Magnesium Oxide (MgO) board, often simply referred to as Mag Board, is a mineral-based, green building material that has been used in various forms for decades, though its widespread adoption in modern construction is a more recent phenomenon. It is an environmentally friendly product made primarily from magnesium oxide (MgO), a type of mineral cement, combined with other non-toxic ingredients like magnesium chloride, perlite, wood fiber, and a mesh of fiberglass. This unique blend results in a construction panel that boasts an impressive array of desirable properties, setting it apart from conventional building materials.
Unlike gypsum-based drywall or cement board, MgO board offers exceptional performance characteristics, including high resistance to fire, water, mold, and mildew. Its inherent strength and durability, coupled with its non-toxic composition and energy-efficient production process, make it an attractive alternative for a wide range of building applications. As the construction industry increasingly seeks sustainable and high-performing materials, MgO board is emerging as a leading solution, contributing to safer, healthier, and more resilient structures.
Composition of Magnesium Oxide Board
The exceptional characteristics of MgO board stem directly from its unique composition and the meticulous manufacturing process it undergoes. Understanding these foundational elements is key to appreciating the material's performance.
How Magnesium Oxide Board is Manufactured
The production of MgO board is a relatively energy-efficient process compared to some traditional building materials like cement. It typically involves a series of steps that combine raw materials into a sturdy, homogeneous panel:
Raw Material Preparation: The primary raw material, magnesium oxide powder, is obtained by heating magnesium carbonate (magnesite) to high temperatures, a process known as calcination. This highly reactive powder is then mixed with a magnesium chloride solution, which acts as a binding agent.
Mixing and Forming: To this base mixture, various fillers and reinforcing agents are added. These typically include perlite (a volcanic glass that enhances fire resistance and reduces weight), wood fibers (for flexibility and strength), and a fiberglass mesh (for tensile strength and dimensional stability). The ingredients are thoroughly mixed to create a consistent slurry.
Casting and Curing: The slurry is then cast into molds and allowed to cure at ambient temperatures. Unlike Portland cement, which requires significant heat for curing, MgO board cures through a chemical reaction between magnesium oxide and magnesium chloride, forming a crystalline structure that provides its strength and durability. This curing process can take several hours to a few days, depending on the specific formulation and desired properties.
Finishing: Once cured, the boards are typically cut to standard sizes, edges are trimmed, and surfaces may be sanded to achieve a smooth finish. Some boards may also undergo a final drying process to ensure optimal moisture content before packaging and distribution.
Key Features of MgO Board
The carefully controlled composition and manufacturing process endow MgO board with a distinct set of features that make it a standout material in construction.
Feature |
Description |
Fire Resistance |
Incombustible and can withstand extremely high temperatures (up to 1,000°C / 1,832°F) without burning, melting, or emitting toxic smoke. Often rated A1 non-combustible. |
Water Resistance |
Highly resistant to water absorption and moisture. It does not swell, warp, or delaminate when exposed to water, making it ideal for wet areas. |
Mold & Mildew Proof |
Due to its mineral composition and resistance to moisture, MgO board does not provide a food source for mold, mildew, or fungi growth, contributing to healthier indoor air quality. |
High Strength & Durability |
Offers excellent compressive and flexural strength, making it very durable and resistant to impact damage. It is also dimensionally stable, resisting expansion and contraction with temperature changes. |
Lightweight |
Despite its strength, MgO board is often lighter than equivalent cement board, simplifying handling and reducing structural load. |
Eco-Friendly |
Made from natural minerals, free from asbestos, formaldehyde, and other harmful chemicals. Its production process is less energy-intensive than some alternatives, and it is recyclable. |
Sound Insulation |
Its density and composition contribute to good sound attenuation properties, helping to reduce noise transmission between rooms. |
Pest Resistance |
As an inorganic material, it is not susceptible to damage from termites, rodents, or other pests that can affect wood-based products. |
Workability |
Can be easily cut, drilled, and fastened with standard tools, similar to working with wood or drywall. It holds screws well and can be finished with paints, plasters, or tiles. |
Applications of MgO Board
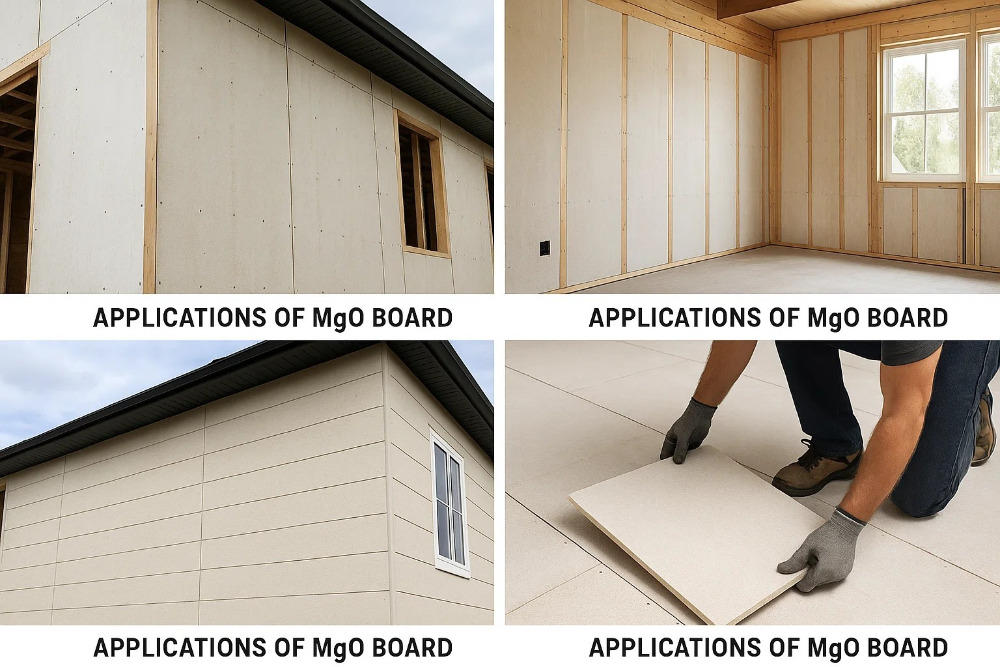
The diverse and superior properties of MgO board make it an incredibly versatile material suitable for a wide array of construction applications, both interior and exterior. Its resistance to fire, water, and mold, combined with its strength and environmental benefits, allows it to be used in places where traditional materials might fall short or require additional treatments.
Walls and Partitions
One of the most common applications for MgO board is in the construction of interior and exterior walls and partitions.
Interior Walls: In residential and commercial buildings, MgO board is an excellent alternative to gypsum drywall, particularly in areas requiring enhanced performance. Its high fire rating makes it ideal for fire-rated assemblies in corridors, stairwells, and commercial kitchens. In bathrooms, basements, and laundry rooms, its water and mold resistance provide a significant advantage over standard drywall, preventing issues like swelling, deterioration, and the growth of unhealthy organisms.
Exterior Walls (Sheathing): When used as exterior sheathing, MgO board provides a robust, weather-resistant, and fire-resistant layer beneath the final cladding. It contributes to the structural integrity of the building and offers an additional barrier against moisture penetration and fire spread.
Acoustic Walls: Due to its density, MgO board can contribute to improved sound insulation, making it a suitable choice for walls in spaces where noise reduction is critical, such as theaters, studios, or multi-family dwellings.
Ceilings
MgO board is also highly effective for ceiling applications, offering similar benefits as seen in wall installations.
Fire-Rated Ceilings: Its non-combustible nature is a primary benefit for ceilings, especially in commercial buildings, public spaces, and multi-story residential units where fire safety regulations are stringent. It can contribute to achieving specific fire-resistance ratings for ceiling assemblies.
Moisture-Prone Areas: In bathrooms, kitchens, swimming pool enclosures, or any other area subject to high humidity or potential moisture exposure, MgO ceilings help prevent sagging, mold growth, and material degradation that can plague traditional ceiling tiles or drywall.
Smooth Finish: MgO board provides a smooth, stable surface that is ready for painting, texturing, or other decorative finishes, allowing for aesthetically pleasing and durable ceiling designs.
Flooring/Subfloor
While less common than wall or ceiling applications, MgO board is increasingly being considered for flooring and subfloor systems due to its unique properties.
Subfloor: When used as a subfloor, it offers a stable, flat, and durable base for various finished flooring materials. Its resistance to moisture prevents warping or swelling, which can be an issue with wood-based subfloors in certain environments. Its fire resistance also adds a layer of safety beneath the main floor.
Tile Backer Board: Similar to cement board, MgO board serves as an excellent backer board for tile installations in bathrooms, kitchens, and other wet areas. Its inherent water and mold resistance ensure the longevity of the tiled surface by preventing moisture from compromising the substrate.
Radiant Floor Heating Systems: Its thermal stability and fire resistance make it a suitable material for encasing or supporting radiant floor heating elements.
Sheathing
As touched upon briefly in walls, MgO board excels as a general sheathing material for both interior and exterior structural applications.
Exterior Wall Sheathing: This is a critical application where MgO board provides structural rigidity, acts as a barrier against air and moisture infiltration, and significantly enhances the fire rating of the entire building envelope. Its dimensional stability means less expansion and contraction, which can lead to a more stable and energy-efficient building.
Interior Structural Sheathing: In some specialized construction, MgO board can be used as interior structural sheathing, providing bracing and an additional layer of fire protection and sound dampening.
Benefits of MgO Board
The growing popularity of MgO board in modern construction is largely attributable to its extensive list of benefits, which address many of the challenges associated with traditional building materials. These advantages not only contribute to safer and more durable structures but also align with increasing demands for sustainable and healthy building practices.
Fire Resistance
One of the most compelling benefits of MgO board is its exceptional fire resistance. Unlike wood or gypsum, which can burn or degrade under high heat, MgO board is inherently non-combustible.
Non-Combustible: MgO board does not ignite, burn, or contribute fuel to a fire. It typically achieves an A1 non-combustible rating, the highest possible fire rating for building materials, as per international standards.
High Temperature Withstand: It can withstand temperatures up to 1,000°C (1,832°F) for extended periods without melting, deforming, or emitting smoke or toxic fumes. This characteristic is crucial for compartmentalizing fires and allowing occupants more time to evacuate safely.
Reduced Smoke and Toxins: In the event of a fire, MgO board produces virtually no smoke and releases no toxic gases, which are often a greater threat than the flames themselves in building fires. This significantly enhances life safety.
Waterproofing and Mold Resistance
Moisture and mold are persistent enemies of many building materials. MgO board offers robust protection against both.
High Water Resistance: Unlike gypsum board, which can swell, soften, and disintegrate when exposed to water, MgO board is highly resistant to water absorption. It maintains its structural integrity even in damp or wet conditions, making it ideal for bathrooms, kitchens, basements, and exterior applications.
No Capillary Action: Its unique composition means it does not wick water through capillary action, further preventing moisture from spreading within the board.
Mold, Mildew, and Fungi Proof: Because it is a mineral-based product and does not provide a food source for organic growth, MgO board naturally resists the proliferation of mold, mildew, bacteria, and fungi. This is a significant advantage for maintaining healthy indoor air quality and preventing structural damage in humid environments.
Durability and Strength
MgO board is known for its impressive strength-to-weight ratio and long-lasting performance.
High Impact Resistance: Its dense and crystalline structure provides excellent impact resistance, making it less prone to dents and punctures than standard drywall. This is particularly beneficial in high-traffic areas.
Flexural and Compressive Strength: It possesses good flexural strength, allowing it to bend slightly without breaking, and high compressive strength, meaning it can withstand significant loads.
Dimensional Stability: MgO board exhibits excellent dimensional stability, meaning it resists expansion and contraction due to changes in temperature or humidity. This minimizes cracking and warping, leading to a more stable and aesthetically pleasing finish over time.
Pest Resistance: As an inorganic material, it is impervious to pests such as termites, rodents, and other insects that can damage wood-based building materials.
Environmental Benefits
Beyond its performance characteristics, MgO board also shines in its environmental profile, aligning with green building initiatives.
Eco-Friendly Composition: It is primarily made from naturally occurring minerals, including magnesium oxide, magnesium chloride, perlite, and wood fiber. It is free from asbestos, formaldehyde, silica, and other harmful chemicals commonly found in some traditional building materials.
Low Energy Production: The manufacturing process for MgO board is relatively energy-efficient, requiring less energy input compared to the production of Portland cement or gypsum.
Recyclability: While not yet universally established, MgO board is theoretically recyclable, and efforts are ongoing to develop widespread recycling programs.
Contribution to Healthy Indoor Air Quality: Its mold resistance and lack of harmful off-gassing contribute to a healthier indoor environment for occupants.
Here's a summary table of the key benefits:
Benefit |
Description |
Superior Fire Resistance |
Non-combustible (A1 rating), withstands 1000°C without burning, melting, or toxic smoke, enhances life safety. |
Excellent Water Resistance |
Does not swell, warp, or delaminate when wet; maintains structural integrity in damp conditions; no capillary action. |
Inherent Mold & Mildew Proof |
Inorganic composition prevents growth of mold, mildew, fungi, and bacteria, promoting healthier indoor air. |
High Durability & Strength |
Impact-resistant, high flexural and compressive strength, dimensionally stable (resists expansion/contraction), pest-resistant (termites, rodents). |
Environmentally Friendly |
Made from natural minerals, free of harmful chemicals (asbestos, formaldehyde, silica), low-energy production, recyclable, contributes to healthy indoor air quality. |
Good Sound Insulation |
Helps reduce noise transmission between spaces due to its density. |
Versatile & Workable |
Easy to cut, drill, fasten; holds screws well; compatible with various finishes (paint, plaster, tile); suitable for diverse applications. |
Disadvantages of MgO Board
While MgO board offers numerous advantages, it's also important to acknowledge its potential drawbacks. These typically relate to cost, availability, and specific installation considerations, though many of these concerns are diminishing as the material becomes more widespread and manufacturing processes improve.
Cost Considerations
One of the most frequently cited disadvantages of MgO board is its upfront cost.
Higher Material Cost: Generally, MgO board has a higher material cost per square foot compared to traditional gypsum drywall. While prices vary by manufacturer, thickness, and region, it's often comparable to or slightly more expensive than cement board. This initial investment can be a deterrent for budget-constrained projects.
Long-Term Value vs. Upfront Cost: It's important to consider the long-term value. The enhanced durability, fire resistance, and moisture/mold resistance of MgO board can lead to significant savings over the lifespan of a building by reducing maintenance, repair, and replacement costs, and potentially even insurance premiums. However, this long-term value might not be immediately apparent in the initial budget.
Availability and Supply
Despite its growing popularity, MgO board might not be as readily available as more conventional building materials in all regions.
Regional Availability: While national distributors are increasing, finding MgO board at every local hardware store might still be a challenge, particularly in less populated areas. This can sometimes lead to longer lead times for orders and potentially higher shipping costs.
Import Dependency: A significant portion of MgO board is manufactured overseas, particularly in China, where vast natural deposits of magnesium oxide are found. This can lead to reliance on imports, which might impact supply chain stability, lead times, and potentially contribute to a larger carbon footprint due to transportation. However, some manufacturers in the US and other regions are emerging, aiming to reduce this dependency.
Quality Consistency: Due to varied manufacturing processes globally, there can be inconsistencies in the quality of MgO board from different suppliers. This was highlighted in some past issues (e.g., in Denmark around 2015) where certain formulations, particularly those using magnesium chloride (MgCl2) as a binder, experienced issues with excessive moisture absorption and corrosion of metal fasteners, leading to restrictions or recalls in some regions. Reputable manufacturers have largely addressed these issues with improved formulations (e.g., using magnesium sulfate (MgSO4) which is not hygroscopic) and stricter quality control, but it's crucial for buyers to source from trusted suppliers.
Installation Challenges
While MgO board is generally workable, certain aspects of its installation can present challenges, especially for those unfamiliar with the material.
Tooling: While it can be cut with standard tools, using carbide-tipped blades or specialized diamond-tipped blades is often recommended for cleaner cuts and to extend tool life, as MgO board is denser than drywall. This might require an initial investment in new tools for some contractors.
Dust Generation: Cutting and sanding MgO board can produce fine dust. Although the material is free of asbestos and formaldehyde, it is still recommended to wear appropriate respiratory protection (e.g., a silica/concrete dust respirator) to avoid inhaling dust particles.
Fasteners: While MgO board holds screws well, its density means that standard nails might not hold as securely as in wood-based materials. Using screws, self-countersinking screws, wall plugs, or anchors is often preferred, especially for hanging heavy items like cabinets or shelves.
Expansion Gaps and Sealing: Like many rigid building materials, MgO board can experience minor hydrothermal movement (expansion/contraction) with significant changes in temperature and humidity. Proper installation requires leaving small expansion gaps between boards and at junctions with other structures, and then sealing these gaps with appropriate non-shrink caulk or sealants, particularly in exterior or high-moisture applications. This is a critical step to prevent potential cracking or moisture infiltration, and it requires careful attention to manufacturer guidelines.
Alkaline Surface for Finishing: The surface of MgO board is alkaline, which requires the use of a primer specifically formulated for concrete or masonry before applying paint or other finishes to ensure proper adhesion and prevent chemical reactions.
Here's a table summarizing the main disadvantages:
Disadvantage |
Description |
Higher Initial Cost |
Generally more expensive per square foot than gypsum drywall, requiring a larger upfront investment, though often offset by long-term savings. |
Availability & Supply |
May have limited local availability compared to traditional materials, potentially leading to longer lead times or higher shipping costs; significant import dependency can affect supply chain stability and contribute to higher embodied energy. |
Quality Variability |
Past issues with some formulations (MgCl2-based) led to moisture absorption and corrosion of fasteners in humid climates; emphasizes the need to source from reputable manufacturers using improved (e.g., MgSO4-based) formulations and strict quality control. |
Installation Specifics |
Requires specific tools (e.g., carbide-tipped blades) for optimal cutting; generates fine dust requiring respiratory protection; may require screws/anchors over nails for secure fastening; necessitates proper expansion gaps and sealing, and an alkaline-compatible primer for finishing. |
Brittleness (Less Flexible) |
While strong, its rigidity can make it more prone to cracking or breaking if improperly handled or installed, especially if dropped or flexed beyond its limits during transport or installation. |
Comparison with Other Construction Materials
To truly appreciate the value and appropriate applications of MgO board, it's essential to compare its properties with those of more traditional and widely used construction materials. This section highlights the key differences and advantages or disadvantages when pitted against drywall, cement board, and plywood.
MgO Board vs. Drywall (Gypsum Board)
Drywall (gypsum board) is the most common interior wall and ceiling material. While cost-effective and easy to install, it has significant limitations where moisture and fire are concerns.
Feature |
MgO Board |
Drywall (Gypsum Board) |
Composition |
Magnesium oxide, magnesium chloride/sulfate, perlite, wood fiber, fiberglass. |
Gypsum plaster core sandwiched between layers of paper or fiberglass mat. |
Fire Resistance |
Excellent (A1 non-combustible); does not burn, melt, or emit toxic smoke. |
Good (fire-rated types exist); contains water that turns to steam, resisting fire for a period, but eventually breaks down and crumbles. Releases smoke. |
Water & Mold Resistance |
Excellent; highly resistant to water absorption, does not swell, warp, or support mold growth. |
Poor (standard drywall); swells, softens, and disintegrates when wet; highly susceptible to mold growth. Moisture-resistant (greenboard) and fiberglass-faced options offer some improvement but are not truly waterproof. |
Strength & Durability |
High; impact-resistant, less prone to dents/punctures, dimensionally stable. |
Moderate; easily dented/punctured, can crack with building movement, susceptible to damage from moisture. |
Environmental Impact |
Eco-friendly, natural minerals, low energy production, no asbestos/formaldehyde. |
Mined gypsum can have environmental impacts; manufacturing process is energy-intensive; dust can be an irritant; some types contain VOCs. |
Cost |
Higher initial material cost. |
Lower initial material cost. |
Workability |
Easy to cut/fasten, requires specific blades/primers. |
Very easy to cut, score, and snap; readily available standard tools; finishes easily with joint compound. |
Applications |
Walls, ceilings, sheathing (interior/exterior), subfloors, wet areas. |
Primarily interior walls and ceilings in dry areas; specialized types for some moisture resistance (e.g., bathrooms, but not truly wet areas like shower enclosures). |
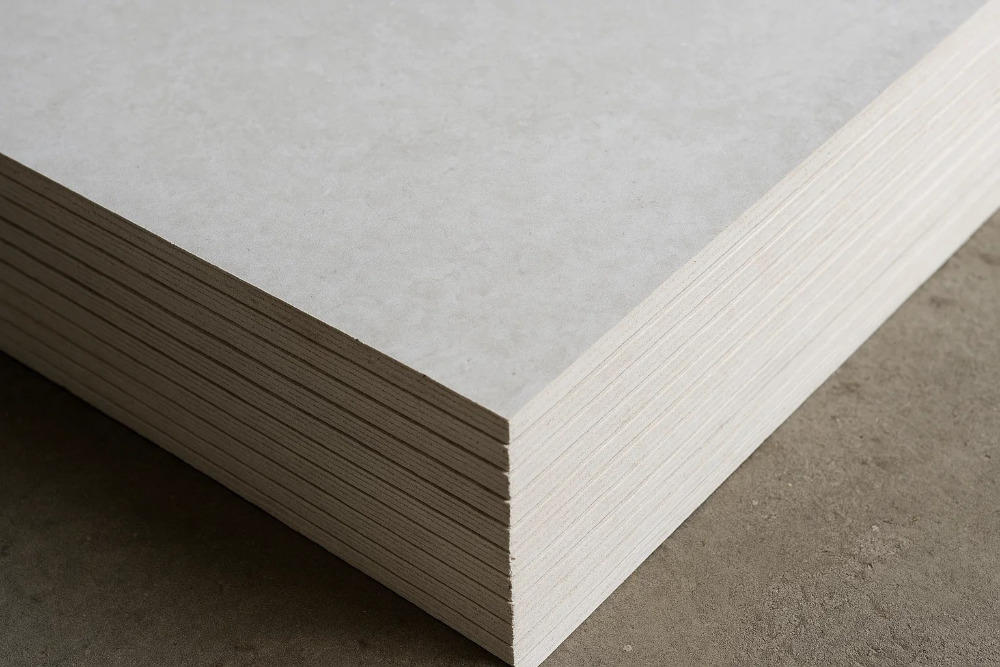
MgO Board vs. Cement Board
Cement board is a popular choice for wet areas like bathrooms and kitchens due to its water resistance. It's often used as a tile backer board.
Feature |
MgO Board |
Cement Board |
Composition |
Magnesium oxide, magnesium chloride/sulfate, perlite, wood fiber, fiberglass. |
Portland cement, sand, water, and often fiberglass mesh or cellulose fibers. |
Fire Resistance |
Excellent (A1 non-combustible); does not burn or emit smoke. |
Excellent (non-combustible); does not burn. |
Water & Mold Resistance |
Excellent; highly resistant to water absorption and mold growth. |
Excellent; highly water-resistant, does not rot or swell. Generally does not support mold growth. |
Strength & Durability |
High; good flexural strength, impact-resistant, dimensionally stable. |
Very High; extremely rigid and strong, very durable. Can be brittle if not fully supported during installation. |
Weight |
Lighter than cement board of comparable thickness. |
Heavier than MgO board, which can make handling and installation more challenging. |
Workability |
Easier to cut (score and snap or saw), less dusty than cement board. |
Harder to cut (requires specialized tools like scoring knives or carbide-tipped saws), generates significant silica dust requiring proper PPE. |
Fasteners |
Holds screws well. |
Requires specialized corrosion-resistant screws designed for cement board. |
Environmental Impact |
Eco-friendly, natural minerals, lower embodied energy. |
Manufacturing Portland cement is energy-intensive and produces significant CO2. Contains silica (dust is a health hazard). |
Applications |
Walls, ceilings, sheathing, subfloors, tile backer. |
Primarily tile backer board in wet areas (showers, floors), exterior applications as a substrate for stucco or siding where extreme rigidity and moisture resistance are paramount. Rarely used for general walls/ceilings due to weight and finishing. |
MgO Board vs. Plywood
Plywood is a widely used wood-based panel product, primarily for structural sheathing, subflooring, and general construction.
Feature |
MgO Board |
Plywood (Oriented Strand Board - OSB) |
Composition |
Magnesium oxide, magnesium chloride/sulfate, perlite, wood fiber, fiberglass. |
Layers of wood veneers (plywood) or strands (OSB) bonded with adhesive resins (e.g., urea-formaldehyde, phenolic resins). |
Fire Resistance |
Excellent (A1 non-combustible); does not burn or contribute fuel. |
Poor (combustible); burns readily, contributes fuel to fire, often requires additional fire-retardant treatments or layers for fire-rated assemblies. |
Water & Mold Resistance |
Excellent; highly resistant to water and mold. |
Poor to Moderate (depending on type); susceptible to swelling, warping, and delamination when wet. Can support mold growth. Exterior grade (e.g., marine ply) offers better resistance but is not truly waterproof. OSB is particularly sensitive to moisture. |
Strength & Durability |
High; dimensionally stable, resistant to impact. |
High (structural); good racking strength for shear walls. Can warp/delaminate with moisture. Susceptible to rot and insect damage. |
Pest Resistance |
Excellent; inorganic, not a food source for termites or rodents. |
Poor; highly susceptible to termite and other insect damage, as well as rot and fungal decay in damp conditions. |
Environmental Impact |
Eco-friendly, natural minerals, low energy production, no asbestos/formaldehyde. |
Uses wood (renewable resource, but often from old growth); adhesive resins can off-gas VOCs (especially formaldehyde in some types); manufacturing can be energy-intensive. |
Cost |
Higher initial material cost. |
Lower initial material cost. |
Applications |
Walls, ceilings, sheathing, subfloors, tile backer, wet areas. |
Structural sheathing for walls, roofs, and floors; general construction, furniture. |
Installation and Maintenance of MgO Board
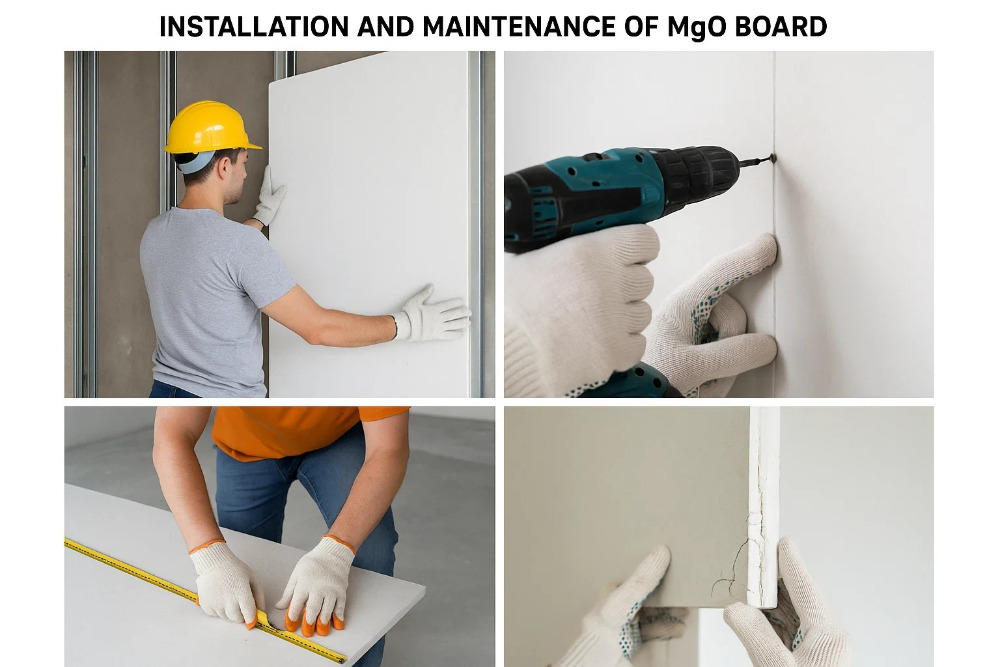
Installing MgO board properly is crucial for achieving a durable and high-performing finish. While it shares some similarities with other panel materials, its unique properties require specific considerations. Similarly, a little ongoing care will help ensure your MgO board lasts for decades.
Installation Process
Careful preparation and attention to detail are key to a successful MgO board installation. Follow these steps to ensure a smooth and lasting result:
Acclimatization and Storage: Before you begin, store MgO boards flat in a dry, well-ventilated area for at least 48 to 72 hours. This helps them adjust to the room's temperature and humidity, minimizing potential movement after installation.
Cutting the Boards: Measure your area carefully and mark the boards for precise cuts. You can score and snap thinner boards with a heavy-duty utility knife, but for cleaner cuts and to preserve tool life, a circular saw with a carbide-tipped or diamond-tipped blade is recommended. Always wear appropriate personal protective equipment (PPE), including eye protection and a dust mask or respirator, as cutting generates fine dust.
Positioning and Fastening: Position the boards on your prepared surface. It's crucial to leave small expansion gaps (typically 1/16" to 1/8" for interior applications, or as per manufacturer guidelines) between boards and around the perimeter where they meet walls or other structural elements. This allows for any minor movement. Fasten the boards using corrosion-resistant screws (like stainless steel or specially coated screws), spacing them approximately 6 to 8 inches along the edges and 12 inches in the field of the board. Ensure fasteners are flush with or slightly countersunk below the surface.
Joint Treatment: For a seamless appearance, apply fiberglass mesh tape over all seams. Then, use a flexible, high-quality joint compound or a specialized seam filler designed for MgO or cement board. Feather the compound smoothly over the taped joints. Once dry, lightly sand the surface. For wet areas or exterior applications, a waterproofing membrane or sealant should be applied over the joints and often the entire surface before the final finish.
Priming and Finishing: Because MgO board has an alkaline surface, you must apply a primer specifically formulated for concrete or masonry before painting or applying other finishes. This ensures proper adhesion and prevents any chemical reactions. Once primed and dry, you can paint, plaster, or tile over the MgO board. If tiling, use a thin-set mortar suitable for cement board.
Tip: Always wear protective gear, such as gloves, eye protection, and a respirator, when cutting or handling MgO boards to ensure safety during installation.
Maintenance Tips
MgO board is designed for low maintenance, but a few simple practices will help maintain its durability and appearance over time.
Regular Cleaning: For interior surfaces, simply wipe the board down with a damp cloth to remove dust and dirt. Avoid harsh abrasive cleaners that could damage the finish. For exterior applications, gentle power washing (at a safe distance and pressure) or manual cleaning can be effective.
Inspecting and Repairing: Periodically check for any signs of wear, such as cracks, chips, or loose fasteners. Address minor damage promptly using appropriate patching compounds. For larger issues, sections of the board can be cut out and replaced following installation guidelines. Also, inspect sealants around joints and penetrations, reapplying them if you notice any degradation to prevent moisture intrusion.
Repainting or Sealing: If your MgO board is exposed to harsh weather, heavy use, or if the original finish shows signs of wear, consider reapplying a sealant or paint. This helps maintain the protective layer and aesthetic appeal.
Note: While MgO board is highly water-resistant, it's best to avoid prolonged exposure to standing water, especially in unsealed or improperly installed areas, as this could potentially affect its long-term performance. Ensure proper drainage and ventilation in all applications.
Cost and Cost-Effectiveness of MgO Board
When evaluating any building material, cost is a critical factor. For MgO board, it's important to look beyond the initial purchase price and consider its long-term value and overall cost-effectiveness.
Price Range
The material cost of MgO board typically falls within a higher range compared to standard gypsum drywall. While prices fluctuate based on global market conditions, regional availability, manufacturer, thickness, and volume purchased, a general estimation would place MgO board in a similar or slightly higher price bracket than cement board, but consistently above basic drywall. For instance, while a standard 1/2-inch gypsum drywall sheet might cost in the range of $10-$20, a comparable size and thickness of MgO board could range from $25-$50 or more.
Factors influencing the price include:
Thickness and Density: Thicker and denser boards, offering enhanced strength and fire ratings, will naturally cost more.
Manufacturer and Formulation: Different manufacturers may use varying formulations (e.g., magnesium chloride vs. magnesium sulfate binders) and production methods, which can impact cost and quality. Boards with superior fire ratings or specific certifications might command a premium.
Origin and Shipping: As much of the MgO board is imported, international shipping costs, tariffs, and fluctuating exchange rates can significantly affect the final price.
Volume: Bulk purchases for large commercial projects often receive better pricing per unit than smaller retail orders.
Long-Term Value
Despite its potentially higher upfront material cost, MgO board offers significant long-term value that can lead to overall cost savings throughout the lifecycle of a building.
Reduced Repair and Replacement Costs: Its superior durability, water resistance, and mold resistance significantly reduce the likelihood of costly repairs or premature replacement due to water damage, mold growth, or impact damage. Unlike drywall, which might need replacing after a flood or significant leak, MgO board often remains intact, saving demolition, material, and labor costs.
Enhanced Fire Safety, Potentially Lower Insurance Premiums: The exceptional fire resistance of MgO board contributes to a safer building environment. In some cases, building with materials that have higher fire ratings can lead to lower insurance premiums for property owners, though this varies by insurer and policy.
Improved Indoor Air Quality and Health: By resisting mold and not off-gassing harmful chemicals, MgO board contributes to a healthier indoor environment. While difficult to quantify monetarily, the avoidance of health issues related to mold exposure can lead to fewer medical expenses and a more productive living/working space.
Energy Efficiency Contributions: While MgO board itself is not an insulator, its dimensional stability and contribution to a tighter building envelope (when properly installed) can support overall energy efficiency by reducing air leakage and helping to maintain consistent indoor temperatures.
Faster Construction and Less Waste (Potentially): While initial installation requires specific attention, the material's workability and resistance to common construction site damage can sometimes lead to fewer damaged sheets and a more efficient build process, reducing waste and labor hours.