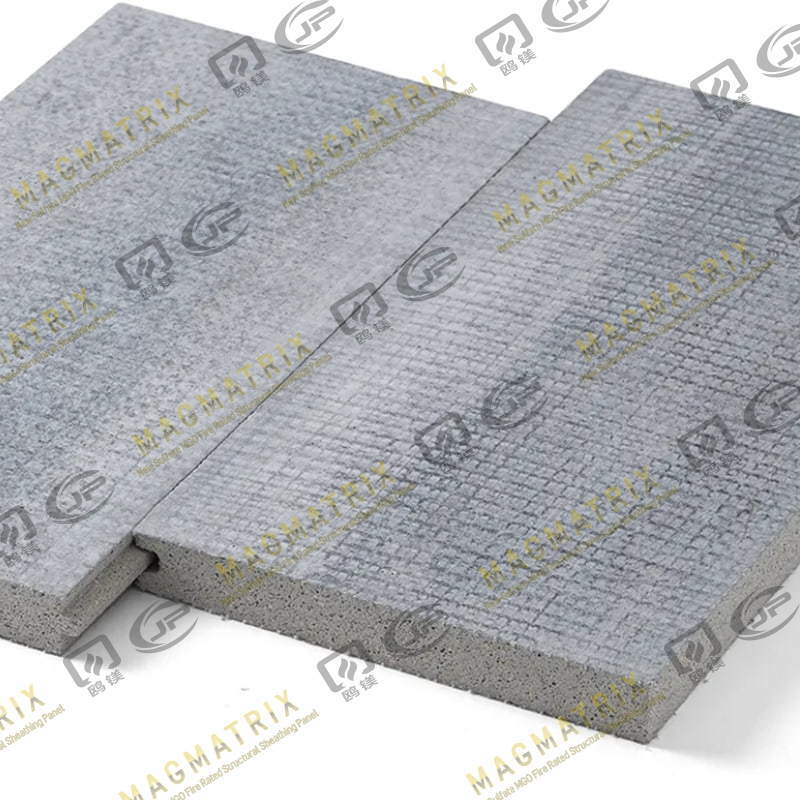
Introduction to MgO Subfloor Sheathing Board
Magnesium Oxide (MgO) subfloor sheathing board has emerged as a revolutionary product in the construction industry. Composed mainly of magnesium oxide, along with other materials such as magnesium sulfate, cellulose, and perlite, this board offers a wide range of benefits that make it an ideal choice for subfloor applications.
Key Characteristics of MgO Subfloor Sheathing Board
Fire Resistance
One of the most remarkable features of MgO subfloor sheathing board is its exceptional fire resistance. It has been tested and proven to meet high fire safety standards. For example, many MgO boards are classified as non - combustible, with some able to withstand high temperatures for extended periods. This property is crucial in preventing the spread of fire in a building, protecting lives and property.
Water and Moisture Resistance
MgO boards are highly resistant to water and moisture. They do not warp, swell, or delaminate when exposed to moisture for short periods. This makes them suitable for use in areas where there may be a risk of water exposure, such as basements or bathrooms. Unlike some traditional subfloor materials like plywood or oriented strand board (OSB), MgO boards maintain their structural integrity even in humid conditions.
Durability and Strength
MgO subfloor sheathing boards offer excellent durability and strength. They have high bending strength, which means they can support heavy loads without sagging or breaking. This makes them suitable for both residential and commercial applications. In addition, they are resistant to pests, mold, and mildew, ensuring a long - lasting subfloor solution.
Environmental Friendliness
MgO boards are considered environmentally friendly. They are often made from sustainable materials and have a low carbon footprint. Many manufacturers use recycled content in their production process. Moreover, MgO boards are recyclable at the end of their useful life, reducing waste in landfills.
Applications of MgO Subfloor Sheathing Board
Residential Buildings
In residential construction, MgO subfloor sheathing boards are commonly used in new home builds. They provide a solid and stable base for flooring materials such as hardwood, tile, or carpet. They are also suitable for use in renovations, where they can replace damaged or deteriorated subflooring. For example, in a bathroom renovation, the water - resistant properties of MgO boards make them an ideal choice for subflooring under tile.
Commercial Buildings
Commercial buildings also benefit from the use of MgO subfloor sheathing boards. In office buildings, retail stores, and restaurants, the durability and fire resistance of these boards are highly valued. They can support the heavy foot traffic and equipment found in commercial settings. In addition, their fire - resistant properties help meet building code requirements for fire safety in commercial structures.
Modular Buildings
Modular building construction has seen an increase in the use of MgO subfloor sheathing boards. These boards are easy to transport and install in modular units. Their lightweight nature, combined with their strength, makes them a convenient choice for modular building projects. They can be quickly assembled to create a subfloor structure that is ready for further finishing.
Comparison with Traditional Subfloor Materials
Subfloor Material |
Fire Resistance |
Water Resistance |
Durability |
Environmental Impact |
Cost |
MgO Board |
Excellent (non - combustible) |
High |
High, resistant to pests, mold, and mildew |
Environmentally friendly, low carbon footprint, recyclable |
Moderate to high, but long - term cost - effective |
Plywood |
Low to moderate, can catch fire easily |
Low, can warp and delaminate when wet |
Moderate, can be damaged by pests and moisture |
High carbon footprint, not easily recyclable |
Moderate |
OSB |
Low to moderate, can catch fire easily |
Low, highly susceptible to water damage |
Moderate, can be damaged by pests and moisture |
High carbon footprint, not easily recyclable |
Low to moderate |
Installation of MgO Subfloor Sheathing Board
Preparation
Before installing MgO subfloor sheathing board, the subfloor area must be clean, dry, and level. Any existing flooring materials should be removed, and the subfloor should be inspected for damage. If there are any soft spots or areas of rot, they should be repaired or replaced.
Cutting and Fitting
MgO boards can be cut using standard woodworking tools such as circular saws or jigsaws. When cutting, it is important to wear appropriate safety gear, including dust masks, as the cutting process can generate fine dust. The boards should be cut to the required size and shape to fit the subfloor area precisely.
Fastening
MgO subfloor sheathing boards are typically fastened to the subfloor joists using screws or nails. The fasteners should be spaced according to the manufacturer's recommendations to ensure proper attachment. In some cases, adhesive may also be used in addition to fasteners to provide extra stability.
Market Trends and Future Outlook
The demand for MgO subfloor sheathing boards is expected to grow in the coming years. As more consumers become aware of the benefits of these boards, especially in terms of fire safety, environmental friendliness, and durability, their use is likely to increase in both residential and commercial construction. In addition, ongoing research and development may lead to further improvements in the performance and cost - effectiveness of MgO boards, making them an even more attractive option for the construction industry.