Selecting the ideal modular house wall panel is a decisive step in any construction initiative. These innovative components present an intelligent approach to building resilient and highly functional structures. Whether destined for residential dwellings or commercial developments, the right panel choice wields substantial influence. Assess critical factors such as durability, budget alignment, and thermal efficiency. Every project carries its own blueprint of demands—thus, the panel must correspond precisely to those specifications. For example, integrating the proper modular wall panel into your home can substantially improve insulation while minimizing utility expenditures.
Key Insights
Choosing the optimal modular wall panel is essential. Evaluate core criteria—structural integrity, affordability, and energy conservation—to align with your objectives.
Modular panels are time- and cost-efficient. Their streamlined installation reduces labor hours, trims down waste, and accelerates project timelines, making them a smart investment.
Not all panels are built alike. Fire-rated panels elevate safety standards, while acoustic panels are engineered to foster tranquility in bustling office environments.
These panels excel in thermal regulation. They retain interior temperatures, decreasing reliance on artificial heating and cooling—leading to long-term cost reduction.
Sustainability matters. A growing number of modular panels are fabricated from eco-conscious materials and are recyclable, contributing to reduced environmental impact and a more responsible construction footprint.
Understanding Modular Wall Panels
Definition and Purpose
Modular wall panels are prefabricated elements meticulously engineered for rapid wall assembly. Employed across residential, commercial, and institutional spaces, these panels serve both structural and decorative purposes. Manufactured in controlled environments, they uphold rigorous quality standards and dimensional precision. Each panel is purpose-built—be it for thermal retention, fire suppression, or acoustic isolation.
Beyond aesthetics, these panels reinforce structural stability, enhance energy efficiency, and accelerate the construction timeline. Decorative variants elevate interior ambiance, while load-bearing types are essential for supporting substantial architectural demands. Below is a reference table outlining panel categories and their respective functionalities:
Panel Categories
|
Purpose and Application
|
Aesthetic Enhancement Panels
|
Enhance interior aesthetics with striking feature walls that exude sophistication.
|
Load-Bearing Structural Panels
|
Fortify structural integrity—ideal for load-bearing installations demanding resilience.
|
Fire-Retardant Composite Panels
|
Safeguard against fire hazards, particularly suited for industrial and commercial environments.
|
Humidity-Resistant Barrier Panels
|
Combat moisture-related issues in high-humidity zones such as bathrooms and kitchens.
|
Thermal Insulation Core Panels
|
Optimize energy efficiency by maintaining thermal balance within the structure.
|
Sound-Dampening Acoustic Panels
|
Mitigate acoustic disturbances in offices and communal areas, fostering a focused atmosphere.
|
The Strategic Role of Modular Wall Panels in Contemporary Construction
Advantages of Modular Wall Panels
Modular wall panels present a suite of advantages for modern construction methodologies. They streamline labor expenditures by requiring minimal on-site intervention and can be installed rapidly, accelerating project timelines. Engineered within controlled factory settings, these panels ensure precision manufacturing, leading to minimal material waste and superior quality consistency. Additionally, their energy-efficient design contributes to significant reductions in heating and cooling costs. Specialized variants—such as acoustic panels—enhance interior comfort by reducing ambient noise and fostering a more serene environment.
The demand for modular panels is on a sharp upward trajectory. Valued at $10.5 billion in 2023, the market is projected to soar to $18.7 billion by 2032—a testament to the increasing preference for sustainable and energy-conscious building solutions.
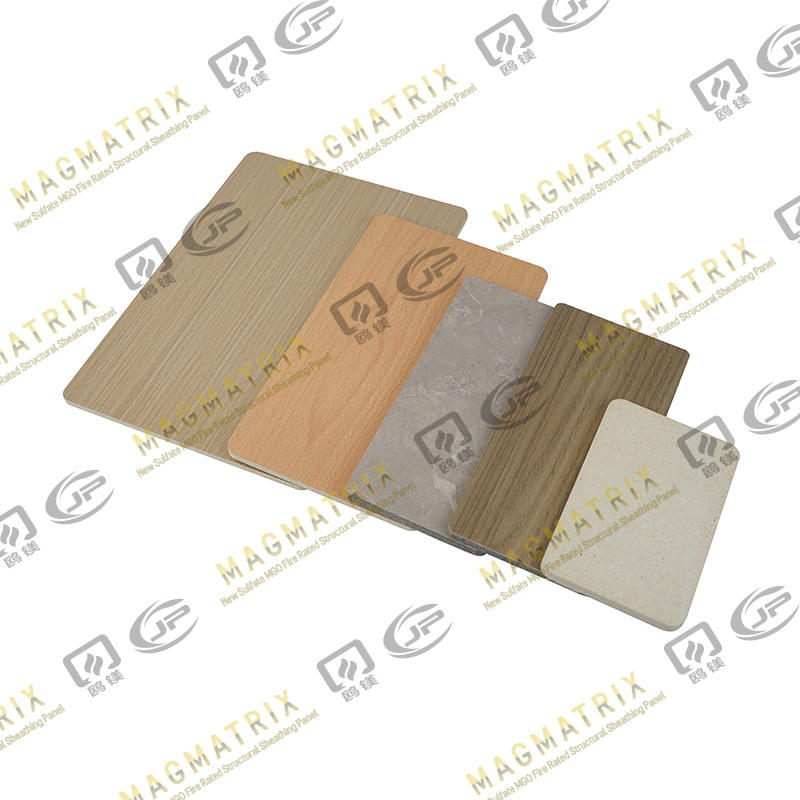
Why Modular Panels Are Gaining Ground
The rise in popularity of modular wall panels is anchored in their practical benefits and operational simplicity. Suitable across a spectrum of applications—from residential spaces to expansive commercial complexes—these panels integrate seamlessly with prefabricated structures, making them especially attractive for modular housing developments.
They also promote tidier construction environments by minimizing on-site debris and airborne particles. Lightweight yet durable, these panels are easy to handle and install, translating to reduced logistical overhead and lower construction costs.
Types of Modular Wall Panels
Precast Concrete Panels
Overview
Precast concrete panels are meticulously engineered off-site in controlled factory environments, enabling accelerated construction timelines. Mold-formed for precision, these panels boast uniform dimensions and exceptional structural integrity. Widely adopted in both residential and commercial developments, they serve dual purposes: enhancing both structural robustness and aesthetic appeal.
Distinctive Benefits
Rapid Deployment & Operational Efficiency
Precast panels expedite the building process. Fabricated away from the construction site, they eliminate delays caused by inclement weather or logistical bottlenecks.
Unwavering Quality Assurance
Manufactured under stringent standards, these panels consistently deliver high-caliber performance and reliability across all applications.
Design Versatility
Customizable to meet bespoke architectural visions, precast panels offer the creative latitude required for standout developments and tailored environments.
Eco-Conscious Construction
Engineered with sustainability in mind, these panels minimize onsite waste and optimize energy usage—translating into long-term cost efficiency and environmental stewardship.
Benefit
|
Description
|
Speed and Efficiency
|
Made off-site, they speed up building and avoid delays.
|
Quality and Consistency
|
Built to exact standards, ensuring they are strong and uniform.
|
Flexibility and Customization
|
Can be adjusted to fit creative designs and special needs.
|
Sustainability
|
Use less material and improve energy use, saving money.
|
Principal Drawbacks
The relocation and installation of precast panels frequently require specialized equipment. Additionally, their initial investment may surpass that of more conventional construction methods.
Structural Insulated Panels (SIPs)
Overview
Structural Insulated Panels, known as SIPs, are precision-engineered composite building elements featuring a rigid foam core sandwiched between durable outer layers. These panels are exceptionally robust and thermally efficient, making them an ideal choice for environmentally conscious construction. SIPs are utilized across walls, roofing systems, and flooring assemblies to optimize internal climate control.
Core Benefits
Superior Thermal Performance: SIPs deliver exceptional insulation, significantly reducing energy expenditure for heating and cooling.
Regulatory Adherence: Engineered to align with rigorous building codes, SIPs uphold industry standards for safety and craftsmanship.
Resilience and Longevity: Designed to withstand severe environmental stressors—including high winds and seismic activity—SIPs offer long-term structural reliability.
Evidence Type
|
Description
|
Compliance with Industry Standards
|
SIPs meet important safety and quality rules for building materials.
|
Rigorous Evaluations
|
SIPs pass tests to show they follow building codes and safety laws.
|
Natural Disaster Resilience
|
Tests prove SIPs can handle earthquakes and tough conditions in the U.S.
|
Key Disadvantages of SIPs
Structural Insulated Panels (SIPs) often come at a premium compared to conventional building materials. Their rigid composition demands meticulous handling during installation to prevent costly damage or structural compromise.
Metal Wall Panels
Overview
Metal wall panels offer a blend of robustness and efficiency, making them ideal for contemporary construction across commercial sectors. Common in office buildings and industrial facilities, these panels present a sleek aesthetic while providing long-lasting performance. Insulated Metal Panels (IMPs) merge structural support with thermal insulation, offering a smart solution that balances function and cost.
Key Advantages
Longevity: Engineered primarily from steel, metal panels exhibit exceptional resistance to environmental degradation, including harsh weather conditions.
Streamlined Installation: IMPs integrate multiple layers—sheathing, insulation, vapor barrier, and more—into a single unit, dramatically simplifying the construction process and minimizing material waste.
Eco-Conscious: Steel's recyclability positions metal panels as a sustainable alternative, supporting green construction practices and lifecycle efficiency.
A hospitality project utilized IMPs for swift assembly and cutting-edge architectural design. By consolidating six distinct wall layers into one, the build time was slashed and surplus materials nearly eliminated. Steel’s enduring strength and recyclability reinforce its status as a cornerstone of modern construction.
Key Disadvantages
Despite their strength, metal panels are susceptible to surface imperfections like dents or abrasions. In extreme climates, additional insulation may be necessary to maintain energy efficiency, slightly offsetting their integrated benefits.
Wood-Based Panels
Overview
Crafted from engineered timber products such as oriented strand board (OSB), plywood, or medium-density fiberboard (MDF), wood-based panels provide a sustainable and adaptable option for modular architecture. Lightweight and easy to manipulate, they serve both structural and aesthetic functions within prefabricated environments.
Commonplace in modular designs, these panels offer dimensional stability and ease of customization. Their use of renewable resources and capacity to reduce onsite waste amplify their environmental appeal.
Key Advantages
Sustainability: Wood panels contribute to low-waste construction. According to research by Colorado State University, modular methods utilizing these materials generate under five percent material waste.
Construction Efficiency: By accelerating the build cycle by 30–50%, these panels enhance project timelines, especially in prefab developments.
Material Adaptability: Suitable for load-bearing walls, partitions, or decorative elements, wood-based panels empower architects to innovate with form and function.
Cost Efficiency: Optimized material usage and minimized waste translate directly to reduced overall expenditures.
Key Disadvantages
Moisture poses a risk to the longevity of wood-based panels. Over time, water exposure can degrade their structural integrity. Furthermore, they offer less fire resistance compared to magnesium oxide panels, limiting their application in high-risk environments.
Glass Reinforced Panels (GRPs)
Overview
Glass Reinforced Panels (GRPs), composed of fiberglass mesh and polymer resin, deliver remarkable strength without the burden of weight. Widely adopted in modular builds, they serve high-performance roles in both industrial and cleanroom settings due to their durability and hygienic finish.
With a sleek, sterile appearance, GRPs suit modern interiors as well as function-driven spaces like hospitals, laboratories, and food processing areas. Their versatility also supports aesthetic applications in architectural design.
Key Advantages
Exceptional Durability: GRPs are impervious to corrosion, moisture, and many chemicals, ensuring longevity even under harsh conditions.
Lightweight Efficiency: Their reduced mass eases transportation and speeds up installation, lowering logistical costs.
Architectural Flexibility: GRPs can be molded into various configurations, enabling creative and unconventional forms.
Key Disadvantages
The upfront investment for GRPs exceeds that of standard alternatives. Moreover, the synthetic materials used in their production may not fully align with eco-certification requirements, potentially impacting sustainable design objectives.