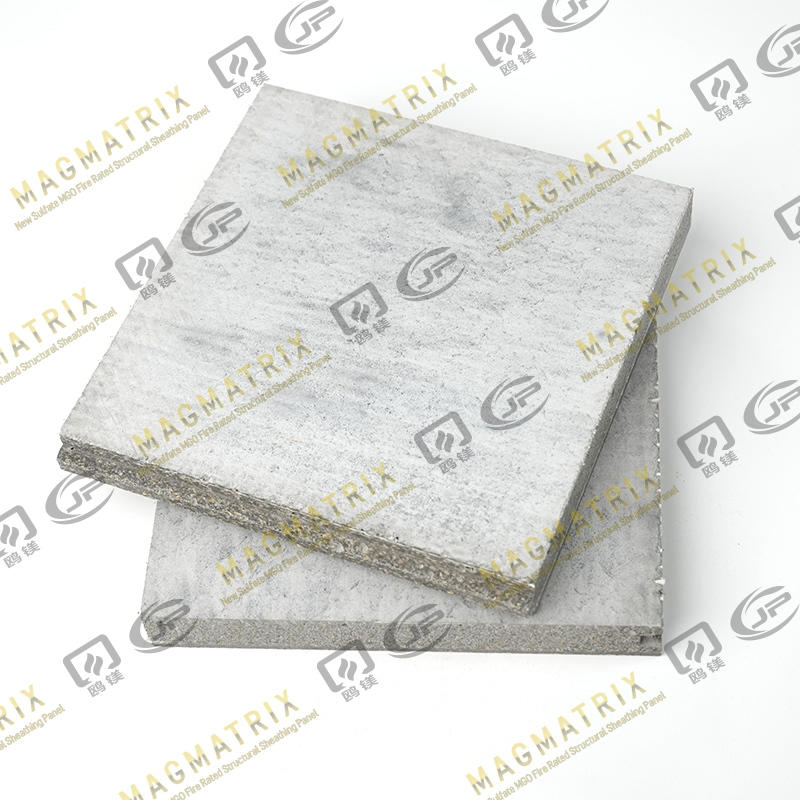
Key Takeaways
- Water Resistance is Paramount: Selecting a subfloor material with adequate water resistance is crucial for preventing mold growth, structural damage, and costly repairs in modern homes, especially in areas prone to moisture.
- Diverse Material Options: A range of materials offers varying degrees of water resistance, from highly impermeable options like magnesium oxide panels and cement board to enhanced wood-based products like engineered wood panels, premium OSB, and waterproofed plywood.
- Beyond “Waterproof”: Understand the distinction between “water-resistant” and truly “waterproof” materials. While some materials can withstand incidental moisture, truly waterproof options are designed for constant exposure without degradation.
- Installation Matters: Even the most water-resistant subfloor can fail without proper installation, including sealing seams, using appropriate fasteners, and ensuring adequate ventilation.
- Consider the Whole System: The performance of your subfloor is influenced by the entire flooring system, including underlayment, adhesive, and the finished floor material. Choose components that work cohesively to manage moisture.
Subfloor Basics
What Is a Subfloor?
At its core, a subfloor is the structural layer of flooring that lies directly beneath your finished floor covering (like hardwood, tile, carpet, or laminate). It’s typically fastened to the floor joists and serves several critical functions:
- Structural Support: The subfloor provides a rigid, stable platform that distributes loads from furniture, foot traffic, and the finished floor material across the floor joists.
- Foundation for Finished Flooring: It creates a smooth, flat, and secure surface for the installation of various flooring types, preventing sagging, squeaks, and unevenness.
- Moisture Barrier (Potentially): Depending on the material chosen, the subfloor can also act as an initial barrier against moisture intrusion from below or within the home.
- Sound Deadening: While not its primary function, some subfloor materials can contribute to reducing sound transmission between levels.
Common subfloor materials historically include plywood and oriented strand board (OSB), but modern construction increasingly explores alternatives with enhanced properties.
Why Water Resistance Matters
Water is a formidable enemy to building materials, and the subfloor is particularly vulnerable. Even seemingly minor water events can lead to significant problems:
- Mold and Mildew Growth: Moisture trapped within or beneath the subfloor creates an ideal environment for mold and mildew, leading to poor indoor air quality, unpleasant odors, and potential health issues for occupants.
- Structural Damage and Rot: Wood-based subfloors, if consistently exposed to moisture, can swell, delaminate, and eventually rot, compromising the structural integrity of your floor and even the entire house.
- Flooring Failure: Swelling or warping of the subfloor can cause finished flooring to buckle, crack, or lift, leading to costly repairs or complete replacement. This is especially true for moisture-sensitive flooring like hardwood or laminate.
- Pest Infestations: Damp, decaying wood can attract pests like termites and carpenter ants, which can further damage the structure.
- Reduced Home Value: Persistent moisture issues and resulting damage can significantly devalue a property and make it difficult to sell.
Water Resistant Subfloor Options
When choosing a water-resistant subfloor material, it’s important to understand the specific properties that contribute to its performance against moisture. Not all materials are created equal, and their suitability often depends on the application area and expected moisture exposure.
Key Comparison Factors
To effectively compare different subfloor options, we’ll focus on the following critical factors:
- Water Absorption/Resistance: This refers to how much moisture a material can absorb and how well it resists damage from water contact. Lower absorption generally means higher resistance.
- Dimensional Stability: How well does the material maintain its size and shape when exposed to changes in humidity or moisture? Materials with poor dimensional stability can swell, warp, or cup, leading to uneven floors.
- Durability and Strength: Beyond water resistance, the material must be strong enough to support live and dead loads and resist impacts and wear over time.
- Mold/Mildew Resistance: Some materials inherently resist mold and mildew growth due to their composition, while others may require treatments or careful moisture management.
- Installation Complexity: How easy or difficult is the material to cut, fasten, and install? This can impact labor costs and project timelines.
- Cost: The upfront material cost is a significant factor, though long-term benefits of water resistance can offset higher initial prices.
- Eco-Friendliness/Sustainability: For environmentally conscious homeowners, the material’s origin, manufacturing process, and recyclability are important considerations.
Moisture and Durability
The interplay between moisture and durability is perhaps the most crucial aspect of subfloor selection.
- Direct Water Exposure: In areas like bathrooms, laundry rooms, or basements where spills, leaks, or high humidity are common, a material with high water resistance is paramount. Materials like cement board or magnesium oxide panels are designed to withstand direct water contact without degrading.
- Vapor Permeability: Even without direct spills, moisture vapor can migrate through concrete slabs or from humid environments. Materials that can breathe or are designed to resist vapor transmission are important in these scenarios.
- Long-Term Performance: A subfloor’s ability to resist moisture over its lifespan directly impacts its long-term durability. Materials that swell or rot when wet will lose their structural integrity, leading to a compromised flooring system and potentially significant repair costs.
- Resistance to Delamination: For engineered or layered products (like plywood or OSB), water exposure can cause the layers to separate (delaminate), severely weakening the panel. Higher quality, water-resistant versions of these products use better adhesives and manufacturing processes to mitigate this risk.
- Impact on Fasteners: Constant expansion and contraction due to moisture fluctuations can loosen fasteners over time, leading to squeaky floors. Materials with better dimensional stability help maintain fastener integrity.
Comparison Table
To provide a quick and easy reference, the table below summarizes the key characteristics of various subfloor materials concerning their water resistance, durability, and other relevant factors. This table is designed to offer a general overview; specific product variations may have enhanced properties.
Feature |
Magnesium Oxide Panels |
Cement Board |
Engineered Wood Panels |
Premium OSB |
Waterproofed Plywood |
Standard Plywood |
OSB |
Primary Use |
All areas, esp. wet |
Wet areas, under tile |
General, some wet areas |
General, some wet areas |
General, some wet areas |
General Dry Areas |
General Dry Areas |
Water Resistance |
Excellent |
Excellent |
Good to Very Good |
Good |
Good |
Poor to Moderate |
Poor to Moderate |
Dimensional Stability |
Excellent |
Excellent |
Very Good |
Good |
Good |
Moderate |
Moderate |
Mold/Mildew Resistance |
Excellent |
Excellent |
Good to Very Good |
Good |
Good |
Poor |
Poor |
Weight |
Moderate to Heavy |
Heavy |
Moderate |
Moderate |
Moderate |
Moderate |
Moderate |
Ease of Cutting |
Moderate (requires scoring) |
Difficult (dusty, requires specialized tools) |
Easy |
Easy |
Easy |
Easy |
Easy |
Fastening |
Screws |
Screws |
Nails/Screws |
Nails/Screws |
Nails/Screws |
Nails/Screws |
Nails/Screws |
Cost (Relative) |
High |
Moderate to High |
Moderate to High |
Moderate |
Moderate |
Low |
Low |
Eco-Friendliness |
Good (mineral-based) |
Moderate |
Moderate (some recycled content) |
Moderate |
Moderate |
Moderate (renewable) |
Moderate (renewable) |
Typical Thickness (mm) |
12-18 |
6-12 (backer board), 12-16 (structural) |
18-23 |
18-23 |
18-23 |
18-23 |
18-23 |
Subfloor Application |
Yes (structural) |
Yes (structural, but often as underlayment) |
Yes |
Yes |
Yes |
Yes |
Yes |
Underlayment Req. |
No (unless for specific finishes) |
Yes (for tile, as a backer) |
No (unless for specific finishes) |
No (unless for specific finishes) |
No (unless for specific finishes) |
No (unless for specific finishes) |
No (unless for specific finishes) |
Material Profiles
Understanding the individual characteristics of each subfloor material is key to making an informed decision. Here, we delve deeper into what makes each option unique, particularly regarding its water resistance and overall performance.
Magnesium Oxide (MgO) Panels
Magnesium Oxide panels, often referred to as MgO board, are a relatively newer entrant to the subfloor market but are rapidly gaining popularity due to their exceptional properties. Composed primarily of magnesium oxide, magnesium chloride, and a reinforcing mesh (often fiberglass), these panels are mineral-based.
- Water Resistance: Outstanding. MgO panels are virtually impervious to water. They do not swell, delaminate, or rot when exposed to moisture, making them ideal for areas with high humidity, potential leaks, or even direct water exposure. They are also highly resistant to mold and mildew growth because they do not provide a food source for these organisms.
- Dimensional Stability: Excellent. MgO panels maintain their shape and size exceptionally well under varying temperature and humidity conditions, preventing warping or buckling of the finished floor.
- Durability and Strength: Very high. They offer excellent compressive and flexural strength, providing a robust and stable base for all types of flooring. They are also fire-resistant.
- Installation: Can be cut with a carbide-tipped saw blade (or scored and snapped for thinner panels). Fastening is typically done with screws. They are heavier than wood-based panels, which can make handling more challenging.
- Cost: Generally higher than traditional wood-based subfloors, but their long-term benefits in terms of durability and moisture protection can offset the initial investment.
- Eco-Friendliness: Considered a greener building material as magnesium oxide is abundant, and the manufacturing process often involves less energy than cement production. They are also naturally mold and insect resistant without added chemicals.
Cement Board
Cement board is a common choice, particularly as a backer board for tile installations in wet areas like bathrooms and kitchens. It’s made from cement, aggregates, and reinforcing fibers. While often used as an underlayment over a structural subfloor, thicker versions can serve as the primary subfloor in specific applications.
- Water Resistance: Excellent. Cement board itself does not degrade when exposed to water, nor does it promote mold growth. It’s inherently inorganic. However, it is porous, so a waterproofing membrane is typically required over it when used in showers or highly wet areas to prevent water from reaching the framing or adjacent materials.
- Dimensional Stability: Excellent. Like MgO, cement board is very stable and won’t swell, warp, or rot due to moisture.
- Durability and Strength: Very good. It provides a solid, rigid surface that is excellent for supporting tile and resisting cracking.
- Installation: Can be challenging to cut, often requiring scoring with a utility knife and snapping, or using a specialized saw blade, which can create significant dust. Fastening is done with specialized screws. It is also quite heavy.
- Cost: Moderate to high, comparable to or slightly less than MgO panels for structural thicknesses.
- Eco-Friendliness: Moderate. While cement production has an environmental footprint, cement board is durable and long-lasting.
Engineered Wood Panels
Engineered wood panels, specifically designed for subfloor applications, go beyond standard OSB or plywood. They are typically made from multiple layers of wood strands or veneers bonded with advanced moisture-resistant resins. Examples include specific brands like Huber’s AdvanTech or Georgia-Pacific’s DryPly.
- Water Resistance: Good to Very Good. These panels are engineered with enhanced moisture-resistant resins and often feature sealed edges or advanced manufacturing processes that significantly reduce water absorption and swelling compared to standard wood products. They are designed to withstand exposure to weather during construction and resist incidental moisture.
- Dimensional Stability: Very Good. Due to their engineered construction and advanced resins, they exhibit much better dimensional stability than standard plywood or OSB, reducing the likelihood of warping or cupping.
- Durability and Strength: Excellent. They are designed for high structural performance, often exceeding the strength requirements of standard subfloors, providing a squeak-free and solid base.
- Installation: Easy. Similar to standard plywood or OSB, they can be cut with standard woodworking tools and fastened with nails or screws.
- Cost: Moderate to High. They are more expensive than standard plywood or OSB but offer superior performance in terms of moisture resistance and durability.
- Eco-Friendliness: Moderate. They are wood-based, a renewable resource, but the manufacturing involves resins. Some products may contain recycled content.
Premium OSB (Oriented Strand Board)
Premium OSB represents an improvement over standard OSB, incorporating enhanced resins and sometimes a more refined manufacturing process to boost its moisture resistance. It still consists of wood strands arranged in layers and bonded with adhesive.
- Water Resistance: Good. While not waterproof, premium OSB is formulated to resist moisture better than standard OSB. It has reduced swelling characteristics when exposed to humidity and incidental wetting, making it a more reliable choice for general subfloor applications where minor moisture exposure might occur.
- Dimensional Stability: Good. Better than standard OSB, but still more susceptible to swelling and edge degradation than engineered wood panels or non-wood options.
- Durability and Strength: Good. Provides adequate structural support for typical residential loads.
- Installation: Easy. Cuts and fastens like standard OSB with common tools.
- Cost: Moderate. More expensive than standard OSB, but generally less than engineered wood panels or non-wood options.
- Eco-Friendliness: Moderate. Made from fast-growing, renewable timber, but involves resins.
Waterproofed Plywood
Waterproofed plywood is distinct from standard interior-grade plywood. It typically uses exterior-grade adhesives (like phenolic resins) that are highly resistant to moisture, often meeting “exterior” or “marine” grade specifications, though true marine-grade plywood is specialized and very expensive. For subfloor use, it generally refers to plywood made with durable, moisture-resistant glues.
- Water Resistance: Good. The key differentiator is the use of water-resistant adhesives that prevent delamination when wet. The wood plies themselves can still absorb moisture and swell, but the panel will largely retain its integrity. It’s suitable for areas with intermittent moisture exposure.
- Dimensional Stability: Good. Better than interior-grade plywood, but still prone to some swelling if exposed to prolonged moisture.
- Durability and Strength: Very Good. Provides a strong and stable subfloor.
- Installation: Easy. Cuts and fastens with standard woodworking tools.
- Cost: Moderate. More expensive than standard plywood but generally less than engineered wood panels.
- Eco-Friendliness: Moderate. Wood is renewable, but the manufacturing process involves glues and pressure.
Standard Plywood
Standard plywood, typically interior-grade “CDX” or similar, has historically been a common subfloor material. It’s made from thin wood veneers bonded together with adhesives.
- Water Resistance: Poor to Moderate. While it can withstand some incidental splashes, the interior-grade adhesives are not designed for prolonged moisture exposure. Plywood can delaminate, swell, and rot when wet, losing its structural integrity and promoting mold growth.
- Dimensional Stability: Moderate. Susceptible to swelling, warping, and cupping when exposed to humidity or water.
- Durability and Strength: Good when dry. Provides adequate strength for general subfloor use under dry conditions.
- Installation: Easy. Can be cut and fastened easily with common tools.
- Cost: Low. One of the most affordable subfloor options.
- Eco-Friendliness: Moderate. Wood is renewable.
OSB (Oriented Strand Board)
Standard OSB is another widely used subfloor material, made from compressed layers of wood strands bonded with waxes and synthetic resins.
- Water Resistance: Poor to Moderate. Similar to standard plywood, OSB is highly susceptible to swelling and edge degradation when exposed to moisture. Its edges are particularly vulnerable, often swelling excessively and creating unevenness (“edge swell”), which can telegraph through finished flooring. It’s prone to mold growth if wet.
- Dimensional Stability: Moderate. Known for significant swelling and delamination when wet, leading to an uneven subfloor.
- Durability and Strength: Good when dry. Provides sufficient strength for most residential applications when kept dry.
- Installation: Easy. Cuts and fastens readily with standard woodworking tools.
- Cost: Low. Often the least expensive subfloor option.
- Eco-Friendliness: Moderate. Made from fast-growing trees, but uses resins and waxes.
Practical Tips for Subfloor Installation
Even the most water-resistant material can fail if not installed correctly. Proper installation is crucial for maximizing the lifespan and performance of your subfloor, especially in guarding against moisture-related issues.
Installation Advice
- Acclimatization is Key: For wood-based subfloor materials (engineered wood, OSB, plywood), allow the panels to acclimatize to the indoor environment for at least 48-72 hours before installation. Stack them flat with spacers (stickers) to allow air circulation. This helps the material reach an equilibrium moisture content with the surrounding air, reducing the likelihood of significant expansion or contraction after installation.
- Proper Fastening Schedule: Follow the manufacturer’s recommendations for fastening. This typically involves using construction adhesive in a serpentine pattern between the subfloor and joists, combined with screws (recommended over nails for better pull-down and reduced squeaks). Fasteners should be placed every 6 inches (approx. 15 cm) along the edges and every 12 inches (approx. 30 cm) in the field of the panel. For cement board, use specialized corrosion-resistant screws.
- Leave Expansion Gaps: Do not butt subfloor panels tightly together. Leave a small gap, typically 1/8 inch (approx. 3 mm), between panels and at walls. This allows for slight expansion and contraction of the material due to changes in temperature and humidity, preventing buckling and warping. Some engineered panels feature tongue-and-groove edges that simplify this, but wall gaps are always necessary.
- Seal Joists and Penetrations: Before laying the subfloor, consider applying a bead of construction adhesive or a suitable sealant along the top of the joists to help create a more airtight and moisture-resistant barrier between the subfloor and the framing below. Seal any penetrations through the subfloor (e.g., plumbing pipes, electrical conduits) with appropriate sealants to prevent moisture or air infiltration.
- Moisture Barriers and Underlayments: In basements or areas directly over concrete slabs, a dedicated vapor barrier (e.g., polyethylene sheeting) should be installed beneath the subfloor material to prevent moisture wicking up from the concrete. For certain finished flooring types, an additional underlayment may be required on top of the subfloor for added moisture protection, sound dampening, or cushioning. Always check the finished flooring manufacturer’s specifications.
- Elevate in Flood-Prone Areas: In areas highly susceptible to flooding (e.g., basements in flood zones), consider installing a raised subfloor system using sleepers or specialized moisture-resistant pedestals to create an air gap beneath the subfloor. This allows for better ventilation and can help reduce damage in case of water intrusion.
- Protect During Construction: If your subfloor is installed before the building is fully enclosed and weather-tight, protect it from rain and excessive moisture with tarps or temporary coverings. Even “water-resistant” products are not designed for prolonged, direct exposure to the elements during the construction phase.
Maintenance and Repairs
- Promptly Address Spills and Leaks: The most effective maintenance tip is immediate action. Clean up spills and address any leaks (from plumbing, appliances, or roof) as quickly as possible. Even highly water-resistant materials can be overwhelmed by standing water over time.
- Ensure Good Ventilation: Proper ventilation in crawl spaces, basements, and throughout the home helps manage ambient humidity levels, which is crucial for the long-term health of your subfloor, especially for wood-based materials.
- Regular Inspections: Periodically inspect your subfloor (if accessible, e.g., in unfinished basements or crawl spaces) for signs of moisture, mold, rot, or pest activity. Look for discoloration, swelling, soft spots, or a musty odor.
- Repairing Damage:
- Minor Swelling/Edge Swell: For minor edge swell on OSB or plywood, sanding down the high spots can sometimes alleviate the issue, especially if a thick underlayment or finished floor is being installed.
- Localized Damage: If a small area of the subfloor is damaged by water (e.g., under a leaky toilet), it’s often possible to cut out the affected section using a circular saw (set to the correct depth to avoid joists) and replace it with a new piece of the same or a more water-resistant material. Ensure proper blocking is installed underneath the new patch for support.
- Widespread Damage: If large sections of the subfloor are soft, extensively molded, or structurally compromised due to prolonged water exposure, a full replacement of the affected panels is necessary. This is a more involved process and may require professional help.
- Identify and Fix the Source of Moisture: Before attempting any subfloor repair or replacement due to water damage, it is absolutely critical to identify and rectify the source of the moisture. Repairing the subfloor without fixing the leak will only lead to recurring problems.
Choosing the Best Subfloor
Selecting the “best” subfloor material isn’t a one-size-fits-all decision. It depends on a combination of factors specific to your project, budget, and the environment of your home.
Consider These Factors When Making Your Choice:
-
Location in the Home:
- High-Moisture Areas (Bathrooms, Laundry Rooms, Basements, Kitchens): For these zones, prioritizing maximum water resistance is crucial. Magnesium Oxide (MgO) panels and cement board are top contenders due to their inherent inorganic nature and excellent resistance to water and mold. Engineered wood panels with advanced moisture resistance are also a strong option here.
- Moderate Moisture Areas (Entryways, Mudrooms): Premium OSB, waterproofed plywood, and engineered wood panels offer good protection against spills and tracked-in moisture.
- Dry Areas (Bedrooms, Living Rooms, Hallways): While water resistance is always a benefit, standard plywood or OSB can be acceptable in these areas if the budget is a primary concern and there’s no foreseeable risk of significant water exposure. However, upgrading to a premium wood-based product still offers enhanced durability and peace of mind.
-
Finished Flooring Type:
- Tile: Cement board is a traditional and highly recommended underlayment for tile due to its rigidity and dimensional stability. MgO panels are also an excellent choice under tile. Engineered wood panels can work well if properly prepared and if the tile manufacturer allows for it.
- Hardwood/Laminate: These floors are sensitive to subfloor movement. Materials with excellent dimensional stability, such as MgO panels or high-quality engineered wood panels, will minimize the risk of buckling or gapping in the finished floor.
- Carpet/Vinyl: These are more forgiving of minor subfloor imperfections, but water resistance remains important to prevent mold and prolong the life of the flooring.
-
Budget:
- Higher Budget: Allows for premium options like Magnesium Oxide panels or top-tier engineered wood panels, offering the best performance and peace of mind, especially in critical areas.
- Mid-Range Budget: Premium OSB, waterproofed plywood, and standard cement board offer a good balance of cost and enhanced water resistance.
- Lower Budget: Standard plywood or OSB are the most economical choices, but they come with significant compromises in water resistance and long-term durability, making them less ideal for modern homes prioritizing resilience.
-
Installation Expertise/Labor Costs: Some materials, like cement board, can be more challenging and time-consuming to install due to their weight and cutting requirements, potentially increasing labor costs if you’re hiring professionals. Wood-based panels are generally easier and faster to install.
-
Long-Term Durability Goals: If you’re building a “forever home” or seeking maximum longevity and minimal maintenance, investing in the most water-resistant and durable subfloor materials (MgO, cement board, high-end engineered wood) will pay dividends over time by preventing costly repairs associated with water damage.
A Balanced Approach:
For many modern homes, a balanced approach might involve using different subfloor materials in different areas:
- MgO or Cement Board: For bathrooms, laundry rooms, and potentially kitchens.
- Engineered Wood Panels or Premium OSB/Waterproofed Plywood: For the rest of the main living areas.
- Standard Plywood/OSB: Only in very dry, low-risk areas if budget is extremely tight, but generally not recommended for overall modern home resilience.
FAQ
What is the difference between water resistant and waterproof subfloors?
The terms “water resistant” and “waterproof” are often used interchangeably, but there’s a crucial distinction.
- Water-resistant materials can withstand incidental exposure to moisture, such as spills or high humidity, for a limited time without significant damage or degradation. They might absorb some moisture but will not readily delaminate or lose structural integrity. Most enhanced wood-based subfloors (engineered wood, premium OSB, waterproofed plywood) fall into this category.
- Waterproof materials, on the other hand, are designed to prevent the passage of water through them and can withstand prolonged or even continuous exposure to water without being compromised. They do not absorb water or promote mold growth. Magnesium Oxide panels and cement board are examples of inherently waterproof or highly water-impervious materials, though proper sealing is still critical for a truly waterproof system (e.g., in a shower).
Can you install tile over any water resistant subfloor?
Not necessarily. While a subfloor might be water-resistant, its suitability for tile installation depends on several factors beyond just moisture protection:
- Rigidity and Deflection: Tile requires a very rigid and stable subfloor. Even if a material is water-resistant, if it has too much flex or bounce, the tile and grout can crack. Plywood and OSB, even premium versions, might require additional layers or specific thickness for tile.
- Dimensional Stability: Tile is unforgiving of subfloor movement. Materials with excellent dimensional stability (like cement board or MgO panels) are preferred because they won’t swell or contract significantly, preventing stress on the tile.
- Manufacturer’s Recommendations: Always consult the tile manufacturer’s guidelines regarding acceptable subfloor materials and preparation. They often specify minimum subfloor thicknesses and acceptable deflection rates.
- Underlayment: For most tile installations, a dedicated tile backer board (like cement board or a specialized uncoupling membrane) is typically installed over the structural subfloor, even if the subfloor itself is water-resistant. This provides an ideal bonding surface and helps manage movement.
How do you know if your subfloor needs replacing?
Several signs can indicate your subfloor needs attention or replacement:
- Soft or Spongy Spots: If you feel soft or bouncy areas when walking, especially near bathrooms, kitchens, or exterior walls, it’s a strong indicator of water damage and weakened material.
- Visible Water Stains or Discoloration: Dark stains, mildew, or mold growth on the subfloor (if visible from a basement or crawl space) are clear signs of moisture issues.
- Musty Odor: A persistent musty or earthy smell, especially in lower levels of the home, can signal hidden mold or rot in the subfloor.
- Cupping, Warping, or Swelling: If the finished floor is showing signs of buckling, cracks in grout, or if the subfloor itself is visibly uneven, it suggests dimensional instability due to moisture.
- Squeaks: While some squeaks are normal, excessive or worsening squeaks can indicate loose fasteners due to subfloor movement or deterioration.
- Pest Damage: Termite or carpenter ant infestations often target damp, decaying wood, so evidence of these pests near the subfloor is a red flag.
- Water Event: After a significant flood or major leak, even if the subfloor appears dry on the surface, it’s wise to inspect it for hidden damage or moisture absorption.
Are eco-friendly subfloor materials as strong as regular ones?
Yes, many eco-friendly or sustainably produced subfloor materials are just as strong, if not stronger, than conventional options.
- Magnesium Oxide (MgO) panels: Are a prime example. They are made from abundant minerals, require less energy in production than cement, and offer superior strength, fire resistance, and mold resistance.
- Engineered Wood Products: Many manufacturers are incorporating recycled wood content or using sustainably harvested timber (FSC-certified) while still producing high-performance, structurally sound panels. The enhanced resins in these products often contribute to their superior durability.
- The “eco-friendly” label usually refers to the source materials, manufacturing process, and indoor air quality (low VOCs), not necessarily a compromise on structural integrity. Always check specific product certifications and specifications to ensure they meet your performance requirements.
How can you protect your subfloor during construction?
Protecting your subfloor during the construction phase is vital, especially before the building is fully enclosed and weather-tight:
- Temporary Weather Protection: Cover exposed subfloor panels with heavy-duty tarps or plastic sheeting when rain or snow is expected. Secure the coverings to prevent them from blowing away.
- Prompt Enclosure: Prioritize getting the roof on and the exterior walls and windows installed as quickly as possible to provide permanent shelter.
- Elevated Storage: Store unused subfloor panels off the ground on stickers or pallets, especially on job sites, to prevent moisture absorption from the ground.
- Cleanliness: Keep the subfloor clean of debris, standing water, and mud. Dirt can trap moisture against the surface.
- Ventilation: Ensure adequate air circulation through the building during construction to help dry out any incidental moisture and prevent condensation.
- Manufacturer Guidelines: Follow any specific storage and protection recommendations provided by the subfloor material manufacturer. Some engineered products are specifically designed to withstand a certain amount of weather exposure during construction, but prolonged saturation should always be avoided.