forming the hydrated magnesium oxychloride cement.
Before it fully hardens, the continuous sheet is cut into standard board sizes (e.g., 4x8 feet, 4x10 feet) using automated cutting saws.
Curing:
The cut boards are then transferred to a controlled curing environment. This is a critical stage where the chemical reaction fully progresses, and the boards gain their final strength and stability.
Curing can occur at ambient temperatures over several days, or in accelerated curing chambers with controlled humidity and temperature to speed up the process. Proper curing prevents warping and ensures the long-term integrity of the board.
Drying and Finishing:
After curing, the boards may undergo a drying process to remove any residual moisture, ensuring dimensional stability and optimal performance.
Finally, the boards are inspected for quality, edges may be trimmed or beveled, and they are typically stacked and packaged for shipment.
Quality Control
Stringent quality control measures are implemented at various stages of the manufacturing process to ensure that MGO boards meet specific performance standards and customer requirements.
Stage |
Quality Control Measure |
Purpose |
Raw Material Input |
Testing of incoming MgO purity, MgCl2 concentration, and aggregate specifications (e.g., particle size, moisture content). |
Ensures that the foundational components meet the required chemical and physical properties for consistent board performance and reactivity. Prevents defects originating from substandard materials. |
Mixing Process |
Regular checks on mix ratios, consistency, and temperature of the slurry. Real-time viscosity measurements. |
Guarantees uniform distribution of all ingredients, optimal chemical reaction conditions, and prevents variations in board density and strength due to improper mixing. |
Forming & Cutting |
Continuous monitoring of board thickness, width, and length. Visual inspection for surface defects, bubbles, or voids. |
Ensures dimensional accuracy for ease of installation and prevents structural weaknesses. Identifies surface imperfections that could affect finish or performance. |
Curing Process |
Monitoring of temperature and humidity within curing chambers. Regular testing of sample board strength at different curing times. |
Ensures that the hydration and hardening reactions proceed correctly, leading to optimal compressive and flexural strength, and prevents warping or internal stresses. |
Finished Product |
Physical Property Testing: |
Confirms the final product meets specified performance criteria for safety, durability, and usability. |
* Flexural Strength (Modulus of Rupture): Measures resistance to bending. |
Indicates the board's ability to withstand loads without breaking, crucial for structural integrity. |
* Compressive Strength: Measures resistance to crushing. |
Important for applications where the board will bear vertical loads. |
* Density: Ensures consistent weight and material content. |
Affects thermal and acoustic insulation properties, as well as handling. |
* Dimensional Stability (Swelling/Shrinkage): Tested under varying humidity. |
Predicts how the board will perform in different environmental conditions, preventing issues like buckling or gaps. |
* Water Absorption: Measures how much water the board absorbs. |
Key for moisture resistance properties and preventing mold growth. |
* Fire Resistance Testing: Conducted periodically on representative samples. |
Verifies that the board meets required fire-rated classifications (e.g., ASTM E84, UL ratings) and ensures safety performance. |
Visual Inspection: Final check for surface finish, edge quality, and overall appearance. |
Ensures aesthetic appeal and ease of installation. |
Properties of Magnesium Oxide Board
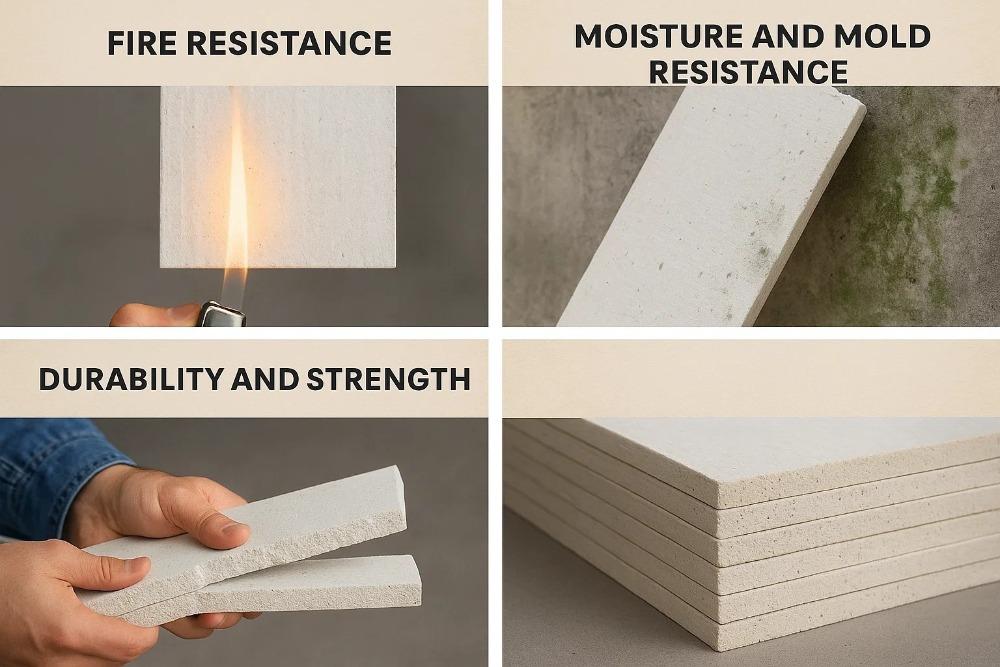
Magnesium Oxide (MGO) sheathing boards possess a unique combination of properties that make them highly desirable in modern construction. These characteristics stem directly from their chemical composition and the robust manufacturing process.
Fire Resistance
One of the most significant advantages of MGO boards is their exceptional fire resistance. This property is primarily due to the inherent non-combustible nature of magnesium oxide and the hydration process that creates magnesium oxychloride cement.
Non-combustible Material: MGO itself is a mineral that does not burn. Unlike wood-based products (like plywood or OSB) or gypsum boards with paper facers, MGO boards do not contribute fuel to a fire.
Thermal Stability: Magnesium oxide has an extremely high melting point (2852°C or 5166°F). This means the board can withstand intense heat for extended periods without degrading, melting, or releasing toxic fumes.
Endothermic Reaction: When exposed to high temperatures, the hydrated compounds within the MGO board undergo an endothermic (heat-absorbing) reaction. This process releases chemically bound water in the form of steam, which effectively cools the surface of the board and creates a fire-resistive barrier. This "cooling" effect delays the temperature rise on the unexposed side of the board, providing more time for evacuation and fire suppression.
No Smoke or Toxic Fumes: Unlike many other building materials, MGO boards do not produce significant smoke or toxic fumes when subjected to fire. This greatly improves occupant safety and visibility during a fire event.
Classification: MGO boards typically achieve a Class A (or Class 1) fire rating according to ASTM E84, which is the highest possible rating for surface burning characteristics. This includes very low flame spread and smoke development indices. They are often critical components in fire-rated wall, floor, and ceiling assemblies, contributing to hourly fire ratings as per standards like ASTM E119 or UL 263.
Moisture and Mold Resistance
MGO boards demonstrate superior performance in environments prone to moisture and offer excellent resistance to mold and mildew growth.
Water Repellency: While not entirely waterproof, MGO boards are highly water-resistant. Their dense, inorganic composition means they do not swell, warp, or delaminate when exposed to moisture, unlike wood-based panels. The magnesium oxychloride cement matrix does not readily absorb liquid water.
Breathability: Despite their water resistance, MGO boards are vapor permeable, meaning they can "breathe." This allows trapped moisture within wall cavities to escape, reducing the risk of condensation and associated problems.
Inorganic Composition: Since MGO boards are made from inorganic minerals, they do not provide a food source for mold, mildew, or other fungi. This inherently prevents biological growth, making them an ideal choice for high-humidity areas like bathrooms, kitchens, basements, and exterior applications.
Dimensional Stability: Their resistance to moisture absorption ensures that the boards maintain their dimensional stability, preventing issues like swelling, shrinking, or warping that can lead to cracking or instability in finishes.
Durability and Strength
MGO boards are renowned for their strength and durability, contributing to the longevity and resilience of structures.
High Compressive and Flexural Strength: The strong ionic bonds within the magnesium oxychloride cement matrix, combined with fibrous and mesh reinforcements, give MGO boards excellent compressive and flexural strength. This allows them to withstand significant loads and impacts without breaking.
Impact Resistance: Their dense and homogeneous structure provides good resistance to impacts, making them less prone to denting or piercing compared to traditional drywall.
Longevity: Due to their inorganic nature, MGO boards are resistant to rot, decay, and insect infestation. They do not degrade over time due to biological factors, contributing to a longer service life for the building.
Thermal Cycling Resistance: MGO boards maintain their integrity across a wide range of temperatures, making them suitable for various climates without concerns about material degradation due to expansion and contraction.
Versatility: Their inherent strength and stability allow them to be used in a wide array of applications, from interior partitions to exterior sheathing, providing a robust and long-lasting solution.
Magnesium Oxide Sheathing Board vs. Other Materials
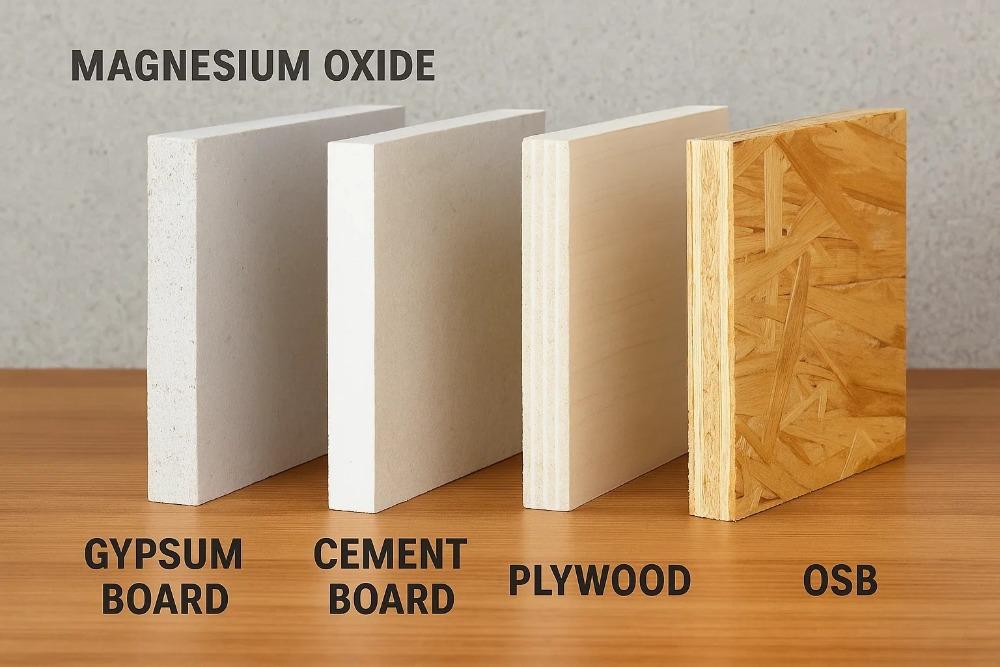
MGO boards offer distinct advantages and disadvantages when compared to conventional building materials. Understanding these differences is crucial for selecting the right material for specific applications.
Gypsum Board
Gypsum board (drywall) is the most common interior wall and ceiling material.
Key Differences:
Fire Resistance: Gypsum boards offer good fire resistance due to the hydrated gypsum core, but MGO often performs better, especially in sustained high-heat situations, and typically achieves higher fire ratings without the need for additional layers in many assemblies. MGO also does not have a paper facing to fuel the fire.
Moisture/Mold: Standard gypsum board is highly susceptible to water damage, swelling, and mold growth. Moisture-resistant gypsum (green board) offers some improvement but is not mold-proof. MGO is significantly more resistant to moisture absorption and inherently mold-proof.
Strength/Durability: Gypsum board is relatively soft and prone to dents and dings. MGO boards are generally denser and more impact-resistant.
Workability: Gypsum board is easier to cut and finish. MGO can be harder to cut and may require specialized tools, and finishing can be more challenging due to differences in surface texture and alkalinity.
Weight: MGO boards can sometimes be heavier than standard gypsum boards of similar thickness, though lightweight MGO versions are available.
Cement Board
Cement board is a durable, water-resistant panel commonly used as a tile backer in wet areas.
Key Differences:
Fire Resistance: Both are non-combustible and offer excellent fire resistance.
Moisture/Mold: Both are highly resistant to moisture and mold. MGO typically has slightly lower water absorption rates.
Strength/Durability: Both are very strong and durable. MGO can sometimes offer better flexural strength for certain applications.
Weight: Cement board is often heavier and denser than MGO, making MGO easier to handle and install.
Alkalinity: Both are alkaline. However, MGO's surface alkalinity can sometimes react with certain finishes or adhesives, requiring primers. Cement board is generally more neutral in this regard.
Workability: Cement board is notoriously difficult to cut and screw, often requiring special tools. MGO is generally easier to cut and faster to install with standard tools.
Plywood and OSB
Plywood and Oriented Strand Board (OSB) are wood-based panels widely used for sheathing, subflooring, and structural applications.
Key Differences:
Fire Resistance: Plywood and OSB are combustible and contribute fuel to a fire. They char and burn, limiting their use in fire-rated assemblies without significant additional layers. MGO is non-combustible.
Moisture/Mold: Plywood and OSB are highly susceptible to moisture damage, swelling, delamination, and mold growth, especially if not properly sealed or if exposed for extended periods. MGO is highly resistant to moisture and mold.
Strength/Durability: Both offer good structural strength. However, MGO's inorganic nature provides superior resistance to rot, insects, and decay, leading to a longer lifespan in many conditions. MGO also offers better impact resistance.
Environmental Impact: While wood is a renewable resource, the production of plywood/OSB often involves resins and glues that can off-gas VOCs. MGO is a mineral-based product with a lower embodied energy and generally considered more eco-friendly.
Key Differences (Table)
Here's a concise comparison of Magnesium Oxide Sheathing Board with other common building materials:
Feature |
Magnesium Oxide Board (MGO) |
Gypsum Board (Drywall) |
Cement Board |
Plywood / OSB |
Primary Composition |
Magnesium Oxide, Magnesium Chloride, Perlite, Wood Fiber |
Gypsum Plaster, Paper Facing |
Portland Cement, Aggregate, Fiberglass Mesh |
Wood Veneers/Strands, Adhesives |
Fire Resistance |
Excellent (Class A/1 Non-combustible, high thermal stability) |
Good (Non-combustible core, paper facing can fuel) |
Excellent (Non-combustible) |
Poor (Combustible, fuels fire, chars) |
Moisture Resistance |
Excellent (Highly resistant to water, no swelling/warping) |
Poor (Standard), Moderate (Green Board), Prone to swelling/damage |
Excellent (Highly water-resistant, no swelling) |
Poor (Highly susceptible to water damage, swelling, delamination) |
Mold Resistance |
Excellent (Inorganic, no food source for mold) |
Poor (Standard), Moderate (Green Board), Prone to mold growth |
Excellent (Inorganic, no food source for mold) |
Poor (Organic, highly susceptible to mold growth) |
Strength/Durability |
Very High (High flexural/compressive strength, impact-res.) |
Low-Moderate (Prone to dents/dings) |
High (Very hard, durable) |
High (Good structural integrity) |
Weight (Relative) |
Moderate-Heavy (Lighter than cement board) |
Light-Moderate |
Heavy |
Light-Moderate |
Workability |
Good (Can be cut with standard tools, can be dusty) |
Excellent (Easy to cut, score, fasten) |
Poor (Hard to cut, requires special tools, screws can strip) |
Good (Easy to cut, nail, screw) |
Sound Insulation |
Good (Dense, mass helps block sound) |
Good (Mass helps block sound) |
Moderate |
Moderate |
Cost (Relative) |
Moderate-High |
Low |
Moderate-High |
Low-Moderate |
Environmental Impact |
Generally Good (Low embodied energy, recyclable) |
Moderate (Gypsum can be recycled, paper facing) |
Moderate (Energy-intensive production, can be recycled) |
Variable (Renewable resource, but often uses formaldehyde-based resins) |
Practical Guide to MGO Board
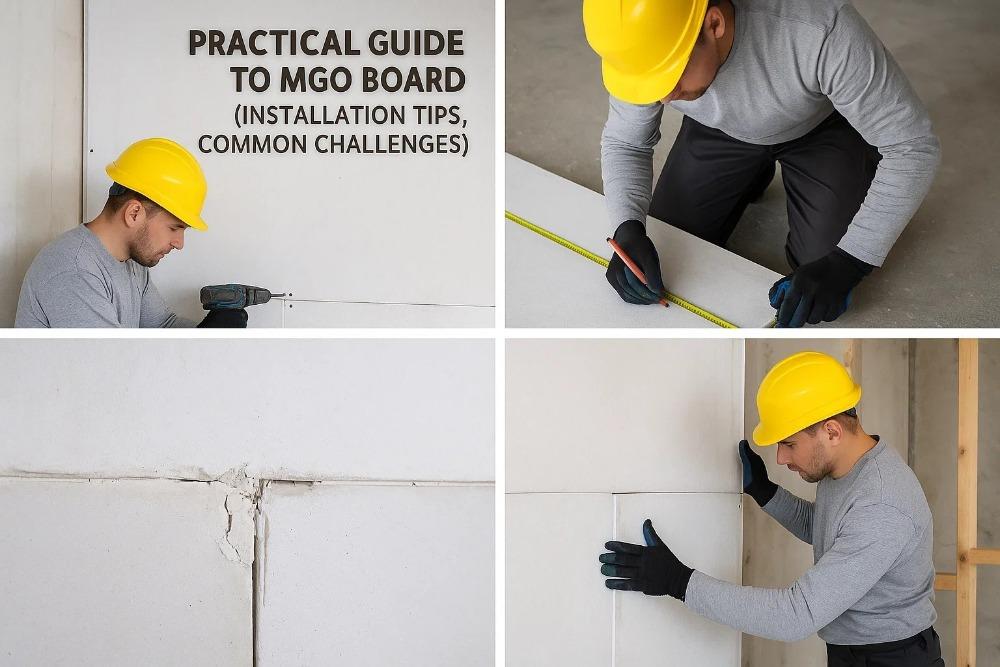
While Magnesium Oxide (MGO) boards offer numerous benefits, proper handling and installation are key to maximizing their performance and ensuring a successful project. Understanding the nuances of working with this material can prevent common issues and optimize its inherent advantages.
Installation Tips
Installing MGO boards shares some similarities with traditional drywall or cement board but also has specific requirements to consider:
Acclimation: Although MGO boards are dimensionally stable, it's a good practice to acclimate them to the job site environment for at least 24-48 hours before installation. This helps ensure they reach equilibrium with the ambient temperature and humidity, minimizing any potential for minor expansion or contraction after installation.
Cutting: MGO boards can be cut using various methods. For straight cuts, a utility knife and straightedge can be used to score and snap the board, similar to drywall. However, due to their density and fibrous reinforcement, a circular saw with a carbide-tipped blade (or a diamond blade for extensive cutting) is often preferred for cleaner, faster cuts, especially for thicker boards. Always use appropriate personal protective equipment (PPE), including dust masks or respirators, and safety glasses, as cutting MGO boards can generate fine dust.
Fastening: MGO boards should be fastened with corrosion-resistant screws, such as galvanized, phosphated, or stainless steel screws. Standard drywall screws are generally not recommended due to their tendency to corrode when reacting with the alkaline nature of MGO over time, which can lead to staining or loss of holding power. Screws should be driven flush with the surface or slightly countersunk. Pre-drilling may be necessary for very thick boards or when fastening close to edges to prevent cracking. The recommended spacing for fasteners typically ranges from 6 to 8 inches along edges and 12 inches in the field, but always refer to the manufacturer's specific guidelines and local building codes.
Framing: Ensure the framing (wood or metal studs, joists) is plumb, level, and square. MGO boards can be installed directly over existing framing. For exterior applications, a weather-resistive barrier (WRB) is often recommended behind the MGO sheathing to provide an additional layer of moisture protection.
Joint Treatment: Joints between MGO boards should be taped and finished. A fiberglass mesh tape, similar to that used for cement board, is typically recommended over paper tape due to MGO's higher alkalinity and moisture resistance. Joint compound specifically formulated for cement board or a polymer-modified thin-set mortar can be used to fill and smooth the joints. Ensure the joint compound is compatible with MGO's alkaline nature to prevent efflorescence or bond failure. Feather the compound smoothly beyond the tape for a seamless finish.
Surface Preparation: Before applying finishes (paint, tile, stucco), the surface of the MGO board should be clean, dry, and free of dust. For painting, a high-quality alkaline-resistant primer is often recommended to ensure good adhesion and prevent potential efflorescence or discoloration, especially with darker paints. For tiling, a suitable thin-set mortar designed for tile-over-MGO or cement board applications should be used.
Expansion Gaps: For large surfaces or exterior applications, consider leaving small expansion gaps between boards (e.g., 1/8 inch) to accommodate any minor movement and prevent buckling. These gaps can be filled with an appropriate sealant or joint compound designed for flexibility.
Common Challenges
While MGO boards offer many benefits, installers may encounter a few challenges:
Dust Generation: Cutting and sanding MGO boards can produce fine, powdery dust. As mentioned, proper ventilation and respiratory protection (e.g., N95 mask) are crucial to prevent inhalation.
Weight: While generally lighter than cement board, MGO boards can still be heavier than standard drywall, especially thicker panels. This may require two-person handling for larger sheets, similar to cement board or heavy plywood.
Alkalinity and Finish Compatibility: The alkaline nature of MGO boards can sometimes react with certain paints, adhesives, or finishes, potentially leading to efflorescence (white powdery deposits) or poor adhesion. This is why using alkaline-resistant primers and compatible finishing materials is strongly emphasized. Always test a small, inconspicuous area first if unsure about compatibility.
Brittleness (if dropped): While strong once installed, the edges and corners of MGO boards can be somewhat brittle and prone to chipping or breaking if dropped or mishandled before installation. Care should be taken during transport and handling.
Fastener Selection: Using the wrong type of screw (e.g., standard drywall screws) can lead to corrosion over time, compromising the fastener's integrity and potentially staining the finished surface. Always use corrosion-resistant screws as recommended by the manufacturer.
Learning Curve: For installers primarily experienced with gypsum board, there might be a slight learning curve regarding cutting techniques, fastening methods, and joint treatment specific to MGO boards. However, the principles are generally straightforward and easily mastered.
Environmental Impact
Magnesium Oxide (MGO) sheathing boards are often lauded as a "green" building material due to several factors related to their production, composition, and performance. Understanding their environmental footprint is crucial for assessing their contribution to sustainable construction practices.
Eco-Friendliness
The eco-friendliness of MGO boards stems from several aspects:
Abundant Raw Materials: Magnesium oxide is derived from magnesite, a naturally occurring and abundant mineral, or from seawater. This contrasts with materials that rely on more finite resources or extensive mining operations. The sheer availability of the raw materials minimizes resource depletion concerns.
Lower Embodied Energy: The manufacturing process for MGO boards typically involves lower embodied energy compared to materials like Portland cement. The primary reaction that forms the magnesium oxychloride cement occurs at relatively low temperatures (often ambient or slightly elevated), significantly reducing energy consumption compared to the high-temperature kilns required for cement production.
Recyclability and Waste Reduction: MGO boards are inorganic and do not contain many of the binders or resins found in wood-based panels, making them potentially recyclable. While infrastructure for MGO board recycling is still developing in many regions, the material can theoretically be crushed and repurposed as an aggregate in other building materials or as a soil amendment. Furthermore, the durability and longevity of MGO boards mean less frequent replacement, reducing construction and demolition waste over the lifespan of a building.
Non-Toxic and Low VOCs: MGO boards are free from asbestos, formaldehyde, crystalline silica, and other harmful chemicals commonly found in some traditional building materials. They produce very low to no volatile organic compounds (VOCs), contributing to healthier indoor air quality. This is a significant advantage for occupants and aligns with green building certifications focused on occupant well-being.
Mold and Mildew Resistance: By inherently resisting mold and mildew growth, MGO boards contribute to a healthier indoor environment and prevent the need for chemical treatments or costly remediation associated with mold issues, thus reducing the use of harmful chemicals over the building's lifecycle.
Energy Efficiency
MGO boards contribute to a building's overall energy efficiency primarily through their insulating properties and ability to create a tight building envelope:
Thermal Insulation Properties: While MGO boards are not designed to be primary insulation materials like foam or fiberglass, their relatively dense and homogeneous composition provides a decent R-value (thermal resistance) compared to their thickness when measured against materials like gypsum board or cement board. When used as sheathing, they contribute to the overall thermal performance of the wall assembly, reducing heat transfer through conduction.
Air Barrier Performance: The dense, rigid nature of MGO boards, when properly installed and sealed at joints, can act as an effective air barrier. Minimizing uncontrolled air leakage (infiltration and exfiltration) is crucial for energy efficiency, as it prevents conditioned air from escaping and unconditioned air from entering. This reduces the load on HVAC systems, leading to lower energy consumption for heating and cooling.
Moisture Management: By resisting moisture absorption and preventing mold growth, MGO boards help maintain the integrity of insulation within wall cavities. Wet insulation loses its effectiveness significantly, leading to higher energy use. MGO's ability to keep the wall cavity dry directly supports the long-term performance of the insulation.
Contribution to High-Performance Envelopes: When integrated into well-designed, high-performance building envelopes, MGO boards can play a role in achieving stringent energy efficiency targets. Their stability and durability also ensure that the envelope maintains its thermal performance over time without degradation.
FAQ
This section addresses some of the most frequently asked questions regarding Magnesium Oxide Sheathing Boards, providing concise and informative answers.
Q: What makes magnesium oxide boards fire resistant?
A: Magnesium oxide boards are inherently fire resistant primarily due to the non-combustible nature of magnesium oxide itself, which does not burn or contribute fuel to a fire. Additionally, the boards contain chemically bound water within their crystalline structure. When exposed to high temperatures, this water is released as steam through an endothermic (heat-absorbing) reaction. This process effectively cools the surface of the board and creates a protective thermal barrier, significantly delaying the spread of fire and the rise in temperature on the unexposed side.
Q: Can magnesium oxide boards get moldy?
A: No, magnesium oxide boards are highly resistant to mold and mildew growth. This is because they are made from inorganic mineral components (magnesium oxide, magnesium chloride, perlite, etc.) which do not provide a food source for mold or fungi. Unlike organic materials such as wood or paper-faced gypsum board, MGO boards do not support biological growth, even in damp conditions. Their excellent moisture resistance also helps prevent the conditions conducive to mold development.
Q: Are magnesium oxide boards safe for indoor air quality?
A: Yes, magnesium oxide boards are considered very safe for indoor air quality. They are free from harmful substances such as asbestos, formaldehyde, crystalline silica, and other volatile organic compounds (VOCs). Their inorganic composition means they do not off-gas harmful chemicals, contributing to a healthier indoor environment. This makes them an excellent choice for individuals with allergies or sensitivities to common building material emissions.
Q: How long do magnesium oxide boards last?
A: Magnesium oxide boards are exceptionally durable and designed for a very long service life. Due to their inorganic composition, they are resistant to rot, decay, insect infestation, and biological degradation that can affect traditional wood-based materials. Their stability against moisture and fire also contributes to their longevity. When properly installed and maintained, MGO boards can last for the lifetime of the building, often exceeding 50 years, making them a highly resilient and sustainable building solution.
Q: Can you recycle magnesium oxide boards?
A: Yes, magnesium oxide boards are theoretically recyclable. As an inorganic, mineral-based product, they can be crushed and repurposed. The crushed material can be used as an aggregate in new construction products, as a soil amendment (due to its magnesium content benefiting agriculture), or as backfill. However, the practical availability of dedicated MGO board recycling facilities can vary by region. In areas where specialized recycling is not yet established, the material is typically disposed of as inert construction and demolition waste. The long lifespan of MGO boards, however, already significantly reduces the overall waste stream compared to less durable materials.